Using brick veneer and metal studs for strong walls
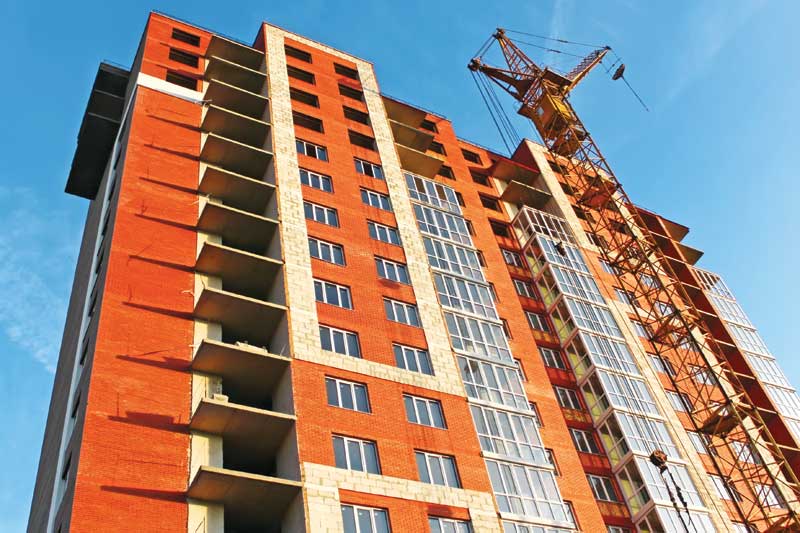
By Michael Gurevich
The brick veneer/metal stud (BV/MS) backup exterior wall assembly was invented in New England in the 1970s. This type of system was formed to substitute the more expansive concrete masonry unit (CMU) backup wall because it is installed much more quickly. Now, new innovations have improved the assembly further.
The original design had contained fibreglass insulation within the stud space, and exterior/interior gypsum board sheathing on each side of the studs. The outside face of the stud backup system had #15 felt installed over it to protect the exterior gypsum board sheathing from moisture. Various different masonry ties were developed to anchor the brick veneer to the studs. As the system was new in the 1970s, no real standards were developed for the design of this wall system.
Building code and industry standards
To help compensate for the lack of standards, the Brick Industry Association (BIA) revised its Technical Notes on Brick Construction #28B, Brick Veneer Steel Stud Walls, in February 1987. It recommends the maximum deflection for the steel stud backup, when considered alone at full lateral design load, be L/600 to L/700.The minimum air space had been increased to 51 mm (2 in.), so ties must be spaced closer.
There should be one tie for each 0.18 m2 (2 sf) of wall area. This is because 25-mm (1-in) air spaces could be bridged by mortar drops, and moisture could migrate inside of the building.
In 2008, The Masonry Society (TMS) 402-08/American Concrete Institute (ACI) 530-08/American Society of Civil Engineers (ASCE) 5-08, Building Code Requirements and Specification for Masonry Structures and Related Commentaries, issued a new chapter, ‘Anchored Veneer,’ with requirements for brick veneer with metal stud backup exterior wall systems. The chapter stated:
If anchored veneer with a backing of cold-formed steel framing exceeds the height of 9.1 m (30 ft) above the noncombustible foundation, the weight of the veneer shall be supported by noncombustible construction for each storey above the height limit of 9.1 m. Thus, continuous steel shelf angle should be provided at each floor above the limit to support the brick veneer.
Thermal bridging at studs
The exterior walls were originally designed with fibreglass batt insulation located between the metal studs, with no insulation over the exterior face of the studs. This batt insulation had a kraft paper or foil facing the building interior that was intended to act as a vapour barrier in colder climates. During the winter in these regions, the exterior flange of the stud was exposed to the cold air behind the brick veneer. The interior flange of the same stud was exposed to the interior warm air, which caused thermal bridging at the metal stud. Thus, condensation could form at the cold surface of the exterior flange. This moisture could potentially contribute to mildew development inside the wall system.
One of the weak points in the BV/MS exterior wall system is the masonry ties, which should anchor the brick veneer to the metal studs. All masonry ties should be connected to the steel studs with screws. Approximately two threads of the screw hold it in the 16-gage outside flange of the metal stud. Thermal bridging can cause condensation moisture at the cold, inside face of this outside flange of the stud. Therefore, rust or a galvanic cell reaction could develop at the juncture between the screw and the stud.
After a few years, this means the connection between the screw and the stud could deteriorate and become loose, allowing the masonry tie and brick veneer to follow suit. Ultimately, this leads to movement and cracks in the horizontal (bed) joints of the brick veneer. Cracks can then lead to water penetration through the brick veneer, which could provide an avenue for moisture to get inside the building.
Insulation moving to exterior side of the wall
The 2000 International Building Code (IBC), specifically the ‘Energy Conservation’ section, included provisions to help eliminate thermal bridging at metal stud locations. The new provision has a minimum design requirement of exterior sheathing on the outside face of the metal studs with rigid insulation containing an R-value of at least R-3.
Consequently, 19 mm (3⁄4 in.) of extruded polystyrene (XPS) insulation board with an R-value of R-3.75 should be installed on the outside face of the metal studs, eliminating thermal bridging at this area. This could also avoid the possibility of screw-to-metal-stud connection deterioration. Good thermal performance means having the entire insulation located at the outside face of the studs. No batt insulation would be required.
At the beginning of the 21st century, new industry standards to locate the 51 mm (2 in.) of XPS insulation board (R-10) on the outside face of the studs were developed. In this case, the vapour barrier would be located between the exterior paperless gypsum board sheathing and the insulation board, and the vapour barrier would act as an air barrier and a moisture barrier at the same place. It is ideal to specify the 1-mm (40-mil) peel-and-stick membrane, which should be sandwiched between the exterior gypsum board sheathing and the insulation board. This exterior wall system works well for cold and hot climates. Condensation analysis should help verify the proper location of the vapour barrier in the wall system.