Specifying acetylated wood for entry doors
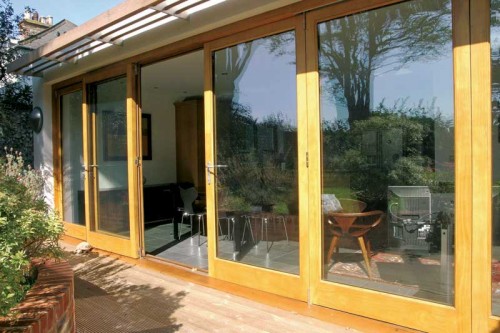
By Lisa Ayala
Given the option, many people gravitate toward wood for entry doors to homes or even light commercial projects. With its rich feel, authentic look, and durability, wood is a timeless, natural choice for optimal curb appeal.
Adding to the list of entry door options is acetylated wood, a high-technology product that undergoes a proprietary, non-toxic modification process to create a more durable and dimensionally stable solid wood product while still retaining natural beauty.
Though only recently made commercially available, acetylation has been studied for more than 75 years. In short, the acetylation process modifies wood at its molecular level by increasing the natural compounds already found there—in other words, nothing is added to the wood that is not naturally present.
More specifically, acetylation targets ‘free hydroxyls,’ an abundance of chemical groups contained within the wood. Free hydroxyl groups readily absorb and release water according to changes in the climatic conditions to which the wood is exposed; this is the main reason why wood swells and shrinks.
The acetylation process alters the wood’s reaction with water by permanently replacing free hydroxyls—the part that absorb moisture—with stable acetyl groups that will not bond with water. Acetyl groups are naturally present in the wood; the acetylation process just increases their level. With a high level of acetyl molecules, the wood does not respond to moisture like regular wood does, improving the shrink/swell cycle by 70 per cent or more. The non-toxic modification also results in a product that is unrecognizable as a food source, proven to be an effective barrier to rot, decay, and insect attack.
The process modifies the wood to its core. Therefore, unlike pressure-treated wood, it can be cut or profiled without exposing unprotected surfaces. Further, since acetylation is non-reversible, there is no risk of leaching or loss.
Due to these characteristics, acetylated wood is appropriate for numerous exterior applications beyond doors, including:
- decking;
- cladding;
- windows; and
- outdoor furniture.
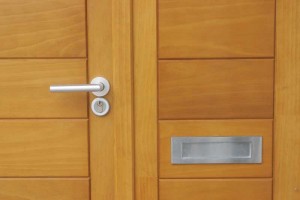
Advantages in durability
In Europe, acetylated wood carries a Class 1 durability under EN 113:1997, Wood Preservatives: Test Method for Determining the Protective Effectiveness Against Wood-destroying Basidiomycetes—this is the highest rating available and is comparable to the best tropical hardwoods. In fact, a recent durability test in New Zealand showed the wood product to be more durable than even old-growth teak. Acetylated wood acts as an effective barrier against a broad spectrum of fungi, including cellar, wet rot, dry rot, soft rot, white, brown, and pore fungi. It is verified by American Wood Protection Association (AWPA) E10, Standard Method of Testing Wood Preservatives by Laboratory Soil-block Cultures. Additionally, the material is indigestible to a wide range of pests, including termites. The wood carries a Class C fire rating—under ASTM E 84, Standard Test Method for Surface Burning Characteristics of Building Materials—and can be treated to meet higher requirements.
The durability and, particularly, stability provide a much more stable substrate for wood coatings. Numerous outdoor and accelerated coating tests demonstrate wood coatings last significantly longer on acetylated wood—film-forming opaque coatings, for example, have been found to last up to three times longer. Therefore, maintenance is dramatically reduced.
Acetylated wood for entry doors
Wooden entry doors are prone to moisture problems, particularly at joints and at the bottom along the weatherstripping. Many doors can swell and warp over time, causing them to stick when closed. This problem with most wood products requires joinery companies to revisit projects to re-hang or trim doors on one or more occasions. Therefore, with its dimensional stability and long-term durability, acetylated wood is a suitable option for fabrication of entry doors to help reduce the likelihood of these problems.
In addition to doors, acetylated wood is being used for frames and trim. To control costs, some door frame producers include acetylated wood just at the bottom of the frame, where the wood is most vulnerable to rot and decay.
Overall, installation of doors made with acetylated wood is the same; however, it is important to pay attention to a few key areas. First, despite its increased dimensional stability, changes in humidity can cause small changes in the material’s volume. Standard tolerances taken into account during product design and installation for regular wood should be followed.
Another consideration with door installation is hardware and the risk of corrosion—acetylated products and other very durable woods contain low levels of acetic acid, which can cause corrosion to hardware. Stainless steel Type 304 or 316 hardware is recommended. Brass is also an option, but may still experience some discolouration over time. Zinc-plated or galvanized steel hardware should be avoided. If stainless steel fixtures are not available and coated fixtures must be used, they should be designed for outdoor use. Pre-drilling is advised.
The wood should be coated at hardware points to provide a barrier; for added temporary protection, a water-repellant spray (such as silicone or polytetrafluoroethylene [PTFE]) can be applied to metal hardware. In enclosed areas such as the lock rebate, an epoxy coating is recommended to provide protection to locking mechanisms.
Machining methodology
Acetylated wood will machine easier than regular wood, producing a very flat surface and improved profile definition. It requires no special tools for cross-cutting, ripping, planing, routing, or drilling.
The material is produced from rough lumber and may have brown discolouration and sticker marks in the first few millimetres from the surface. To achieve a uniform appearance, it may be necessary to plane off several millimetres for stain-grade applications.
When planed properly, acetylated wood surfaces are very smooth. Therefore, knives must be aligned and sharp—otherwise, every flaw or dent in the knives will leave a permanent mark in the wood. When moulding, the rough material is fed through machines as one would do with hardwood rather than softwood. The chip-extraction system should remove shavings to prevent indentations in the planed surface.