Accelerated corrosion testing
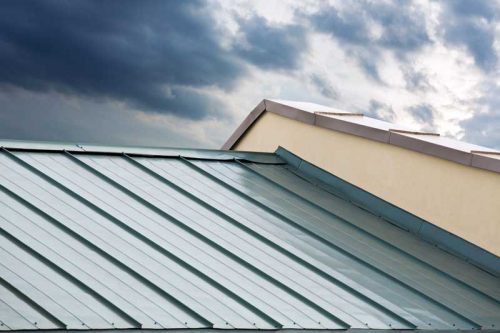
By Gary Dallin
The purpose of an accelerated corrosion test is to duplicate the field corrosion performance of a building material in the laboratory. This provides scientists and engineers with a means of quickly developing new products. For many years, the salt spray test has been used extensively for this purpose by researchers in the evaluation of new metallic coatings, paint coatings, types of chemical treatments, and paint pretreatments for use with metallic-coated steel sheet products.
For an accelerated corrosion test to be truly useful, the results must correlate with performance in the real world—something that has never been demonstrated with the salt spray test. This has led many researchers to conclude that the test is irrelevant, and should be discontinued. However, the results of salt spray testing are still extensively used in product literature, customer specifications, product data sheets, and technical literature.
Typical data shows the ‘life’ of a given type of coating, the benefits of new paint systems, and the salt spray requirements for the acceptance by an end customer of an alternative product. Therefore, it seems virtually impossible to stop using the salt spray test at this time. In fact, there are so many specifications that require a product to exhibit a specified number of ‘hours to failure’ in the salt spray test, that any change to the test or its elimination is improbable.
Clearly, any push to eliminate it would require architects and specification writers to accept some alternate. The corrosion performance of different products has been compared using this test for so long it would be difficult for researchers to lack salt spray test results when presenting performance data to a potential end user. Salt spray testing, while severe, is a good screening test because results can be generated in a timely manner and ‘poor contenders’ can be eliminated early on in the evaluation process.
Salt spray test procedure
The salt spray test procedure involves the spraying of a salt solution onto test samples. This is done inside a temperature-controlled chamber. The solution is a five per cent salt (i.e. sodium chloride [NaCl]) solution. The samples under test are inserted into the chamber, following which the salt-containing solution is sprayed as a very fine fog mist over the samples. The temperature within the chamber is maintained at a constant level. Since the spray is continuous, the samples are constantly wet, and therefore, constantly subject to corrosion. Through the years, there have been some new twists added to better simulate special environmental conditions, but the most common procedure in North America is the test described in ASTM B117, Standard Practice for Operating Salt Spray (Fog) Apparatus.
In summary, the procedure details are:
- wooden or plastic racks contained in the salt fog chamber (as large as 0.9 m high by 0.9 m deep by 1.5 m wide
[3 x 3 x 5 ft ]); - samples are placed on the wooden or plastic rack at a small tilt angle;
- five per cent NaCl in tap water pumped from a reservoir to spray nozzles;
- solution mixed with humidified compressed air at nozzles;
- compressed air atomizes NaCl solution into a fog at the nozzles; and
- heaters to maintain a 35-C (95-F) cabinet temperature.
The test duration can be anywhere from 24 to more than 1000 hours, depending on the material. Within the chamber, the samples are rotated frequently so all the samples are exposed as uniformly as possible to the salt spray mist.
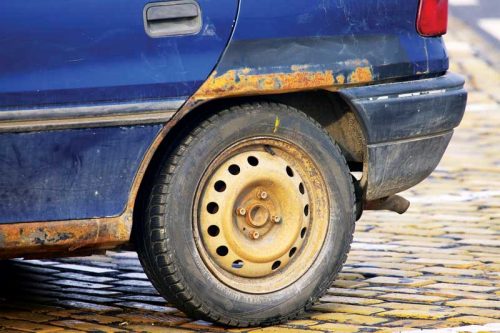
When the process is used for testing metallic-coated steel sheet, the corrosion performance is rated by the number of hours until:
- rusting of the steel is first evident;
- five per cent of the surface area is rusted; and
- 10 per cent of the surface area is rusted.
The onset of red rust on a sample of galvanized sheet, for example, means the coating has been consumed by the corrosion reaction, and the corrosion of the base steel is beginning. There is no single best performance criterion. It simply depends on what the user defines as failure.
When the salt spray test is used to rate the performance of paint pretreatments, paint primers, and/or topcoats, the normal rating schemes involve:
- measuring the width of paint undercutting either along a scribed line, through the paint, or at a sheared edge after 250, 500, or 750 hours of exposure in the test chamber; or
- measuring the amount of paint blistering on the surfaces of the painted steel panel in 250, 500, or 750 hours.
There are other ways to define failure, but the above two are very common. Since the salt spray test does not involve any exposure to ultraviolet light, paint fading and chalking are not measured in this test. A standard has been developed for modified salt spray testing—ASTM G85, Standard Practice for Modified Salt Spray (Fog) Testing, has several modifications involving cyclic additions of acid and SO2. This standard is not as widely used as ASTM B117. Method A5 of G85 has been found by some producers to rank materials and coatings similar to what is witnessed in actual service.