What are Canada’s next green leaps?
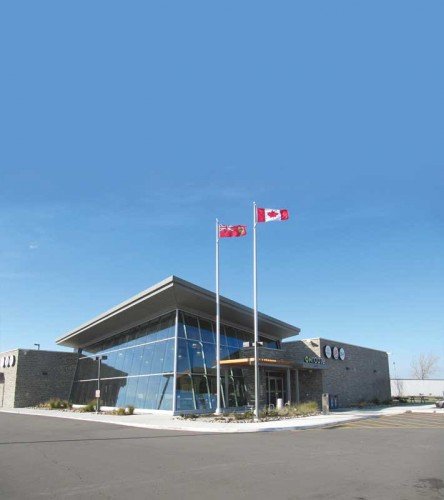
By Bob Marshall, P.Eng., BDS, LEED AP
In October, Canada will host the U.S. Green Building Council’s (USGBC’s) Greenbuild show for the first time when the event comes to Toronto. Given the country’s burgeoning community of sustainability advocates, it seems fitting there will be a dedicated stream of educational sessions highlighting Canadian projects and strategies.
Greenbuild 2011’s theme is “next”—as in, what are the next big leaps for sustainable design? To help ascertain the answer, the Canada Green Building Council (CaGBC) appointed this author to chair a team to work through a three-stage selection process established by USGBC to evaluate the abstracts.
From over 1200 submitted abstracts, seven sessions were selected for Canadian content. They cover diverse topics, including:
- innovative building commissioning;
- using wood for mid-rise buildings;
- solutions for university projects; and
- understanding new ways of thinking for central business districts, neighbourhoods, and mixed-use developments.
Clearly, multiple sustainable practices are being integrated across all key sectors—this green transformation will only increase over the next decade. Fortunately, many of the solutions to be presented in the Greenbuild sessions are already being implemented.
For example, reducing energy intensity is critical for lowering emissions and energy cost savings during the operational stage of buildings. In the 2012 update to USGBC’s Leadership in Energy and Environmental Design (LEED) rating program, there will be a new category for measuring energy performance, which addresses one of the more controversial issues surrounding USGBC’s LEED rating system.
In the current version of LEED, many points can be achieved from energy modelling based on design, rather than actual operational energy performance. Canada has been more rigorous with energy performance requirements and measured performance. Therefore, the educational solutions already put into practice in this country will be of great interest to the expected 25,000 attendees at Greenbuild. This article touches on some of the related topics, specifically building envelope commissioning and wood use. (For more information on this author’s approach to sustainable design, see the May 2010 Construction Canada article, “Time for Holistic Thinking-Integrated building energy performance solutions.” Visit www.constructioncanada.net and select “Archives.”)
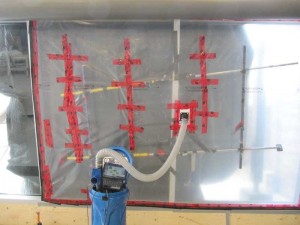
Institutional green buildings
Innovative measures being implemented in institutional buildings will be featured in the session, “Canadian Building Commissioning: How does it impact your Igloo?,” presented by this author, along with Andrew Cunningham (EllisDon) and Michael Tiffe (TAB Mechanical). While there are not many igloos in Ontario, the province does boast the most LEED buildings in Canada.
Infrastructure Ontario is managing $14 billion in green construction projects, most of which are institutional. Landmark LEED candidate buildings include 20 new 400-series highway travel centres (pictured at left), which are part of a $300-million government/industry renewal project. For this work, building envelope commissioning practices have been implemented.
The act of commissioning covers the envelope, vertical/horizontal transportation, and electrical, mechanical, and control systems. For the travel centres, commissioning work has been implemented on both the steel and wood-frame buildings; it has included review of details, construction quality field reviews, and air and water tests.
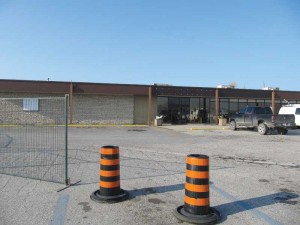
The building commissioning process is recognized by LEED 2009 as a possible exemplary credit where the practices contribute to tighter buildings that improve energy efficiency, comfort from drafts, and reduce the risk of condensation buildup. There is also the new Canadian Standards Association (CSA) Z320-11, Building Commissioning, which covers the systematic process to verify and document various systems during the facility’s design, construction, testing, and operation stages. This standard is not yet mandatory for new construction under the codes, but benefits of a tighter, more thermally efficient building envelope can be realized by reducing or eliminating some heating equipment.
Constructible details
For the highway projects, one challenge involved creating constructible details at changes in cladding and roof/wall interfaces. This task was exacerbated by the multiple consultants involved—some reviewed the roof, others reviewed the wall, but seemingly constructability at the roof/wall interface was a challenge that needed to be overcome.
Fortunately, at the onsite pre-construction meeting with the architect, general contractor, building science consultant, and trades, details were marked up on a projected image before construction, thereby minimizing the need for rework. Subsequent phases of the project allowed for the roof/wall details to be made more easily constructible and improved in terms of thermal performance.
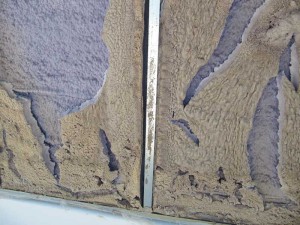
Construction quality reviews
Even with constructible details, construction quality reviews are required to verify the general contractor and trades understand the intended performance and can install the various components of an assembly in the proper sequence. This attention to detail is important especially for through-wall flashings and membranes that cannot be easily changed without costly rework.
Medium-density sprayed polyurethane foam (SPF) is increasingly being used to improve the energy efficiency of green buildings. This material provides both thermal protection and an air barrier between the many building penetrations (i.e. windows, doors, and ducts). It is extremely important interfaces between penetrations and different substrates be provided with membranes to bridge gaps and provide continuity of the air barrier system.
Underwriters Laboratories of Canada (CAN/ULC) S705.1 and S705.2, Standard for Thermal Insulation: Spray Applied Rigid Polyurethane Foam–Medium Density, are referenced in the National Building Code of Canada (NBC) as the material and installers’ responsibility. However, mandatory quality checks by third parties are not spelled out in the code, so it is important quality control reviews be specified during construction. On several LEED buildings, this author has found faulty sprayfoam installations that have had to be removed and replaced. The material can be a suitable choice, but only when correctly specified, installed, and reviewed during construction.
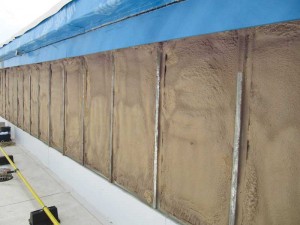
Commissioning and documentation
Commissioning documentation is required at completion. In addition to the commissioning manual, it consists of maintenance and data manuals, system operator manuals, contract documents, and record drawings. As this work is intended to be re-applied throughout the facility’s life, these documents can be used in the creation of a re-commissioning manual.
Part of the onsite commissioning should also include testing of window/wall interfaces. Envelope commissioning tests for windows and doors are important to be spelled out in the contract documents. The pass criteria should be reflective of the assemblies’ expected exposure. For example, in the case of sloped outward windows not protected by large canopies, the air and water pass criteria should be higher than with vertical recessed windows.
In some projects, this author has found localized sprayfoam, specified to fill the gaps, was not uniformly installed, serving as a source of air leakage and water infiltration. When this is the case, a recess on the interior side of the foam between the frame and opening can be made so a compatible interior sealant can be applied. (Ideally, this sealant would be free of volatile organic compounds [VOCs] so indoor air quality [IAQ] is not impacted.)
Residential green buildings
Canadian seminars at Greenbuild will also deal with aspects of residential design and construction. Wood-frame multi-family mid-rises are now being built. In British Columbia, there are about 60 of these buildings, five or six storeys tall, under construction. These sorts of projects will likely be increasing throughout the country as urban populations grow. At Greenbuild, this topic will be explored in “Canada Leads the Way with Codes for More Affordable, Renewable Wood Mid-rise Green Buildings” (YL 14) session—conducted by Russ Thomas (National Research Council Institute for Research in Construction [NRC-IRC]), Michael Green-McFarlane (Biggar Architecture+Design), and Sukh Hohal-Wood (WoodWorks BC).