Insulated siding is heating up in colder climates
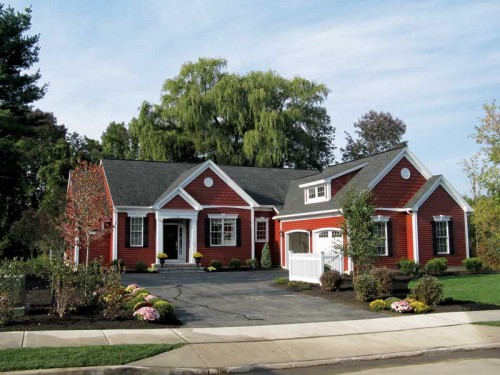
By Matt Dobson
Energy prices are growing increasingly unpredictable, but one constant is the rise in heating bills when the mercury drops. Homeowners are always looking for ways to be more comfortable in their houses and save money on their energy bills. For forward-thinking project teams in cold Canadian climates, this is an opportunity to specify products that help reduce drafts and eliminate energy waste.
One of the less obvious energy-wasters in residential projects is the ‘thermal bridging’ effect—the transfer of heat through framing members or studs that occurs even when windows and walls are insulated. Thermal bridging can rob a home of heat, even in the tightest building envelopes. One way to help resolve this issue involves cladding a home in insulated vinyl siding.
Vinyl siding products can have rigid foam expanded polystyrene (EPS) insulation laminated or permanently attached to the panel. As a form of continuous insulation installed outside of the building framing, these claddings help reduce energy loss from thermal bridging, decrease air leakage, and improve the wall assembly’s overall R-value (or thermal resistance measure).
The first commercial insulated siding was introduced in 1997. Since then, the product has been recognized as continuous insulation by several building codes and energy efficiency programs.
Incentives for cladding with continuous insulation
Canadian codes and voluntary programs recognize this type of siding as ‘home insulation,’ and some even offer grants for energy-saving retrofits where it is included. Through the ecoEnergy Retrofit Homes program (part of the Government of Canada’s Economic Action Plan), for example, homeowners can qualify for grants by using insulated siding with other energy-efficient products.
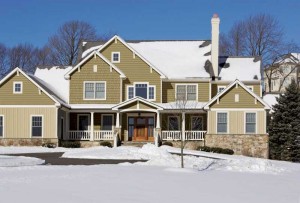
Another voluntary program, National Resources Canada’s (NRCan’s) Energy-efficient New Homes, recognizes the Energy Star Qualified Homes program, which requires new homes meet thermal bridging requirements to earn the Energy Star label. Due to its ability to reduce thermal bridging, insulated siding has been added to the checklist of building products or methodologies that can help qualify homes under Energy Star Qualified Homes, Version 3.
For residential single- and multi-family new construction, the 2011 National Energy Code of Canada for Buildings (NECB) serves as a regulatory tool for energy-efficient homes. Continuous insulation—including this type of vinyl siding––has become a part of the total wall assembly approach because it improves the wall’s thermal value and reduces thermal bridging. Generally speaking, builders and remodelling contractors can use insulated siding to meet NECB’s R-value/U-factor requirements.
Real-world retrofits demonstrate results
Since the first field tests on insulated siding in the early 1990s, design and manufacturing improvements have increased the product’s functionality and durability. To demonstrate this performance, the Vinyl Siding Institute (VSI) commissioned energy research firm Newport Ventures to review the energy performance of insulated siding installed on four existing single-family homes under real-world conditions in cold-weather climates.
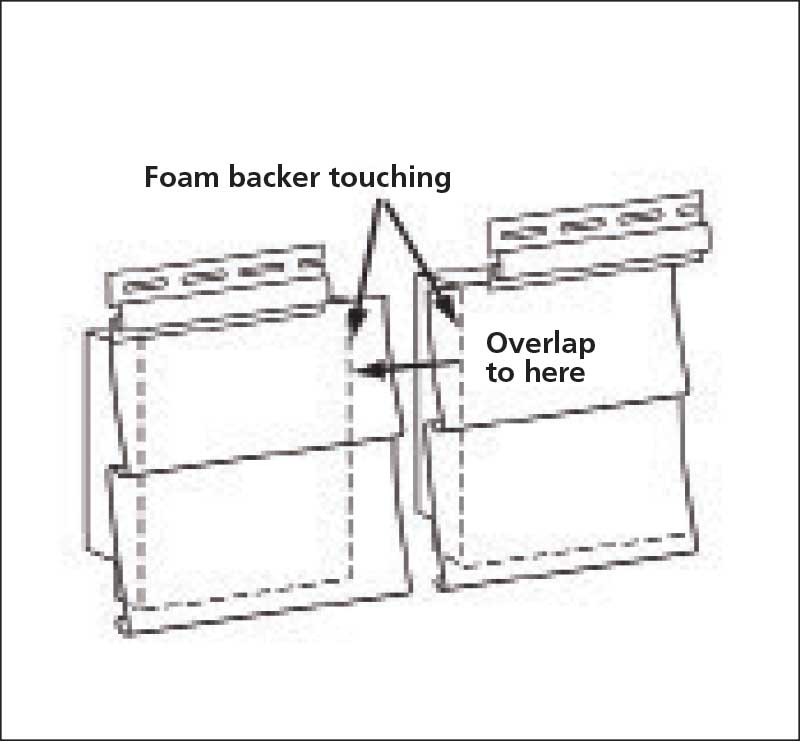
The company gathered insulated siding products from four North American manufacturers and identified single-family detached homes in four cities spanning two of the colder U.S. climate zones. For each home, installers removed the existing siding, placed a water-resistive barrier (WRB) over the sheathing, and installed new insulated siding. The R-values, or thermal resistance ratings of the insulated siding products varied from R-2 to R-2.7 (i.e. RSI-0.35 to RSI-0.48). Before installation of the insulated siding, Newport conducted energy audits on each home to quantify key energy performance metrics, including airtightness, insulation levels, and equipment efficiency.
Airtightness was analyzed using blower door tests:
- before removing the old siding;
- after the existing siding was removed and the WRB was installed; and
- after the insulated siding was installed.
All four homes demonstrated improvements in airtightness; overall, they achieved an average 12 per cent improvement in air tightness after the insulated siding was installed.
Newport simulated pre- and post-insulated siding conditions to project the expected heating energy savings. These simulations included both the R-value impact of the insulated siding, as well as the airtightness improvement measured for each individual home. The building energy simulations demonstrated heating energy savings ranging from five to 12 per cent, with an average savings of about eight per cent across the board.
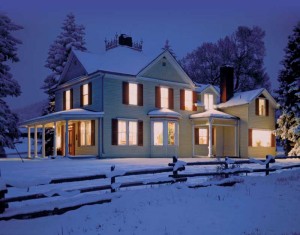
Newport also used the building energy simulations to produce a Home Energy Rating System (HERS) index for each of the houses. After the existing siding was replaced with a WRB and insulated siding, each home achieved an improvement (i.e. reduction) in its HERS index of between two and eight points.
To help Newport determine the effect of insulated siding on heating energy use over time, the four homeowners agreed to provide their utility bills for two years before and two years following the insulated siding retrofits. The company will analyze the bills for differences in heating energy use and update the “Insulated Siding Energy Performance Study,” with results expected in early 2013. (For a current version of the study, visit www.insulatedsiding.info).
Proper performance requires proper installation
As with any other energy-efficient product, insulated siding can only perform as continuous insulation if it is properly installed and according to the manufacturer’s instructions. Installers must understand how to work with the product’s unique properties. With vinyl siding, there are a few installation rules to consider accounting for its expansion and contraction properties. Installers must also know how to accommodate the extra thickness of the insulation with these various siding products.
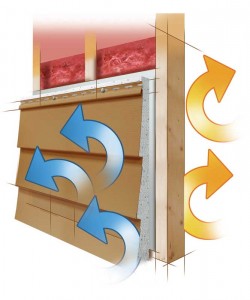
Image courtesy Progressive Foam Technologies
The VSI Certified Installer Program independently verifies whether someone has passed a test on the proper techniques according to ASTM D 4756, Standard Practice for Installation of Rigid Poly (Vinyl Chloride) (PVC) Siding and Soffit.
Before starting installation, one should ensure they are using the starter specified by the insulated siding manufacturer that will accommodate the full thickness of the insulated siding to ensure proper performance. Specifications should include a WRB installed under all insulated siding. The siding is not a watertight covering, but it does function as an initial rain barrier and significantly reduces the amount of water reaching the underlying WRB.
The designers should also specify accessories such as nails and other fasteners that will accommodate the full thickness of the insulated siding. Since the foam material is permanently attached to the panel, insulated siding is thicker than a vinyl cladding alone. It is best to use accessories specified by the manufacturer.
Installers should keep these tips in mind when hanging insulated siding panels:
- On the factory-cut ends of insulated siding panels, the foam is set back from both ends of the panel. This ensures correct overlapping of adjacent panels.
- To overlap the panels, the vinyl tab at the end of one should be inserted between the foam and the vinyl of the adjacent panel. The installer should slide the panels together until the ends of the foam touch to ensure continuous insulation coverage. It is important to note this is different from installing vinyl siding alone, which requires overlapping in a way that allows the panels to move freely from side to side.
- If the siding is being installed in cold weather (i.e. colder than 4.4 C [40 F]), it is recommended to leave a gap of 3.2 mm (1/8 in.) between the foam panels to allow for expansion when weather is warmer.
Installers can use the same type of fasteners employed for vinyl siding installation, but longer lengths may need to be specified to accommodate the insulation’s thickness. The fastener has to be able to penetrate a minimum of 19 mm (3/4 in.) into a nailable surface, and it should not be driven tightly against the siding nail hem. The installer must leave a space equal to the thickness of a dime between the fastener head and the nail hem.
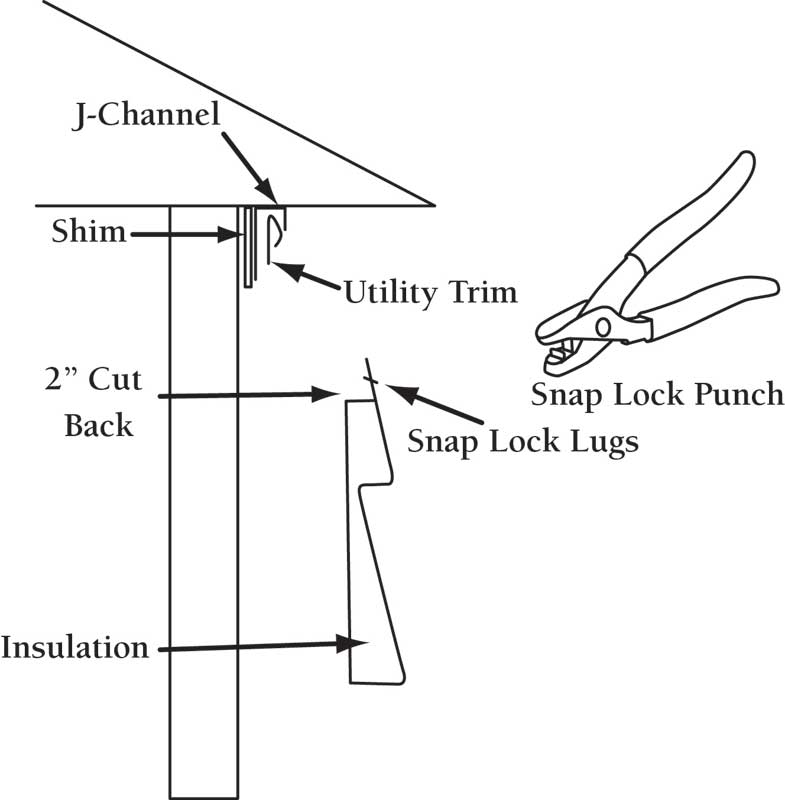
Images courtesy Vinyl Siding Institute
Finishing with foam
Completing the final course of insulated siding at the top of the wall requires a few specific instructions:
- When determining the length of the final panel of a course, the installer should measure from the edge of the foam on the installed panel to the corner, allowing 6.4 mm (1/4 in.) for expansion. This measurement should be applied to the final panel, measuring the foam instead of the panel. This will ensure foam-to-foam contact with the necessary amount of room for expansion of the siding.
- The height measurement of the remaining open section should be taken in several sections, with 6.4 mm subtracted from each location to allow for movement. The panel should then be cut to the required measurement and the foam cut back by 50.8 mm (2 in.). Using a snap lock punch, the vinyl siding should be punched along the cut edge every 152.4 mm (6 in.) with the raised lug on the outside face.
- Utility trim should be installed along the top of the wall to receive the siding’s top edge. Shims should be used under the utility trim to match the angle or distance from the wall of the siding edge. The siding should then be pushed into the utility trim; the raised lugs will catch and hold the siding firmly in place.
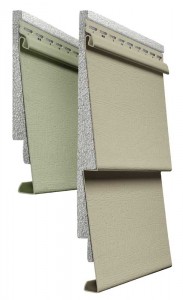
In remodelling applications, insulated siding can be installed over furring strips, but for it to perform as insulation, it must be installed directly over a WRB and sheathing. When insulated siding is installed over furring strips, the space between the strips must be filled in with rigid insulation or another appropriate building material or the insulated siding cannot be considered ‘home insulation.’
Conclusion
The Vinyl Siding Institute’s Insulated Siding as Home Insulation: Guide for Users and Energy Raters illustrates many of these insulated siding installation techniques. The book provides various wall assemblies for insulated siding to demonstrate how various U-factors can be achieved. It also explains how insulated siding is tested to establish R-value, or thermal resistance ratings, and how it can be used for compliance with various energy-related requirements and voluntary programs.
Insulated siding is an affordable way to make homes more comfortable and energy-efficient. It provides a valuable, cost-effective option for builders and remodellers to specify products that will help homeowners reduce drafts and eliminate energy waste.
Matt Dobson is the code and regulatory director for the Vinyl Siding Institute (VSI), which represents manufacturers of vinyl and other polymeric siding and suppliers to the industry. He has nearly 18 years of experience in the construction industry and has a bachelor of science in building construction management from Michigan State University. Dobson is a member of the International Code Council’s (ICC’s) Code Development Committee for the International Building Code (IBC), a consensus committee member for the development of ICC 700, National Green Building Standard, and is a member of the National Association of Home Builders (NAHB). He can be reached via e-mail at mdobson@vinylsiding.org.