Nailing down a quality hardwood floor with OSB
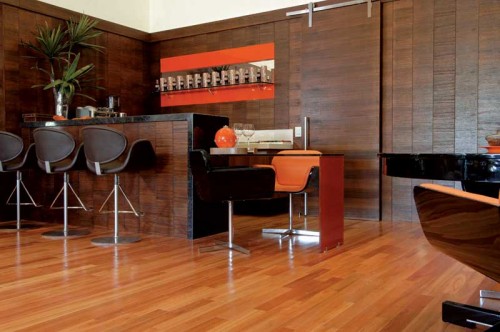
By Chris Degnan
Hardwood floors are popular for their striking grain patterns, rich colours, and natural beauty. Their eye-catching esthetic is not solely dependent on these surface characteristics, however, as what goes under a floor is often as important as the finish material itself.
As the support structure for the flooring, a sound subfloor provides stability underfoot and helps enable a high-quality finish. Excess moisture in the substrate can damage overlying hardwood flooring, potentially creating cupping, cracking, or other defects.
To ensure a first-rate, visually appealing hardwood floor, building professionals are increasingly using oriented strandboard (OSB) subfloors. Engineered to optimize value and performance, OSB panels are typically more consistent than plywood, knot- and void-free, and lower in cost. OSB panels provide a flat, solid base for floorcoverings, and help yield even, stable, and long-lasting floor finishes.
OSB attributes
OSB is a structural panel with uniform strength and stiffness. Manufacturers produce the material by applying durable adhesives to thin wood strands and aligning them into layers of alternating strand orientation for strength. The stacked layers (typically four deep) form large mats, which manufacturers bond together under high heat and pressure.
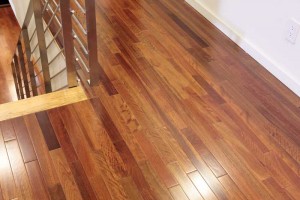
While some early OSB formulations were prone to edge swell and delamination—causing some building professionals to favour plywood—manufacturing advances have improved the moisture resistance. Now, some products have 50-year limited lifetime warranties against delamination. Today, nearly all OSB panels are produced with ‘exposure 1 bond’ adhesives. As with plywood, OSB panels with this bond classification are unsuitable for permanent exposure to weather, but resist the effects of moisture during construction delays. Most manufacturers also treat OSB panel edges with sealants to further protect against moisture intrusion. Additionally, panels are available with self-draining grooves on their edges to eliminate standing water during construction.
All major North American building codes, including the National Building Code of Canada (NBC), recognize OSB for structural applications. Such panels meet stringent performance criteria in Canadian Standards Association (CSA) O325, Construction Sheathing, and the U.S. Department of Commerce (DOC) PS2, Performance Standard for Wood-based Structural Panels.
Creating a high-quality floor system
With proper specification and installation, OSB works with other structural elements to produce a consistent and stable base for hardwood floor finishes. To aid in this process, OSB manufacturers provide a range of technical information on product capabilities and performance, along with installation tips for OSB subfloors.
This article summarizes some of the general factors for using OSB subfloors under hardwood flooring. To keep from voiding warranties (as with any subfloor material), it is important to check with the hardwood flooring manufacturer for specific requirements.
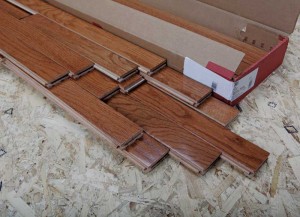
Installation
Contractors can saw, drill, sand, and fasten OSB panels easily with standard tools, though carbide-tipped blades tend to wear best.
Most manufacturers recommend leaving a 3-mm (1/8-in.) gap between panels to allow for normal linear expansion. Some panels have tongue-and-groove (T&G) edges to provide edge support and a self-gapping fit. For such panels, it is necessary to ensure the correct side is installed down so the profiled edges fit together. Manufacturers typically stamp the panels to show which side goes down.
To help stiffen the entire floor assembly, an approved adhesive is applied on the joists before placing and fastening panels. Using adhesive in panel grooves also helps lessen floor movement.
While a typical OSB floor panel thickness is 18 mm (23/32 in.) in residential applications, using thicker 22- or 29-mm (7/8- or 1 1/8-in.) panels can boost floor performance—reducing vibration and providing a more rigid base for hardwood floors. Thicker panels usually cost more, but it is possible to achieve a net savings for the overall floor assembly, as fewer joists might be needed. Specifically, thicker panels can allow an increase in joist on-centre (oc) spacing from 406 mm (16 in.) to either 488 or 610 mm (19.2 or 24 in.), depending on the building type, joist size, occupant expectations for floor performance, and local code requirements.
Moisture management
A critical part of the installation process is to pay careful attention to the moisture content of the subfloor and hardwood flooring—problems can arise later in the finished floor if the moisture differential between the OSB and hardwood is too great. For example, OSB that has absorbed moisture on the jobsite contracts as it dries, causing loosening around nails and staples that attach the hardwood flooring. This can result in pops when occupants walk across the finished floor. If there is a high moisture differential, with the OSB panels having a higher MC than the hardwood, moisture will migrate into the hardwood, potentially causing the flooring to cup or buckle.
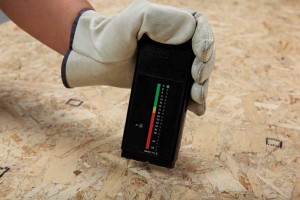
To help ensure balanced moisture content (MC) levels between the subfloor and hardwood flooring, it is important to first confirm the OSB is adequately dry. While a subfloor may appear dry on the surface, moisture content within the panels may be too high. Although it can only accurately be determined with a moisture meter, checkpoints to help identify whether the subfloor might require additional drying time include:
- length of time since construction;
- most recent exposure to rain and/or standing water;
- presence of factory-cut drainage grooves in OSB (this reduces the drying period by preventing standing water during construction); and
- whether HVAC equipment is installed and running.
When testing wood subfloor moisture content, one should use policies set forth by the U.S. National Wood Flooring Association (NWFA). One NWFA recommended policy is to use a moisture meter on at least 20 locations on the OSB subfloor per 93 m2 (1000 sf), and average the results. While a MC of 10 per cent or less is the accepted industry standard, one must still ensure the panels’ MC aligns with the hardwood flooring manufacturer’s recommendations. Further, even if the MC average is within an acceptable range, high readings in one or more areas indicate trouble zones that need additional attention. Areas prone to moisture include portions of the subfloor near exterior and plumbing walls, as well as panels over crawlspaces.
Hardwood acclimation
Proper moisture management requires acclimating the hardwood flooring to the interior environment, which aids in preventing gaps between boards, heaving, or buckling. Hardwood flooring typically arrives at the jobsite with a MC of six to 10 per cent. Since moisture tolerance varies by wood species, floor type (i.e. solid strip versus engineered), and strip width, it is important to check the hardwood flooring manufacturer’s specifications.