Building Durable Structures: From concrete mixes to waterproofing strategies
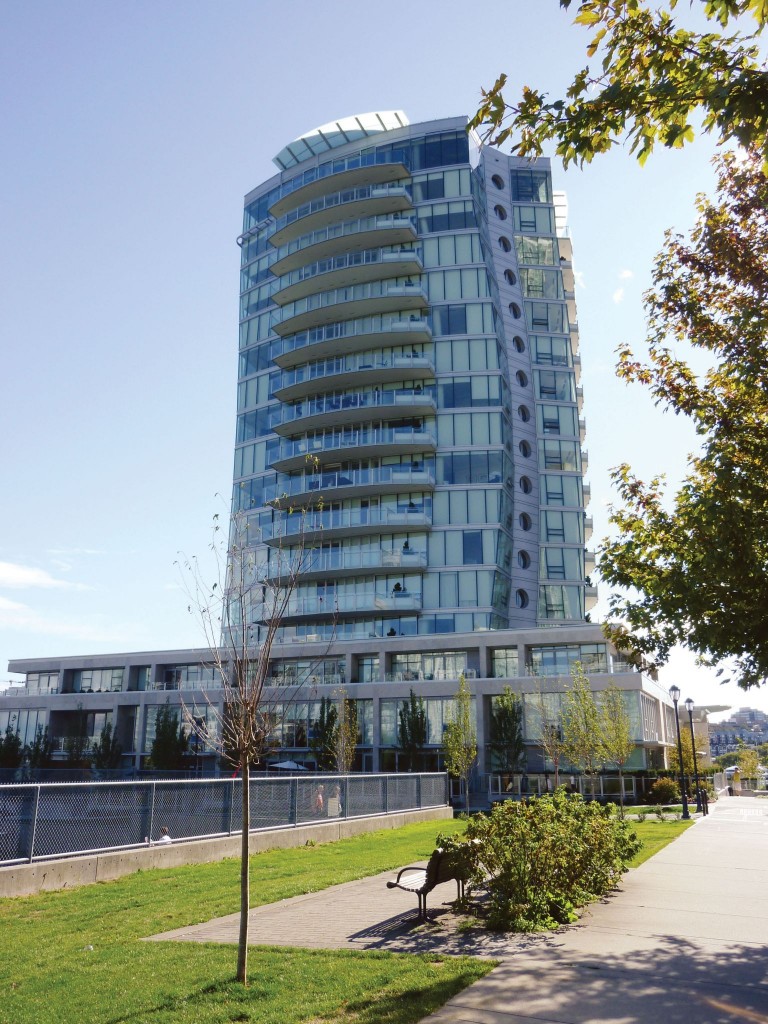
By Alireza Biparva, B.Sc., M.A.Sc.
When it comes to buildings, routine maintenance is expected on any structure as wear and tear is inevitable. However, the difference between small repairs and a major retrofit or rehabilitation is significant. Referring to De Sitter’s Law of Fives, a major repair can be expected to cost roughly five times what routine maintenance would have cost. An all-out replacement will then cost five times what a major repair would entail. So, avoiding large-scale work of this nature is of the utmost importance for the financial viability of a concrete structure.
With much of Canada’s infrastructure built in the 1950s and ’60s, deterioration has been occurring for more than half a century with much of the budget heading toward repair, maintenance, and inspection, instead of building for the population growth. This handicaps the future insofar much of the country’s infrastructure—including roads, highways, and bridges—are in dire need of repair. Governments shoulder this expensive task of inspection and repair. In Ontario alone, an Auditor General’s report in 2009 reported there were 14, 800 bridges with an average age of 30 years and 3500 determined to be in either fair or poor condition. Further, the Federation of Canadian Municipalities (FCM) estimates the country will incur a $123-billion infrastructure deficit, growing by two billion every year. This does not say anything about building infrastructure for a growing population—this is only repairing that with which is already underserving.
Repairs also have hidden costs that affect the bottom line of projects. These include traffic delays incurred due to inspection, maintenance programs and needed repairs. There is also the time needed, fuel costs associated, and the health impact from the pollution set-off in implementing procedures and projects. For instance, the Port Mann Bridge in Coquitlam, B.C., caused disruption to vehicles crossing—the substantial delays meant more pollution given off by idling vehicles, and further, less people using the bridge and finding longer routes to make it across. The final issue was the $3.3-billion investment (approximately) into building a new bridge altogether.
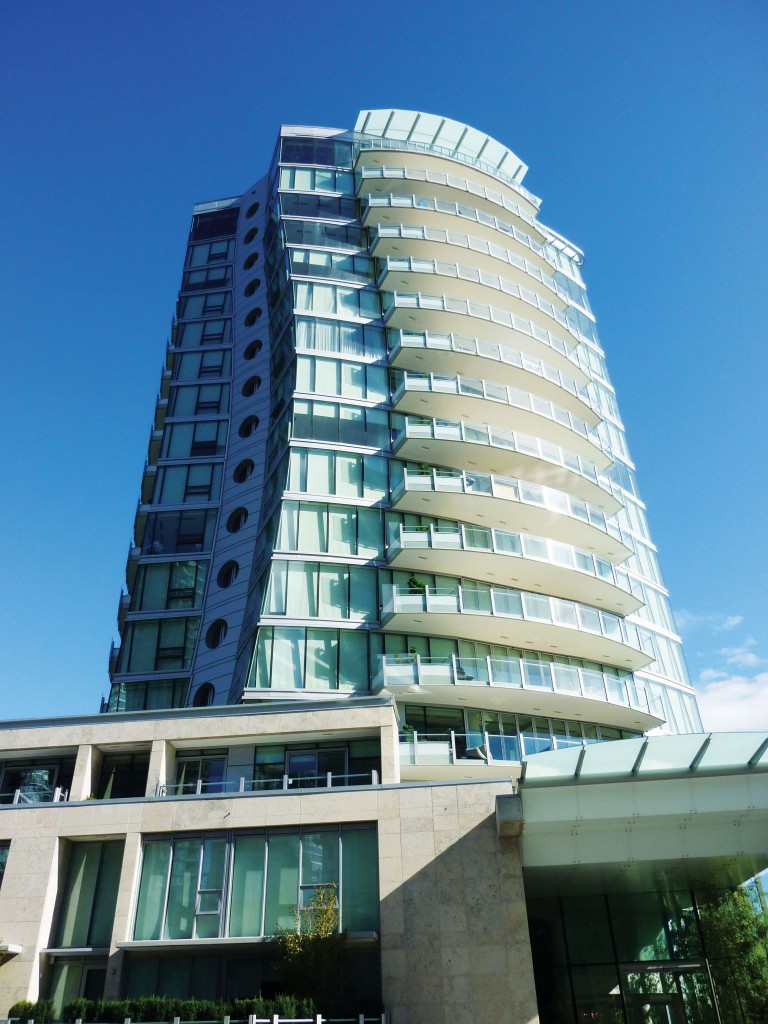
The Canadian government is investing heavily into infrastructure building, but will not be able to run the deficit to a point that continual maintenance and repair is needed. Moreover, the infrastructure built must be done so that it is made as resilient and as sustainable as possible to thwart deterioration from external factors, refuse to breakdown from use, and handle the constant impact of natural weathering hazards. To do so, concrete must be built for the utmost durability.
Concrete challenges, concrete solutions
Concrete comes with many advantages—it can be moulded into virtually any shape, is accessible anywhere on the planet, and has high compressive strength. Though porous in nature, concrete has the potential to be a durable product. However, in its basic form, the material has limitations that can leave a structure vulnerable to early deterioration.
Concrete has low ductility, tensile strength, strength-to-weight ratio and is susceptible to cracking. Above and beyond all, however, concrete is permeable. It allows the ingress of deleterious materials leaving it vulnerable to the attack of chemicals such as acids, sulfate attack, and alkali aggregate reaction. Without doubt, the ingress of moisture, which brings with it different chemicals, is the biggest concern for concrete structures. Thankfully, there are solutions to these limitations, all pointing to ensuring a concrete mix is developed with durability in mind.
This is not to say durable concrete will not require maintenance and even repair from time to time—both remain givens to ensure the safety and service life standards of the concrete structure are met. Moreover, a durable structure will lessen the burden of the costly maintenance and repair needed. This means the lifecycle costs (i.e. total cost of ownership over the life of an asset, including those costs associated with maintenance and repair) will be significantly lower over a longer lifespan with a durable structure.