Creating better masonry with material compatibility
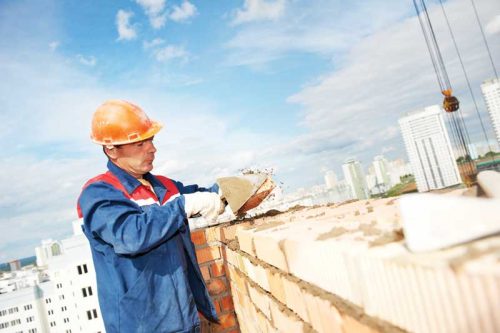
By Art Fox
The walls of today’s masonry buildings are becoming more complex than ever, with designs modified to meet new energy code requirements. This evolution means more components in walls than ever before, and they can all come from different manufacturers. One of a designer’s biggest challenges is deciding which materials will both meet the building’s needs and be compatible with one another. This article provides a general overview of how compatibility of various materials commonly used in masonry walls affects performance, either from a materials composition or functionality standpoint, and which should never be used together.
At its most basic level, a masonry cavity wall is simply two wythes of masonry separated by a space or cavity of varying dimensions. Bricks and stone are among the most ancient building materials, but until fairly recently, masonry walls were solid brick with no cavity between inner and outer wythes. Also called ‘barrier walls,’ these solid masonry walls were the only types that could be built due to limitations of material manufacturing and building technology. Barrier walls relied on sheer mass to provide structural strength, resistance to heat transfer, and water infiltration protection.
Masonry cavity walls were first built in North America in the late 1800s, but it was not until the late 1930s that this type of wall gained popularity, with wrought iron or masonry ties joining the two wythes together. As cavity walls became more common, designers started looking for ways to minimize the wall’s footprint, while creating taller, more energy-efficient, versatile buildings. To do this, they began modifying the basic design. High compressive-strength brick and mortar were created. Starting in the 1970s, a variety of continuous rigid insulation (RI) products were developed for use in the cavity. As wall design continued to evolve, many new products entered the market, including:
- multiple flashing membranes for the base of the wall;
- preformed corner boots and end dams;
- several types of drip edges and weep vents;
- air barriers with multiple water and vapour permeability characteristics;
- sealants with aggressive adhesion, high flexibility, and long lifecycles;
- thermal-break brick ties;
- air- and watertight fasteners; and
- products that serve as both RI and air barriers.
Designers are faced with the overwhelming challenge of choosing materials to specify a sustainable wall meeting today’s exacting energy codes while ensuring all the materials perform together, despite being made by a variety of manufacturers who do not test their products for compatibility with those of other companies.
Bricks and mortar
The bricks and mortar of the outer wythe must be matched to achieve the designer’s vision, and need to provide a combined compressive strength that supports the weight of the wall and any other materials attached to it. Bricks are locally manufactured, so appearance and strength will vary depending on the raw materials and each manufacturer’s processes. Standard clay and lightweight bricks using materials such as fly ash are available. One should consult a local brick manufacturer to determine the right types of specify for each job.
Unlike brick, mortar manufacturers strive to provide consistent characteristics no matter where the product is manufactured. While mortars are frequently ordered based on compression strength and flexibility, bond strength characteristics are more important criteria. This is because they work together to hold the masonry units in place while allowing wall flexion in response to lateral loads, or expansion and contraction from temperature swings.
Type M mortar has the highest compression strength (17,236 kPa [2500 psi] minimum) and is extremely durable—making it the ideal mortar for stone. It is usually recommended for walls bearing heavy loads such as masonry below grade or in contact with the earth. Type S also has high compressive strength (12,410 kPa [1800 psi]), plus high tensile bond strength and maximum flexural strength to resist wind, soil pressure, and earthquakes. It is usually specified for use at or below grade. Types M and S should be considered incompatible with brick, but are fine for concrete masonry units (CMUs).
Type N mortar has a medium compressive strength (5171 kPa [750 psi]) and is used for above-grade brick walls and other masonry structures exposed to severe weather. Finally, Type O has a low compressive strength (2413 kPa [350 psi]) and is only for use on interior, non-load-bearing brick walls. The bottom line is many masonry building envelopes require several different mortar types—which must be compatible with the brick and other masonry products, and with the structural and weather conditions to which they will be subject.