Plaza Deck Restoration: Principles of drainage and waterproofing
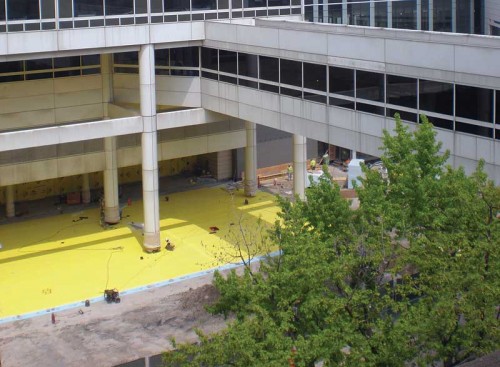
By Stacy Byrd, LEED AP
Plaza deck waterproofing typically requires replacement at some point during the building’s life. Restoration of the waterproofing system over occupied space poses many challenges, both in design and construction. Typically, plaza decks now being subject to restoration were constructed many years ago and do not include subsurface drainage or adequate deck slope at the waterproofing membrane level. Correcting these deficiencies can result in increased plaza deck thickness and dead loads.
The designer is often faced with the building not being constructed exactly per plans and specifications because of changes implemented during the construction process. These ‘as-built’ changes may or may not have been documented, or the documentation may no longer exist. This makes it especially challenging for consultants to determine causes of the water ingress and develop plans to remediate problems at the plaza area without doing extensive and expensive intrusive investigations.
Inspection and design challenges
If there is a leak in the plaza deck, the waterproofing membrane is buried under reinforced concrete, heavy pavers, pavement, or soil with plantings. Their removal and replacement represents a significant cost to the building owner. With waterproofing membrane restoration, the designer must address related issues with the existing building components and provide installation details that take into account the limitations posed by the existing conditions and building occupancy. These issues typically include:
- structural concrete deck condition;
- structural slab load capacity;
- drainage slope at both the wearing course and membrane level;
- overall assembly depth;
- flashing heights and detailing at perimeter conditions; and
- waterproofing membrane selection.
Exploratory openings are almost always required to determine the configuration and condition of the plaza assembly materials, including the concrete deck’s condition. These openings can also provide data on existing drainage patterns. One should select locations for the openings based on:
- known water ingress;
- paving surface deterioration;
- proximity to drains; and
- anticipated low-drainage areas.
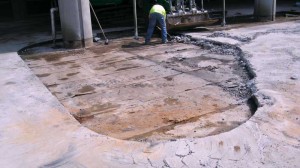
However, it should be noted these openings represent only a small area of the deck, and the conditions discovered by exploratory openings should only be relied on to conclude a ‘general’ estimate of repair requirements. Typically, the plaza deck assembly’s actual condition and the extent of deterioration, if any, will not be known with certainty until the remedial construction operations. Therefore, the construction documents should incorporate various repair work that may be required to restore the structural deck condition. To protect the owner, prices for such repairs should be incorporated into the contract bid documents. (This is a project by project ‘cost’ issue based on the existing construction of the building and the anticipated repairs as related to the condition and construction of the structure. For example, the owner and contractor, even with up-front investigation work, may not know the extent to which the concrete deck has deteriorated and needs to be repaired before a new waterproofing membrane can be installed. In this case, the contractor would be directed to provide a unit price for deck repair at the time of bid. The contractor can also place some conditions on the unit price to protect his interest as well. However, at the least the owner gets a bid that tries to cover all of the assumed repairs based on the building’s existing construction).
Many investigations have revealed the deterioration and subsequent water ingress was a result of water trapped within the plaza deck assembly directly atop the waterproofing membrane and the project did not incorporate a subsurface drainage layer. Therefore, this article focuses on subsurface drainage and selecting and installing a proper waterproofing system for plaza deck restoration.
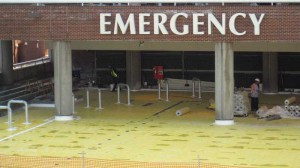
Positive drainage
A good plaza deck waterproofing design incorporates drainage at both the deck wearing surface and subsurface at the waterproofing membrane level. Many plaza deck waterproofing failures are a result of the deck surface not sloped to properly drain. It is essential to provide drainage at the waterproofing membrane level as a component of the design. This ensures water that infiltrates the deck assembly will flow to the drains and minimize freeze-thaw-heaving and deterioration of the wearing surface. Additionally, if the deck-wearing surface is continuous, it should be sloped to internal drains or off the slab’s edge.
Drainage at both levels can be achieved with ‘two-tiered’ drains or by separate surface and subsurface drains. Good drainage slope at the membrane level will minimize water ponding, reduce deterioration of the membrane, minimize hydrostatic pressure on the membrane, and decrease the potential for deterioration of other plaza deck components from prolonged exposure to moisture.
Wearing course drainage
Plaza designs can incorporate one or several materials in different locations as the wearing course. These include continuous materials such as reinforced concrete, or unit materials such as precast concrete pavers, brick, or stone. Additionally, the precast concrete pavers can be installed either in an open- or closed-joint configuration. The former indicates the pavers are suspended on support pedestals which provide a gap between each adjacent paver and an air space beneath the paver––separating it from the assembly materials underneath. The latter indicates the pavers are installed on a cementitious grout bed with the joints between adjacent pavers filled with grout.
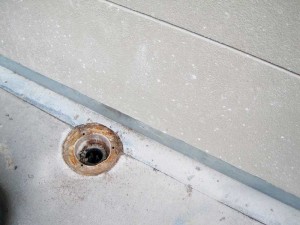
Pavers on pedestals generally provide the best means to promote drainage at both the wearing course level and under the wearing course. Pedestals suspend the pavers up and out of the water on the membrane, and provide an air space underneath the plaza surface so water can flow freely to a drain. Paver-on-pedestal systems also allow easy removal and reinstallation of the wearing course for inspection and maintenance of the drains and waterproofing membrane. However, pedestals are not suitable for bricks and irregular natural stone.
An advantage offered by open-joint paver systems is the wearing surface can be constructed level for improved plaza use and esthetics. Typically, there is no need to use surface drains; therefore, deck drains can be concealed below the pavers. However, pavers on pedestals have their disadvantages. Without proper installation, the pavers can move or shift when loaded, consequently becoming a hazard. Additionally, paver-on-pedestal systems have limited load-bearing capacity and are generally intended for pedestrian traffic.