Art meets science: Roof replacements
By Michael Hensen

As many building restoration consultants and contractors will attest, roof replacement design and construction have evolved substantially in the last 20 years. Contractors or roof designers can no longer rely on habitually selecting favourite roof solutions, and one roof system or assembly can no longer be considered suitable for all buildings. There is no longer one material manufacturer that can supply all the solutions. New roof designs have increased demands from building owners to provide roofs that offer complete sustainable solutions and not just waterproof protection.
Evolution of roof construction practices
Roof construction up to the mid-1980s was traditionally a predictable practice. Roofing crews would leave their place of business to work on projects where the only installation instruction required was how much roof work was expected to be completed that day. There was no question of what type of roof system was to be installed, no concern about how much or what kind of insulation was required, and no consideration of how to ensure continuity of the air barrier, vapour retarder tie-ins, adhesive rates, mechanical fastening patterns, material lists, and shop drawings. The practice worked well, with roofing contractors installing watertight solutions that would typically provide long-lasting, effective results. Roofing technicians were craftsmen often trained through apprenticeship and generational-type training. They were successful in their trade primarily due to the predictable and repetitive nature of working with built-up roof assemblies with few variables and the sole objective of keeping precipitation out. There was very little thought of using roof assemblies for anything but waterproofing.
Modern construction practices and increased building code demands have transformed substantially since the 1980s, primarily to provide a better environmental separation between the interior and exterior climates, improve interior comfort, and reduce energy costs. There are no longer umbrella-type covers on buildings; instead, impermeable solutions that attempt to control or eliminate thermal, moisture, and airflow migration. Early attempts with what seemed to be revolutionary materials, including new membranes and insulations designed to provide improved roof performance, brought mixed results. As an industry, roofers and designers alike experienced roof system failures, often due to a lack of understanding regarding how to install the roof with the new products and not knowing how to apply building science principles to roofing design and installations.
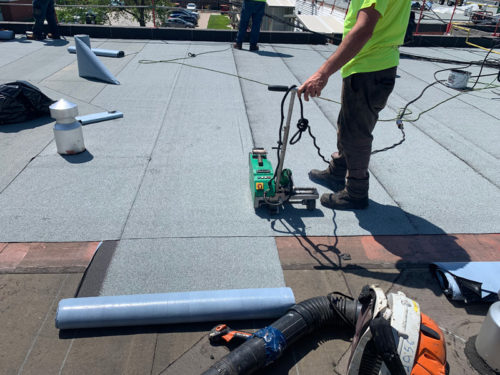
Challenges with early insulated roof systems
The early versions of insulated roof systems brought new issues, including vapour drive and thermal bridging, which resulted in uncontrolled deterioration and premature failures of roofs to provide the desired improved protection. The moisture-related deterioration included reduction in anticipated thermal resistance values, mystery leaks, emulsifying adhesives, corrosion of metals, and mould issues. Membrane technology also changed as new membrane types were developed to improve performance and (hopefully) provide reliability in an insulated roof system. Roof membrane system types included single- and multi-ply assemblies incorporated in built-up (membrane over insulation) or inverted (membrane under insulation) formats. The unfortunate part of the new membrane and insulation trend was that the roofing industry was unsure about how to install and detail the new roof assemblies. Roofing contractors would rely on their workers with their traditional built-up roof training, habits, and equipment to install new single- or multi-ply systems by trial and error. As time progressed, some membrane manufacturers worked with contractors and industry organizations to determine best practice methodology and attain reasonable confidence in providing long-term solutions.
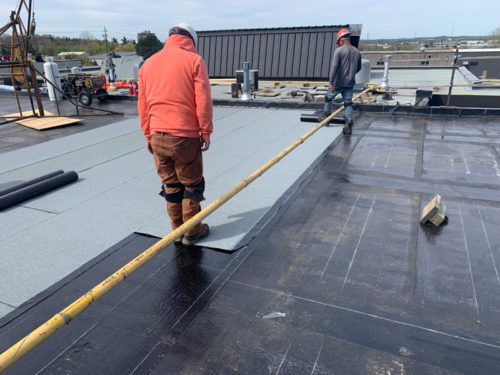
There is no denying that historically, owner roof replacement decisions were swayed by selecting roof membrane systems from persuasive material sales staff offering extraordinary solutions and services, the attempt for the economy by choosing an inexpensive solution and price, or even chasing what appears to be a too-good-to-be-true warranty. The bottom line is that no sales pitch can guarantee success, the best price does not ensure a successful solution, and no warranty has ever improved the performance of a roof assembly. A well-designed and installed roof system deserves warranties issued by the contractor and membrane manufacturer as a gesture of quality, not as a guarantee that a roof system is a suitable solution to waterproofing and energy management or that the roof system meets the building code.
Modern designs account for the difficulty of installing roofs (the art) to meet raised expectations of building performance (the science) and, of course, all within governing building code requirements. The practicality of installing membrane and insulation continuity can sometimes resemble a game of “Twister” that requires coordination between the roofing contractor and representatives of other trades, including mechanical, electrical, plumbing, fenestration, cladding, and insulation contractors, during new build construction projects. Roofing contractors are often hired as general contractors, subcontracting other trades within a roof replacement project contract as the only way to complete a roof replacement without risking water infiltration.
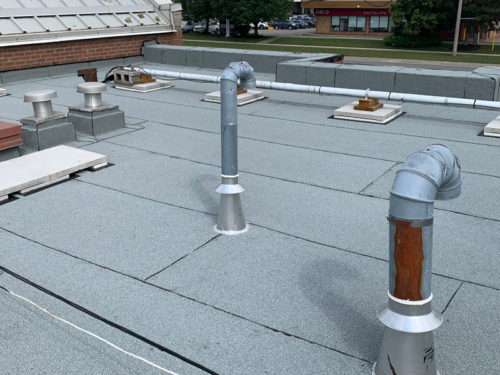
Prior to designing a roof replacement, it is important to understand how the existing building has been constructed, including the type of structure and roof deck, existing mechanical and plumbing systems, parapet and adjacent wall construction, rooftop equipment, and penetrations. It is counterproductive to design a roof incompatible with existing materials or building detailing as the connections could fail, allowing for air and moisture infiltration (resulting in energy loss and leaks). Removing wall parapet claddings to ensure continuous barrier membrane and insulation transitions, lifting mechanical units to complete curb detailing, and ensuring sufficient drainage capacity and strategy are all steps that must be intentionally and carefully detailed and performed to ensure successful roof replacement.
Relying on the roofing contractor’s technician to bridge the transition between adjacent wall and parapet detailing, building materials, and roof accessories without professional direction opens the possibility that the technician’s installation does not meet building code and building science best practices. This is not a slight towards a roofing technician’s ability but is an emphasis on the co-operative approach between the roofing contractor and design professional that roof replacement work should follow. In turn, the designer must be mindful of the difficulties, limitations, and obstacles of roof construction and the notion that what may look good on paper may not be possible or practical to install. Weather conditions, safety, accessibility, and material limitations could all turn what looked like a good design idea into an impossible or costly endeavour.
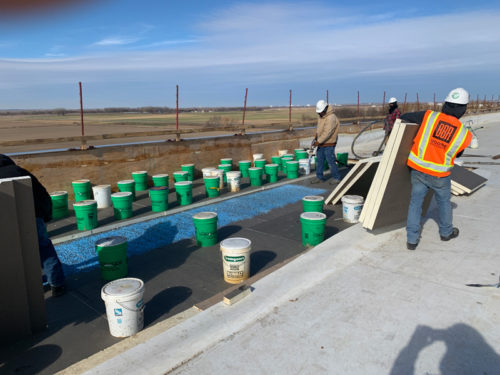
Modern roofing practices and responsibilities
Today’s roofing contractors have, for the most part, adapted to the modern ways of roofing. They send their crews to project sites with material safety data sheets, life safety and rescue equipment and plans, engineered shop drawings for scaffolding and hoarding, building and road closure permits, and tapered insulation drawings. Today’s roofing technicians are trained to install multiple types of roof membranes and incorporate them with insulation in various configurations of roof systems. How they incorporate their ability to work with roofing materials into the entire building envelope is where accurate contract documentation and site review of work in progress by a design professional lead to successful roof installations.
With the trend toward municipalities requiring building permits for roof replacement work in many jurisdictions, designers are reminded of their obligation to implement current building codes and municipal by-law requirements in the design. Considerations for structural loading, wind uplift resistance, roof drainage, insulation values, and building occupancy have always been required; however, they are not often accurately analyzed or calculated.
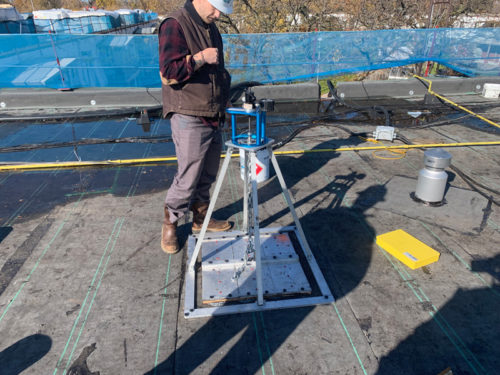
Balancing design and practicality
In recent years, increased demands have also come from how roofs are used. Some view roofs as prime opportunities to implement landscaping, additional building mechanical and operational equipment, stormwater retention systems, and energy production equipment (solar and wind). Some of these have become requirements and are included in municipal by-laws to “green” the roof surfaces and reduce the negative aspects of large, low-slope roof spaces. How roof design and construction are to cope with these new demands on roof space is a challenge from a roofing design and engineering perspective. Providing viable solutions to roofing contractors to overcome these innovations to the roof space must be the objective of the roof design professional.
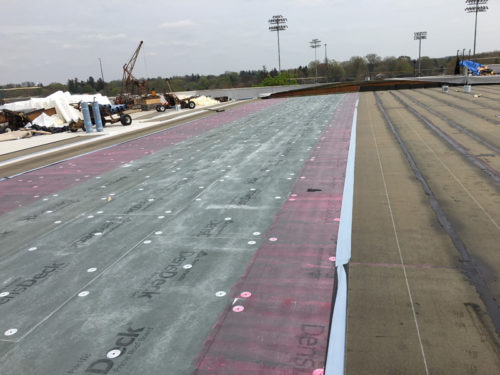
Looking at the future of roof construction practice, designers must be able to continuously identify solutions to meet the demands of balancing roof installation with sound building science and engineering principles. With the most recent demands by governments of decarbonization, CO2 reductions, energy consumption reductions, and sustainable land and building stewardship, owners are more motivated than ever to engage professionals with proven experience in balancing the arts and sciences of roof design and installations.
Author
Michael Hensen is a professional engineer and a registered roof consultant (IIBEC). His technical duties for Rimkus include engineering and leadership of the building enclosure consulting practice.