Producing quality polished concrete floor slabs
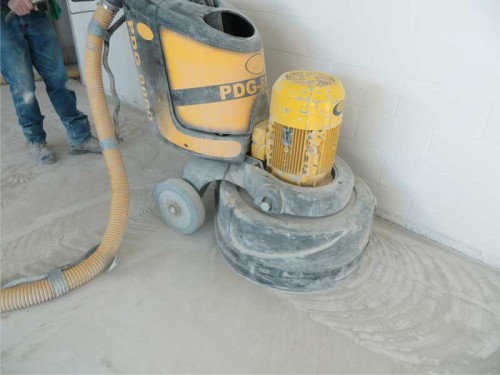
By Paul Jeffs
Producing a good quality polished concrete floor may appear to be a relatively simple task. (This article only discusses polishing of newly constructed floor slabs. Existing slabs can be polished, but the esthetic quality will be primarily dependent on the already existing near surface conditions with regard to the presence and extent of defects and, of course, the skills and techniques of the polished concrete contractor. When the term polished concrete is used it refers to the practices of grinding, honing, and polishing). Certainly, when conditions and circumstances are favourable during the various phases of construction, highly durable, attractive surfaces and finishes can be achieved that require very little maintenance. Unfortunately, the achievement of these features when conditions and circumstances are not favourable can be extremely complex and sometimes considerably more costly.
To understand the many complexities, one should examine the members of the project team, how they can influence the quality of a polished concrete floor surface, and their typical roles, responsibilities, objectives, and expectations. Then, one should examine the factors adversely or beneficially influencing the achievement of each member’s objectives, as well as how these factors can vary considerably from project to project. (Unfortunately, it has been this author’s experience that, prior to a project start-up, each team member has varying levels of awareness of the factors that can inadvertently cause problems and sometimes result in conflict. Team members are therefore often unprepared for the consequences when conditions and circumstances turn out to be unfavourable.)
One should also examine the various problems that can sometimes result when conditions and circumstances are not conducive to the achievement of an acceptable finish. However, the term ‘polished concrete’ should first be defined and explained.
What is polished concrete?
Canada’s Concrete Floor Contractors Association (CFCA) defines polished concrete as:
a sustainable exposed concrete surface finish obtained through intensive diamond grinding incorporating a densifying liquid hardener. During the polishing process, cement paste is removed from the surface of the concrete which may expose underlying concrete fine and coarse aggregates.
However, polished concrete practices have evolved over the last decade and there are now numerous proprietary systems available offering similar esthetic effects, but using different techniques and/or materials to achieve the surface finish. In recognition of this evolution, the Concrete Polishing Association of America (CPAA) has published a more comprehensive definition. It states polished concrete is:
The act of changing a concrete floor surface, with or without aggregate exposure, until the desired level of finished gloss is achieved by using one of the listed classifications; Bonded Abrasive Polished Concrete, Burnished Concrete, or Hybrid Polished Concrete.
CPAA then goes on to define bonded abrasive polished concrete as being:
The multi-step operation of mechanically grinding, honing, and polishing a concrete floor surface with bonded abrasives to cut a concrete floor surface and to refine each cut to the maximum potential to achieve a specified level of finished gloss.
CPAA concludes its definition with the statement—this system yields the most durable finish and requires the least maintenance. Interestingly, unlike CFCA, the U.S. group does not refer to the use of a densifier within its definitions.
The final surface finish may be a natural colour, or it may be enhanced by application of dyes, tints, or stains during multi-step operations. This information is missing from both organizations’ definitions. Alternatively, an integrally mixed pigment may be included during the concrete batching operations, or a pigmented dry-shake hardener can be applied during the finishing operations.
There is rarely consensus within the polished concrete industry regarding the best materials and techniques. However, there is a general agreement a multi-step, mechanical operation involving cutting and refining the surface is essential for the achievement of a high-quality, durable finish.
Each step cuts progressively finer microscopic peaks and valleys and should continue until the abrasive under use can no longer refine the appearance. The number of steps and the specific abrasive used during each step will be determined by the desired finish.
In the past, a major issue has arisen regarding accurate communication with the polished concrete contractor as to the desired finish, and expectation of esthetic quality and uniformity of appearance. In an attempt to provide owners and specifiers with standardized terminology, both CFCA and CPAA have published classifications for the degree of aggregate exposure and finished gloss. Unfortunately, although similar, each classification is different (Figure 1).
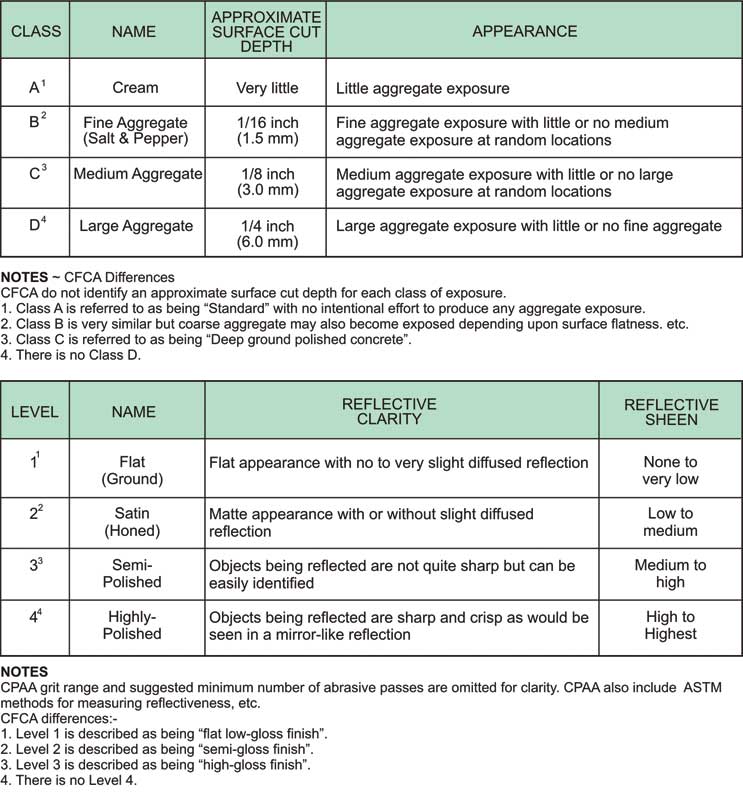