By Greg Fantin
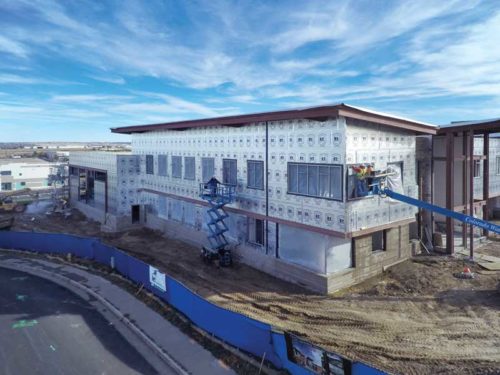
Shortages of certain construction materials are compelling builders and contractors to seek substitutes and alternative suppliers to meet the demand for new construction. While mineral wool products continue to face long lead times in the North American market, potentially hindering momentum for new construction, another more cost-effective option for continuous insulation (c.i.) is polyisocyanurate (polyiso) for above-grade exterior wall applications
Polyiso is a rigid, closed-cell foam board insulation known for its outstanding thermal efficiency and high RSI-value per inch of thickness. Its core is made of a thermoset plastic foam, usually encased between aluminum, coated glass, or polyethylene terephthalate (PET) facers. This composition makes polyiso an ideal choice for effective temperature regulation in buildings. The insulation is effective for exterior above-grade and below-grade, commercial and residential applications. Through a continuous lamination process, it forms a durable, thermally resistant core with its typical facers.
Polyiso’s faster installation process also eliminates the need for a separate air/water barrier, saving both time and money. Additionally, polyiso meets NFPA 2851 fire safety standards for all common claddings in modern construction and is available for immediate use.
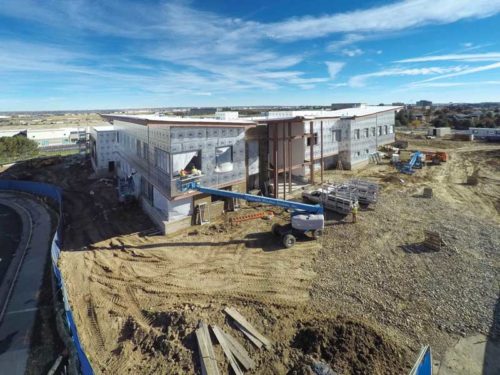
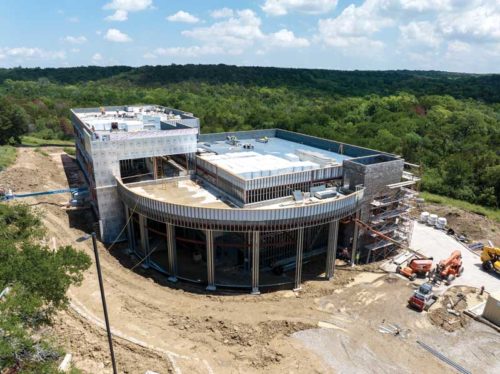
Higher RSI-value
Polyiso insulation has one of the highest RSI-values per inch among foam board insulations, typically between RSI-1.05 to RSI-1.14 (R-6 to R-6.5) per inch. R-value is a measure of thermal resistance, indicating how well an insulation material can prevent heat flow. Mineral wool insulation, conversely, has a lower R-value per inch, generally around RSI-0.65 to RSI-0.73 (R-3.7 to R-4.2). The RSI-value is a measure of thermal resistance, indicating how well an insulation material can prevent heat flow. This higher RSI-value allows cladding to be secured closer to the structural studs and eliminates the need for expensive cladding attachment systems such as Z-furring, which also compromises thermal performance.
The closed-cell structure of polyiso also minimizes air and moisture infiltration, enhancing its insulating properties. The high RSI-value means it can provide superior thermal resistance with a thinner layer of insulation. This is particularly beneficial in space-limited applications such as walls, roofs, around windows and doors, and below-grade. This insulation is widely used in commercial and residential buildings, especially in areas where maximum insulation efficiency is needed without adding significant thickness.
In comparison, mineral wool is made from spun fibres of rock (basalt) or slag (a byproduct of steel production), and has an open-cell structure, which allows airflow that can reduce its thermal performance. Achieving the same level of insulation as polyiso would require a significantly thicker, and more costly, layer of mineral wool. Mineral wool is commonly used in both residential and commercial buildings, particularly in applications where fire resistance and sound absorption are critical considerations.
In areas where space is restricted, mineral wool insulation can pose a challenge. In wall assemblies or confined attic spaces, the additional thickness of mineral wool can reduce the available living or storage space. Additionally, the increased material thickness can complicate the installation process, requiring adjustments to framing or other structural elements to accommodate the thicker insulation. Careful consideration is needed when used in space-constrained applications.
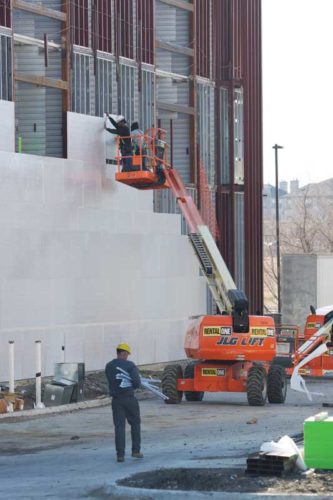
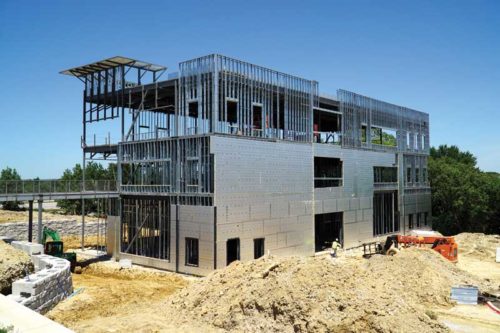
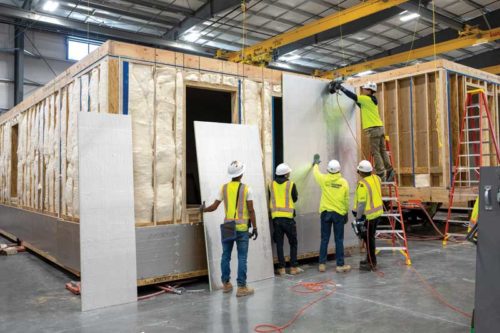
Moisture resistance
Polyiso is highly resistant to moisture. This closed-cell foam insulation does not absorb water, making it suitable in areas where moisture resistance is crucial. Polyiso is often used in exterior wall assemblies, roofing systems, and below-grade applications where water exposure is a concern. Its ability to resist moisture helps prevent mould growth and protects the building envelope from water damage.
While mineral wool is water-resistant, it is not as impervious to moisture. While it repels water to a certain extent, mineral wool can absorb some moisture if exposed to prolonged or heavy water contact. To mitigate moisture absorption, mineral wool is often used in conjunction with a vapour barrier or other moisture management systems, especially in areas with high humidity or potential water exposure.
Cost effectiveness
Polyiso’s high RSI-value means less material is needed to achieve the same insulation effect. This can lead to additional cost savings in terms of materials and labour, as well as potential energy savings over the building’s lifetime.
It is also worth noting that polyiso boards are lightweight and easy to handle, cut, and install. In comparison, mineral wool is denser and heavier, which can make it more difficult to handle and install, and requires careful handling to avoid irritation from the fibres.
Environmental impact
Polyiso is often considered for its energy efficiency benefits during the building’s operational life. The high RSI-value of polyiso contributes to better energy efficiency by reducing heat loss or gain more effectively. This can result in lower heating and cooling costs and a smaller carbon footprint over the building’s operational life. Additionally, polyiso insulation can also serve as the building’s primary air- and water-resistive barrier,2 enabling architects to reduce redundant materials in their designs.
Common misconceptions
Mineral wool has been a popular choice for its insulating properties and is frequently selected based on the belief that it is non-combustible and will prevent fire spread. However, this is not entirely accurate. The spread of fire depends on all components within a building envelope. Mineral wool assemblies can still fail NFPA 285 fire tests and must undergo testing and evaluation to ensure they meet fire safety criteria when combined with combustible claddings and water-resistive barriers (WRBs).
Another common misconception is the notion that a building envelope must be permeable. Designing a permeable assembly can be complex, as the designer must account for the permeability of each component and their combined permeability, which is limited by the least permeable component. This is not to say the wall should be permeable; however, some designers believe it should be able to pass through, which is incorrect. A primary benefit of a polyiso c.i. wall system is that vapour and air cannot pass through it
Additionally, the designer must consider the year-round vapour drive, as vapour can sometimes be driven into the building rather than drying outward. In contrast, a warm wall assembly is simpler and safer. The main consideration is to use enough c.i. to ensure the dew point is within the rigid foam board, thereby eliminating the potential for condensation. This approach moves the environment of the cavity inside, where the HVAC system manages moisture just as it does for the occupied living space. This is the easiest solution, offering the most cost-effective and lowest moisture potential throughout the year.
Conclusion
While both polyiso and mineral wool have their advantages, polyiso is often preferred for its higher RSI-value per inch, moisture resistance, lower cost, and ease of handling and installation. However, the choice between the two should consider the specific requirements of the construction project, including thermal performance, moisture conditions, fire resistance, environmental impact, and budget.
Notes
1 NFPA and CAN/ULC testing requirements for vertical flame spread on walls are closely aligned processes to determine fire safety compliance for wall assemblies. The document by the Metal Construction Association (MCA) explains this in more detail, review it at metalconstruction.org/view/download.php/online-education/education-materials/mcm-educational-downloads/metal-composite-materials-fire-performance-testing-in-the-united-states-and-canada.
2 To view test data, review the data sheet at rmax.com/ecomaxci-fr-air-barrier.
Author
Greg Fantin has served as vice-president of marketing and sales for Rmax, a division of the Sika Corporation, for the past 12 years. Fantin is dedicated to championing the polyiso industry, proactively advocating for the insulation as one of North America’s most widely used and cost-effective insulation products. He currently serves on the board of directors for the Polyisocyanurate Insulation Manufacturers Association (PIMA), an association of polyiso manufacturers and industry suppliers, and served as its chairman from 2018–2020.