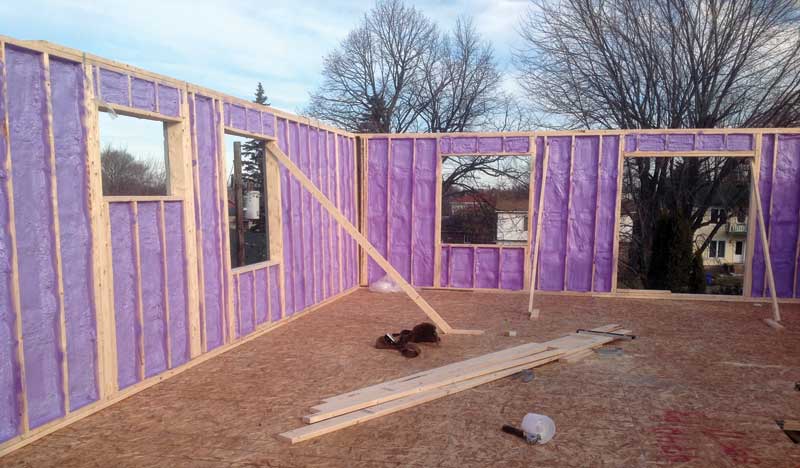
By Robert Cardinal, B.A.Sc., MPM
“Reducing the operational energy use and increasing durability should be the prime concerns of architects who wish to design and build ‘green’ buildings,” wrote John Straube, PhD, P.Eng., principal at RDH Building Science and RDH Building Science Labs. “I have reached this conclusion after spending years looking at actual building energy consumption, reviewing countless computer simulations, and being involved in numerous green building charrettes.
It has even been suggested that 80 per cent of a green architect’s concern should be directed toward reducing energy consumption during operation.” (For more, see “Why Energy Matters,” BSI-012 Insight, from www.buildingscience.com.)
While several Construction Canada articles have focused on energy efficiency in larger non-residential structures, there are important reasons why this aspect of going green is becoming more noticeable in the housing market. Beyond the larger environmental benefits, owners of high-performance homes experience savings in operational costs, and new product technologies are enabling these achievements to happen with a lower up-front cost.
To create high-performance homes, thermal performance is a critical component. While improving the efficiency of any residential project begins with the envelope, it is much more nuanced than simply adding higher amounts of insulation.
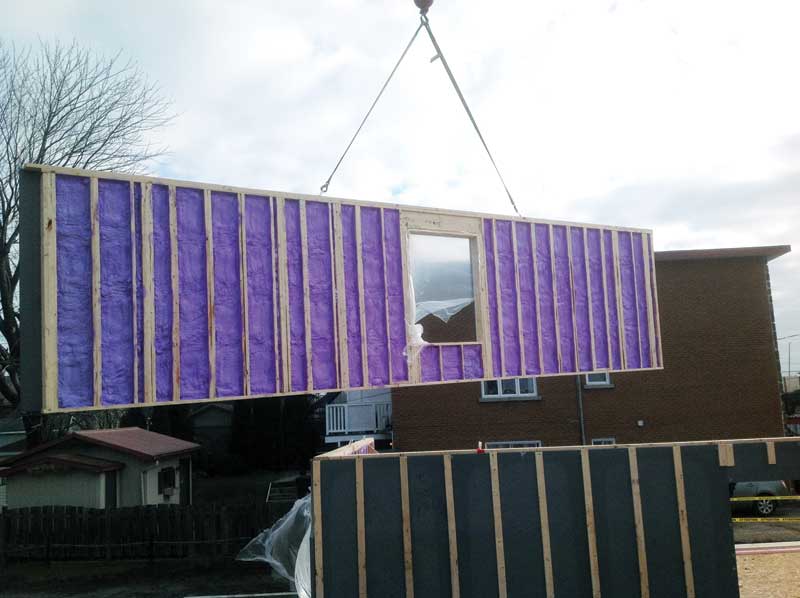
One solution involves wall assemblies that address thermal bridging, air leakage, and moisture control via a ‘systems’ approach. Instead of building wraps and seam tapes, some of these propriety systems employ a layered and integrated wall concept to make the envelope airtight. This helps address challenges with long-term durability, adhesion of sealing materials and methods, and the need to meet RSI value requirements with a relatively thin wall. Traditional adhesives and seam tapes can be sensitive to temperature, surface moisture, or contaminants (e.g. dust, soil) during installation; they can also be subjected to extreme changes in environment depending on where they are applied (i.e. interior versus exterior).
Integrated wall assemblies can meet or exceed new code requirements with a minimum nominal insulation RSI value of R-25 (i.e. RSI 4.4), up to R-45.8 (i.e. RSI 8.1) with 2×4 wood framing. This is possible by reducing the thickness of framing members (going from 2x6s to 2x4s), increasing the thickness of continuous exterior insulation (i.e. replacing the displaced framing with ci), and using materials with higher thermal resistance per unit thickness. The result is improved energy/cost efficiencies and durability, while maintaining the ease of installation of conventional methods. By using less wood framing than traditional practices, it can also reduce the amount of materials required.
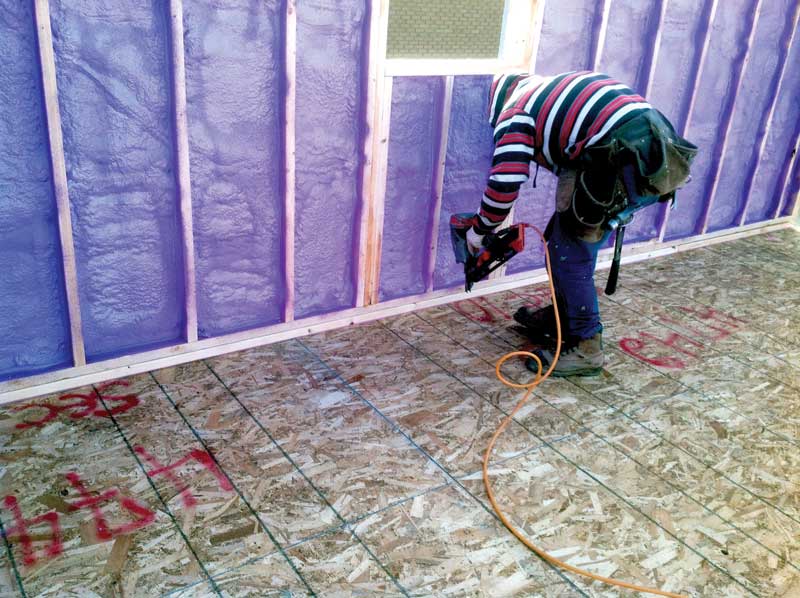
The need for change
Building codes and customer demands are constantly changing. In particular, the 2010 National Building Code of Canada (NBC) references CAN/ULC-S741, Standard for Air Barrier Materials−Specification, and CAN/ULC-S742, Standard for Air Barrier Assemblies−Specification. Similarly, the 2015 National Energy Code for Buildings (NECB) references and recognizes the suitability of CAN/ULC-S742 to the Canadian climate, making the distinction between it and test methods that do not assess performance under winter conditions. These requirements challenge manufacturers to find solutions without increasing the thickness of walls.
The application of building science was required to develop a high-performance wall assembly to meet these demands, necessitating continuous insulation (ci), and using an air/vapour barrier system without a conventional vapour or water-resistive barrier (WRB). These types of integrated systems assemble known products in a different way while maintaining traditional construction methods.
A consortium of stakeholders from the sprayed polyurethane foam (SPF) industry and the National Research Council (NRC) developed a procedure to evaluate the combined effect of heat loss due to conduction and air leakage through a wall system. This new wall energy rating (WER) was used to assess the thermal performance of 16 assemblies insulated and air-sealed using both common materials and methods, or the latest generation of open- or closed-cell SPF. The research also included walls having cavities partially or completely filled with sprayfoam insulation, and walls with or without penetrations, such as electrical boxes, ducts, pipes, and windows (Figure 1). The findings confirmed any wall assembly’s overall thermal performance was improved when air leakage is reduced.
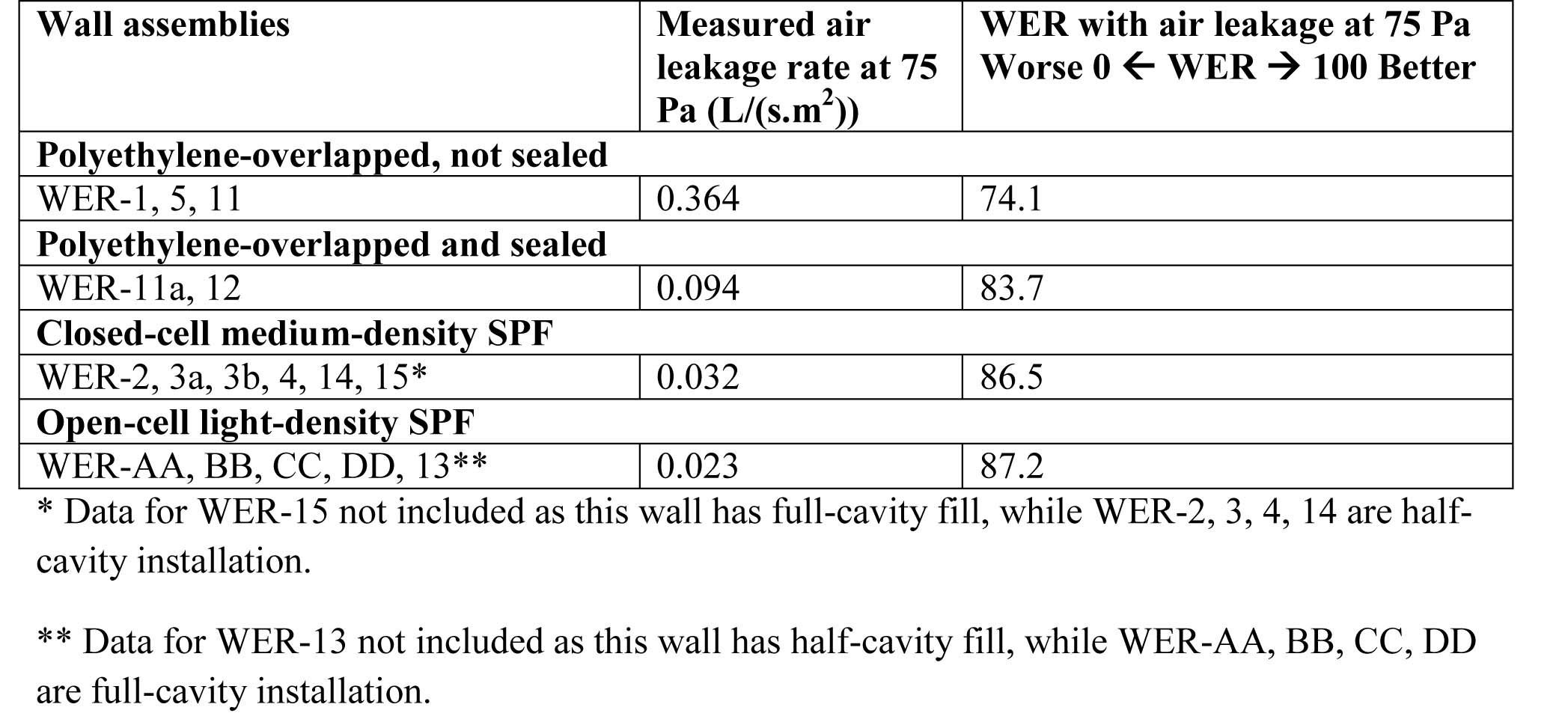