By Mickel Maalouf
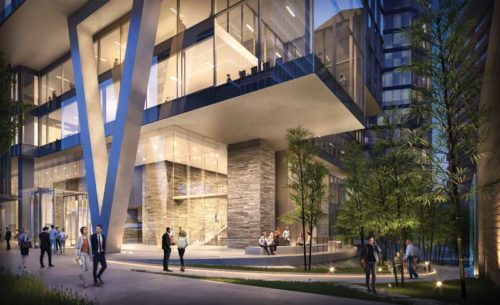
The use of spray polyurethane foam (SPF) insulation as the air barrier system is a critical aspect of modern architectural and engineering practices to enhance building energy efficiency and durability. Using SPF as a comprehensive air barrier system in new constructions and selective retrofits (subject to review by the building envelope consultant) requires careful consideration of essential design aspects. Keeping that in mind, the focus should be on mitigating air leakage and enhancing air-tightness, refining application techniques, and ensuring compliance with prevailing building codes and standards.
In Canada, building codes and regulations are evolving to emphasize the importance of air barrier systems in improving energy efficiency and building performance. Key developments include increasingly stringent air-tightness requirements which push for more advanced air barrier solutions. Additionally, government programs and incentives are promoting the adoption of energy-efficient building practices, including the use of effective air barrier systems. Further, the shift towards performance-based codes, which focus on the overall energy performance of buildings rather than prescriptive measures, is encouraging innovation in air barrier technology.
To illustrate, the National Energy Code for Buildings (NECB) mandates building assemblies be tested as “air barrier systems” to control air leakage and ensure resistance to high wind pressures. These products provide robust solutions for achieving the required air-tightness levels, contributing significantly to improved energy-efficiency and building durability, enhancing long-term resiliency.
The development and adoption of technologies are significantly transforming the air barrier systems industry. For example, spray foam, which combines insulation and air barrier functions, has been tested and approved in several assemblies for decades as an air barrier system. It has been frequently used in large buildings due to its excellent air sealing properties and thermal performance and is now being used in buildings that need to meet the new stringent NECB requirements. Understanding the properties of spray foam insulation, including its thermal resistance and the distinctions between open-cell and closed-cell foams, is crucial.
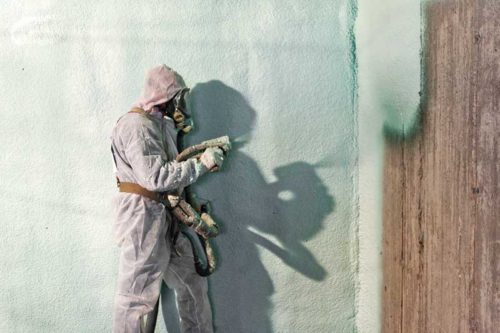
Understanding spray foam insulation properties
Spray foam insulation is renowned for its high thermal resistance and air-sealing capabilities, which contribute to enhanced energy efficiency and indoor comfort. SPF is available in two primary types: open-cell and closed-cell foam.
Open-cell spray foam insulation provides a superior air barrier compared to traditional insulation in various applications such as walls, floors, and attics. Recognized as a versatile option for home insulation, it expands upon application to fill gaps and cracks, thereby forming an effective air barrier. By adhering to most construction surfaces and creating a tight seal, open-cell SPF enhances a building envelope’s air-tightness while acting as an effective sound barrier.
Closed-cell foam, on the other hand, is denser and offers a higher RSI-value per inch, providing excellent thermal insulation. Its impermeability to water vapour makes it ideal for use in exterior applications and areas prone to moisture exposure. Closed-cell foam also adds structural strength to the building envelope due to its rigidity and adhesive properties.
Understanding the differences between these foam types is crucial for selecting the appropriate SPF for specific applications and ensuring optimal performance as an air barrier system.
There are many new types of spray foams on the market today to choose from. Some enhanced versions of closed-cell spray foam, manufactured in Canada, feature specific Environmental Product Declaration (EPD) and have been tested as air barrier systems in accordance with CAN/ULC S742, Standard for Air Barrier Assemblies, as well as for radon resistance. The hydrofluoroolefin (HFO) blowing agent used in them is the most environmentally conscious to date, with zero ozone depletion potential (ODP) and a global warming potential (GWP) of 1. They are compatible with most building products and can be used in various applications, including unique wall assembly systems that allow for the installation of insulation from the interior while managing the thermal bridging of the studs and structure. These are considered “all in one” spray foam products as they are air barrier, vapour barrier for interior, exterior applications above- and below-grade, and rain screen.
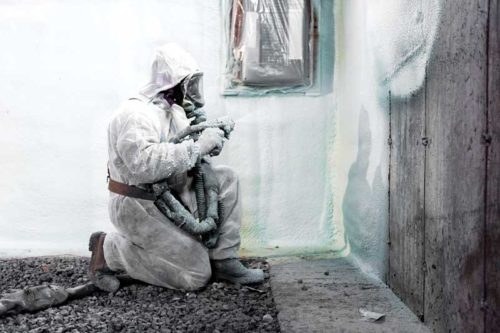
Mitigating air leakage and enhancing air-tightness in buildings
SPF plays a significant role in mitigating common air leakage paths, such as joints, seams, and penetrations, thereby enhancing the overall air-tightness of buildings. Effective air sealing reduces energy loss, improves indoor air quality (IAQ), and enhances occupant comfort.
Sealing around penetrations, such as pipes, ducts, and electrical conduits, is crucial to prevent air leakage. SPF can be used to seal these areas effectively, providing a continuous air barrier.
Thermal bridging occurs when conductive materials, such as metal studs or concrete, create a path for heat flow, bypassing the insulation. SPF can be applied over these thermal bridges to reduce heat loss and improve the overall thermal performance of the building envelope.
SPF application as a continuous insulation must cover the entire building envelope without gaps or interruptions. This ensures a consistent thermal barrier and minimizes the risk of thermal bridging and air leakage.
To meet NECB requirements, there are high performance spray foam products in the market that are effectively tested as air barrier systems in accordance with CAN/ULC S742.
Application techniques for optimal air barrier performance
Application techniques for SPF are crucial in ensuring the optimal performance of air barriers. Achieving uniform thickness and density in SPF application is crucial for maintaining continuous insulation and air sealing, especially over complex geometries and thermal bridging areas.
Additionally, in Canada, where spray foam application standards are embedded into code, compliance means spray foam must be applied in accordance with the CAN/ULC S705.2 standard of application. This ensures only trained and licensed contractors can install the product.
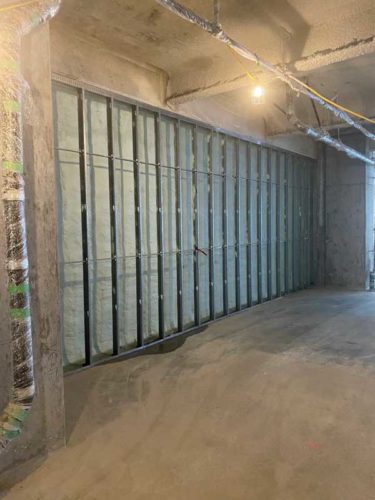
Best practices for SPF application include:
- Surface preparation: Proper surface preparation is vital for adhesion and performance. This includes cleaning the substrate to remove dust, debris, and contaminants, as well as ensuring the surface is dry and free of moisture.
- Application methods: SPF can be applied using various methods, including spray guns and portable units. The choice of application method primarily depends on the project size, complexity, and specific requirements. Regardless of the method, a consistent application technique is critical to avoid gaps, voids, and uneven thickness.
- Layering and curing: Applying SPF in multiple layers can help achieve the desired thickness and density. Each layer must be allowed to cure properly before applying the next to prevent issues such as shrinkage and poor adhesion. Monitoring the curing process and environmental conditions, including temperature and humidity, is essential for optimal air barrier results.
While application technique is important, so is the equipment. It must be capable of delivering a precise 1:1 volume ration of polymeric isocyanate (PMDI) and polyol blend at appropriate temperatures and spray pressures. It is crucial to use trained and certified applicators to ensure these parameters are met and proper installation is achieved. Ensure the substrate temperature is at least 5 degrees above the dew point, with optimal processing results achieved when ambient humidity is below 80 per cent. The substrate must be free from moisture (dew or frost), grease, oil, solvents, and any other contaminants that could negatively impact the adhesion of the polyurethane foam. This product is not suitable for covering flexible ductwork. Additionally, it must not be used when the continuous service temperature of the substrate or foam falls outside the range of -60 to 80 C (-76 to 180 F).
It is also required this product be separated from the building’s interior by an approved thermal barrier or a finish material equivalent to a thermal barrier, as per applicable codes. The most common thermal barrier is a regular 12.7-mm (0.5-in.) interior gypsum board commonly used as finishing material.
Compliance with building codes and standards
Understanding compliance associated with integrating SPF into air barrier systems, including adherence to the latest building codes and standards is critical. This includes navigating the requirements of energy codes, fire safety standards, and environmental regulations. Having SPF also contributes to achieving certifications under various green building frameworks, such as LEED.
Energy codes
In Canada, the energy efficiency of buildings, including the use of air barrier systems made of spray foam insulation, is governed by several codes and standards:
- NECB
- Thermal performance: Spray foam insulation must meet effective thermal resistance (RSI-value) requirements to cut thermal bridging and enhance the energy efficiency of building envelopes overall.
- Air leakage control: The NECB mandates stringent air leakage control and high wind pressure resistance measures, requiring assemblies be tested as air barrier systems. As such, several assemblies insulated with spray foam are tested as air barrier systems in according with CAN/ULC S742 to meet those requirements.
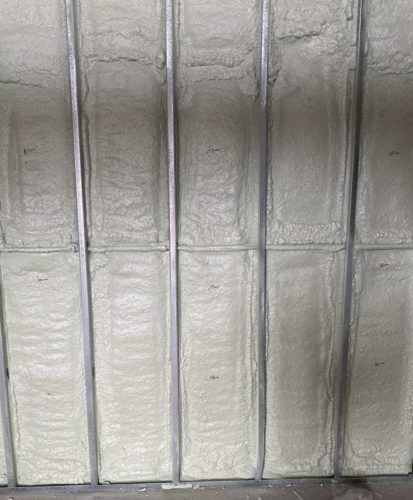
- National Building Code of Canada (NBC)
- Section 9.25—Heat Transfer, Air Leakage, and Condensation Control: This section details the requirements to control heat transfer, air leakage, and condensation within building envelopes. Spray foam insulation used as an air barrier must comply with these specifications to ensure energy efficiency.
- Provincial and territorial codes
- Various provinces and territories may have their own energy efficiency requirements, often based on or more stringent than the NECB. Builders must comply with local regulations regarding the use of spray foam as an air barrier.
Fire codes
Fire safety regulations for spray foam insulation used in air barrier systems are governed by the NBC and specific ULC standards:
- NBC
- Section 3.1.5—Noncombustible Construction: This section includes requirements for combustible materials used in noncombustible buildings. Spray foam can be used in noncombustible buildings given it meets certain standards, such as flame spread rating, and that it is separated from adjacent spaces by a thermal barrier.
- Section 9.10.17—Flame Spread Limits and Section 9.25.2—Thermal Insulation. These sections provide guidelines for the installation of foamed plastics in housing and small buildings, notably regarding their flame spread index and their protection by a thermal barrier.
- CAN/ULC-S101, Standard Methods of Fire Endurance Tests of Building Construction and Materials
- Fire Endurance Testing: Some high-rise building assemblies using combustible insulation may need to undergo fire endurance testing to ensure they can withstand fire exposure and maintain structural integrity. There exist several assemblies with spray foam insulation that have been tested to meet CAN/ULC S101 standards to comply with code requirements in such instances.
- CAN/ULC-S102, Standard Method of Test for Surface Burning Characteristics of Building Materials and Assemblies
- Flame Spread and Smoke Developed Index: Spray foam must be tested for its surface burning characteristics, including flame spread and smoke development ratings.
- CAN/ULC-S124, Standard Method of Test for the Evaluation of Protective Coverings for Foamed Plastic
- Protective Coverings: Spray foam must be covered with approved protective materials to separate it from adjacent living spaces.
Environmental regulations
Environmental regulations for spray foam insulation focus on its impact on the environment, particularly regarding the use of blowing agents and the material’s lifecycle impact:
Canadian Environmental Protection Act (CEPA)
Blowing agents: The use of hydrofluoroolefin (HFO) blowing agents with low GWP and zero ozone depletion potential (ODP) is mandatory to minimize environmental impact.
Chemical safety: Compliance with regulations on the use and disposal of chemicals used in spray foam production and application.
EPDs
Transparency and sustainability: EPDs provide detailed information on the environmental impact of spray foam products throughout their lifecycle, from raw material extraction to disposal.
Green Building certifications
LEED: Spray foam insulation can contribute to LEED certification points by improving energy efficiency, reducing air leakage, and using environmentally friendly materials. Some of the best products on the market are made of recycled plastic materials, rapidly renewable soy oils, and fourth generation blowing agents with zero ODP and less than one GWP. This type of spray foam product meets all the requirements of the Paris, Kyoto, and Montreal protocols.
Indoor environmental quality: SPF helps maintain indoor air quality and comfort by reducing air leakage and controlling moisture. Some SPF products are UL GREENGUARD GOLD-certified for IAQ, meeting volatile organic compounds (VOC) emission standards such as those other building materials to ensure safety and healthy indoor environments. This certification aligns with the LEED Indoor Environmental Quality category, emphasizing the importance of creating healthy indoor spaces.
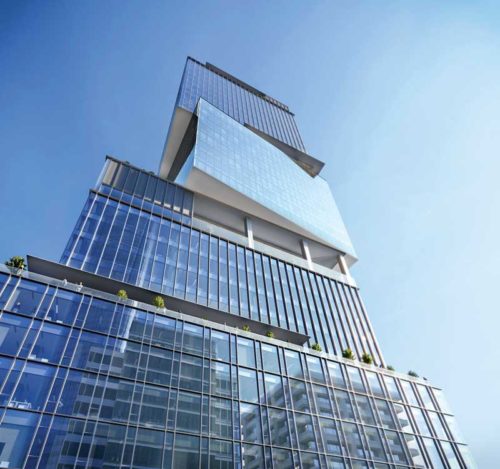
Case study: The Stack
To illustrate the effective integration of SPF with air barrier systems in modern building designs, consider The Stack in British Columbia. Situated in the vibrant heart of Vancouver, The Stack stands as a testament to modern architecture and innovative design. This project has transformed the city’s skyline, heralding a new era of state-of-the-art office spaces.
With its ascending and intricate twists, the building transcends conventional standards of architecture. It also emphasizes a deep commitment to sustainability. Notably, The Stack is Canada’s first commercial high-rise office tower to achieve the prestigious Canada Green Building Council’s (CAGBC) Zero Carbon Building—Design Standard certification. Its pursuit of LEED v4 Core & Shell Platinum certification further underscores its dedication to environmental responsibility.
Architects and engineers faced the challenge of creating intricate and visually appealing structures for the building without being constrained by building envelope restrictions. Given the specific insulation performance criteria set for this project, they chose an innovative spray foam solution that acts as an effective air and vapour barrier, seamlessly integrating with diverse architectural elements, and sealing all joints and material junctions to create a perfectly sealed, more energy-efficient building. Meanwhile, to reach the LEED and Zero Carbon Building objectives, architects chose spray foam insulation for its low embodied carbon and the high energy efficiency it provides.
Conclusion
Integrating spray foam insulation with air barrier systems is a strategic approach to enhancing building performance, sustainability, and occupant comfort. By comprehending the properties of SPF, ensuring material compatibility, refining application techniques, and adhering to building codes and standards, architects and engineers can achieve optimal results. The benefits of SPF, including superior thermal resistance, air sealing capabilities, and contributions to green building certifications, make it a valuable component in modern construction practices.
As demonstrated by The Stack, the effective integration of SPF with air barrier systems results in improved energy efficiency, reduced environmental impact, and enhanced building durability. This promotes wider adoption within the construction industry, ensuring buildings perform at their best, supporting sustainability goals, and providing comfortable, efficient environments for occupants.
Author
Mickel Maalouf is a LEED green associate and sustainable building science manager with Huntsman Building Solutions (HBS).
Great article, very useful information