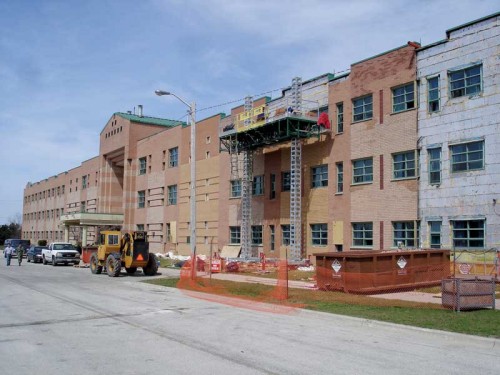
By Steven Fechino
An important part of many Canadian project teams, the masonry industry is a proud group that builds durable structures using time-honoured techniques that have spanned generations. Discipline and mentoring are the keys to learning the ‘laws’ that make up this complex trade. As with all things, masonry has rules that will and will not change over time:
- Masons get paid for what they lay on the wall, not for effort.
- Completing a job correctly costs the mason four times less than a mistake (i.e. once for removal of defective work, twice for its replacement, three and four times for the jobs not completed while the repair work was performed).
- A wall without flashing, completed properly, has a 95 per cent chance of leaking, as opposed to one flashed correctly, which is almost
zero per cent.
Masonry contractors across the country know these three rules, as do many of the architects, specifiers, engineers, and building owners who work closely with them. However, some of the other long-lasting rules have recently undergone some changes.
For example, sealants and flashing technology have improved over the last few years. Products designed to improve the workmanship and quality over what has been available in the past are now available for residential and commercial masonry contractors. With many other recent innovations, new flashing fabrics, membranes, and composites have been created to give the masonry and roofing contractor better options to serve their building owners.
Sealants
Early in this author’s career, before sealants had evolved into what they are now, bituminous mastics were commonly employed to lap flashings, patch around dowels, and seal penetrations that passed through the wall. Bituminous mastics, when used now, should be checked for compatibility with today’s flashings. When determining the compatibility between products, one can simply call the manufacturer and ask; it is also a good idea to request a letter stating the approval or disapproval of the product.
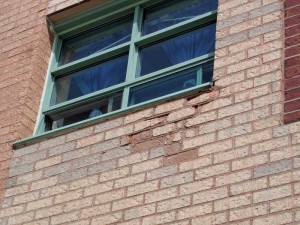
Butyl
Butyl has had a long run in the construction industry, primarily due to the adaptability of the product to the roofing sector. This synthetic rubber, available in sealant tube form as well as tape rolls, is typically more economical to use in the correct application than some of the other sealants on the market.
When making a flashing lap or sealing around dowels, butyl can be an ideal choice. However, it cannot be used for general joint-sealing, expansion joints, or any exposed joints, as this material remains uncured and loose for the life of the product. Butyl is compatible with products made with current formulations of:
- polyvinyl chloride (PVC);
- thermoplastic polyolefin (TPO);
- ethylene propylene diene monomer (EPDM);
- laminated copper fabrics; and
- most rubberized asphalts.
Polyurethanes
Polyurethanes tend to be the most commonly used and accepted sealants for sealing masonry-to-masonry, masonry-to-dissimilar material, and flashing laps. These products are typically one-or-two part sealants that offer a wide range of colours for construction-related joint-sealing.
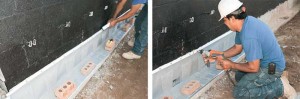
Polyurethanes offer a lifespan ranging from six to 10 years, depending on exposure and geographical location. The working temperatures of polyurethanes are limited from 4 to 35 C (40 to 95 F), with a typical tack-free time of four hours. Single-part polyurethanes are often moisture-cured, while two-part sealants are chemically cured.
Modified polyethers
Modified polyethers have become a new force in the sealant industry. Polyethers are modified silicones that have the gunnability (i.e. flowability out of a caulking gun) of silicone and the most desirable characteristics of polyurethanes. They do not migrate oils into porous masonry and are gunnable in temperatures down to –9 C (15 F).
Given their low level of volatile organic compounds (VOCs) and quick tack-free time (depending on temperature and humidity, usually about an hour), polyethers are expected to eventually replace the popularity of polyurethanes. The chemistry exhibits superior joint material performance and bonding to various membranes and substrates. The material can also be installed in a range of weather conditions. Polyether used with a primer will seal TPO products with excellent results. In terms of first costs, polyethers are a bit higher than polyurethanes, but they have a longer life. Polyurethanes remain suitable for masonry, but are not typically good enough to bond to most new flashing materials.