Can we future-proof our buildings?
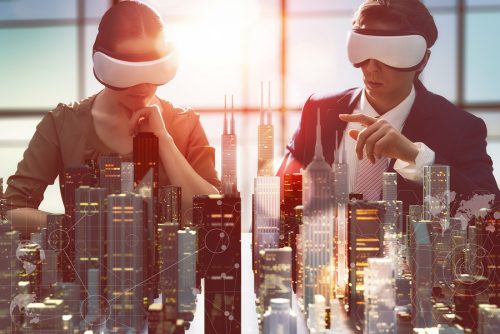
Photo © BigStockPhoto
By Brian Burton
Construction professionals and consultants deliberate over the past, present, and future of Canada’s built environment for a living. The topic is not just an academic debate—it is necessary to prepare for the future by applying lessons learned from the past. The concept of ‘future-proofing’ actually describes what we would normally term a ‘systematic approach’ to mitigating risk. In the business world, use of risk mitigation actually predates the industrial revolution; its basic premise has been employed very effectively for centuries.
Over time, we have digitized the process and now refer to it as ‘predictive analysis,’ in reference to the creation of computerized decision-making tools that utilize accumulated historical data to create probability models of the future. Corporations and governments harness demographic and psychographic database information to generate models for quantifying consumer behavior and optimizing the impact of their marketing strategies.
The technique has been successfully used by the marketing, retailing, information technology (IT), and industrial design sectors to streamline decision-making, modify branding, and mitigate risk. Faster computers, a voracious marketplace, and the need to distinguish one’s self from competitors have made this kind of analysis advantageous on an individual basis. On an industry-wide basis, however, it enables improved efficiency and better results that can stand the test of time. So what does this all mean for designing and constructing buildings?
Why rethinking Canada’s built environment is so difficult
The country’s design/construction sector has been somewhat slow in considering how best to anticipate and prepare for the future in improving work processes. However, this is understandable given most buildings are ‘one-off’ prototypes—these are not traditional end-products built on assembly lines using robotics, so there is no ‘economy of scale’ in the usual sense of the term. Additionally, the building creation process on the whole is not mechanized or automated; since it requires considerable skill, judgment, and expertise to accomplish, any desired change in approach or sequencing takes both training and time.
There are other reasons rethinking construction processes is difficult. For example, buildings are characterized by inherent immobility and cannot be easily relocated or reoriented. When occupied, any major modification, repair, or adaptation activity can be a costly exercise. Further, buildings are extremely complex—a situation compounded by their major components and systems degrading at different rates. (Unlike other industries, there is also no cost and time benefit of standardized replaceable components.)
The built environment is prone to inherent deficiencies due to factors such as compression, overlap, and concurrency. Buildings must also absorb the costs associated with the high degree of regulation and social responsibility, along with additional costs incurred because of the extended gestation period required for design, construction, and commissioning. Practitioners are required to incorporate the high expectations of clients, end-users, and/or occupants in terms of health, safety, and comfort, as well as durability and sustainability, performance characteristics, maintainability, and serviceability.
The industry itself has been historically resistant to large-scale innovation and change. That is, innovation has been incremental because buildings are simply too simply expensive to undertake any systematic or radical innovations on any one specific building design or project. This author would also argue the industry has been disadvantaged by the surprisingly small investment in formal measures designed to improve quality and the lack of truly effective representation at senior levels of the provincial and federal governments.
Why future-proofing is important
Buildings are long-term investments with an intrinsic value far in excess of the sum of its parts. They collectively serve as a vast storehouse of embedded energy; in their design, construction, and ongoing reuse we have made extraordinarily effective use of what would normally be considered materials of low intrinsic value.
Any attempt to prepare buildings for the future will have to acknowledge the same characteristics mentioned that make buildings and the industry unique and special in doing so. Enabling the built environment to be ready for the future is almost certainly a collective challenge that will eventually need to be tackled by the revision mechanisms built into our National Building Code of Canada (NBC). Historically, we have used our model code to address concerns about the safety, well-being, and productivity of the occupants and/or our building stock itself. This approach would not have to be modified to address any specific concerns any about the future.
The biggest risk to our built environment are those we will have difficulty in anticipating or controlling—obsolescence in one form or another is undoubtedly at the top of the list. One dire consequence is a failure of buildings to provide essential services.
Although predictive analysis has been reasonably successful in predicting and quantifying buyer behaviour, it is unlikely it could correlate the numerous factors involved in the buildings themselves and occupant interaction. Even a simplistic approach would have to include thermal comfort, indoor air quality (IAQ) and ventilation, acoustics, daylighting, security, communications, and a degree of control over the indoor environment. The same limitations would probably apply with regard to anticipating evolving social patterns, demographics, and user expectations of the indoor environment.
It would also have to consider the rapidly changing demographics of the Canadian population—the number of citizens over the age of 65 has doubled since 1982. By 2030, most baby boomers will be seniors; by 2056, one-quarter of all Canadians will be older than 65. What does this mean for our design practices? For our buildings? (Perhaps code officials should require a registered mandatory emergency plan for buildings over 12 storeys in height, taking mobility and accessibility into account.)
The other implications of obsolescence of our building stock are mostly related to functional, financial, technological, legal, and esthetic issues that we can probably control or influence to a certain degree. Other areas warranting consideration include critical shortages of materials/resources and labour, environmental concerns, and minimizing our exposure to the risk of catastrophic events and their subsequent consequences. Ensuring our buildings are future-proofed is imperative—it warrants our collective attention and action.
Forging the future
Anecdotal evidence suggested the design/construction industry is not investing enough of its revenues back into research and design, and not coincidentally, there are too few government incentives encouraging this aspect. The aerospace and resource sectors put in vast amounts of money in R&D, while construction invests a negligible amount relative to the size and strength of the industry.
Although we quite likely possess the expertise in building science considered necessary to improve overall building performance, we typically fail to systematically apply the knowledge. To ameliorate this, construction codes could be modified to ensure design reviews by building scientists are mandatory. Local building departments should also be more vigilant in enforcing minimum code requirements (including those for durability); a requirement for mandatory building commissioning prior to receiving an occupancy permit is also a good idea.
Regardless, the industry must adopt a proactive stance with regard to investing in research and development or overall quality, and ultimately building sustainability, will suffer as a result.
Brian Burton has written or co-authored several feature articles for Construction Canada, ranging from climate change’s effect on the built environment and the revitalization of Toronto’s Maple Leaf Gardens to specifying seismic restraints. He also publishes pieces on his site. Burton can be reached at blueblade49@gmail.com.