Leading The Way in P3 Delivery: Using BIM for capital-intensive projects
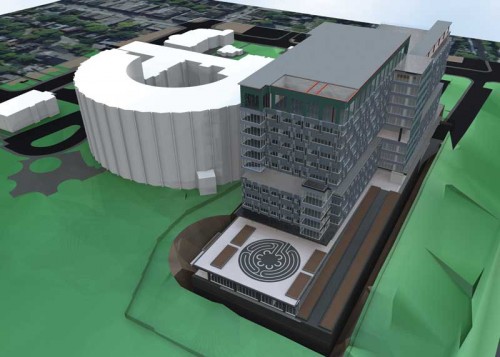
By Terry D. Bennett, LS, LPF, MRICS, LEED AP
Canada is changing the way local hospitals, city streets, or bridges are being financed and maintained. A popular approach the country’s federal and provincial governments have taken to build crucial structures could be the answer for other governments around the world to consider for the infrastructure they desperately need—such as more regional hospitals to provide critical care for families.
This author has attended many meetings with Canadian government offices, developers, and construction companies. He has seen firsthand how public-private partnerships (P3s) are proving to be an effective way for public entities to build much-needed buildings and infrastructure projects—whether a water and wastewater facility, town centre, or a new roadway to connect the suburban environment or other piece
of infrastructure.
P3s are co-operative ventures between the public and private sectors where the risk and responsibility to design, build, finance, operate, and maintain the building or infrastructure project are undertaken by a consortium that most often includes a large contractor as a long-term business opportunity and investment. The private-sector consortium will generally fund the construction, operation, and maintenance of the asset, while the public-sector client will enter into a long-term service-subscription agreement to use the asset—generally for 25 to 30 years. The options range from design-build to outright privatization, where the government transfers all responsibilities, risks, and rewards for service delivery to the private sector. As a result, P3s provide much-needed capital to finance government programs and projects, freeing public funds for use on core economic and social programs.
Modelling the P3 process
With more than 150 projects built or under way last year—including Toronto’s Bridgepoint Hospital redevelopment, British Columbia’s Abbotsford Regional Hospital and Cancer Centre, and New Brunswick’s Trans-Canada Highway—Canada is the North American leader in this new project delivery method.
In Canada, many of the large, critical pieces of infrastructure ranging from $100 million to more than $1 billion have used the P3 delivery method. For municipalities that do not have the capital necessary to build the vital structures their communities require, alternative P3 delivery models are being considered when they may be suitable in terms of:
- project size;
- procurement costs;
- financial capacity;
- internal knowledge and experience; and
- availability of internal resources.
Considering a P3’s procurement phase, project teams are led by the contractor, and include the financier, insurer, consultants for architecture and engineering, and major trades who respond to requests for qualification and proposal (RFQs and RFPs). This can be challenging for newly formed consortiums, as they need to function as a team.
Advanced 3-D design technology has been used to assist in RFP response, allowing for a more concise, highly visual proposal tied to financing and preliminary construction schedules. This helps a consortium prove to government partners it understands project objectives and can describe and visualize valuable, intangible, results.
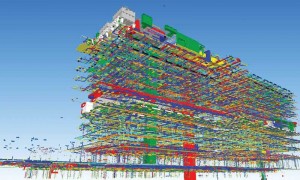
Putting owners ahead of the curve
The long-term risk and responsibility of building and maintaining P3 projects falls predominantly to the contractor. Therefore, many consortiums are mandating their teams use intelligent, 3-D model-based design for planning design, co-ordination of disciplines and trades, commissioning, and the operations and maintenance of their infrastructure projects.
During planning and design stages, there are too often errors, omissions, and confusion in the delivery method since co-ordinating thousands of conventional computer-aided design (CAD) drawings and specifications can overwhelm the design process. Virtual construction in advance of the physical work can uncover errors such as a water hydrant that would appear in the middle of a road or an HVAC system going through a window. Finding and fixing errors in co-ordination within the digital environment, before the project reaches the construction stage, saves valuable time and resources.
How can builders provide the project timetable, price tag, and return on investment (ROI) that make the venture a sound investment for private or public owners and at the same time catch design issues before breaking ground? A crucial component is technology allowing for the virtual construction of building and infrastructure projects. Additionally, technology enables various stakeholders to determine whether the project is profitable enough for long-term investment as well as the airtight integration among the design team, contractors, and subcontractors required to maximize profits.
Streamlining collaboration
To achieve this collaboration, building information modelling (BIM) is taking an increasingly important role since it is the most effective process available. An intelligent model-based process, BIM provides insight for creating and managing infrastructure and building projects faster, more economically, and with less environmental impact.
Municipal and provincial governments are facing pressure for increased efficiency, cost-cutting, and sustainable design, yet most publicly funded capital projects remain within traditional contracts and project delivery methods that have not changed in decades. Governments are trying to meet stringent policies and solve complicated infrastructure problems, while continuing to accept deliverables from a dated and unsophisticated toolset. Most owners are just learning about new project delivery processes such as BIM, and they are beginning to see an increasing mandate during RFPs for its use.
With BIM, intelligent model-based information is available throughout the project lifecycle to guide better decisions for planning, design, building, and maintaining the structure throughout many decades. Since designers can visualize and analyze a project before construction begins, there are fewer conflicts; co-ordinated, consistent information afforded by BIM helps provide faster delivery.
Bridgepoint Hospital
An example of how BIM helps streamline collaboration, detect clashes, and deliver in a traditional design-build/finance/maintain P3 project is the Bridgepoint Hospital redevelopment.
Fully visible along the Don Valley Parkway (one of Toronto’s major roadways), this P3 project began in August 2009. Managed by the Toronto office of PCL Constructors Canada Inc., the new hospital will replace the existing, aging one onsite. As part of the construction project phasing, the nearby Toronto Jail facility will be demolished. The existing historic Don Jail—the second jail onsite—will be incorporated into the new hospital design as administrative offices.