Circular strategies: Extending the life of existing buildings
By Dwayne Torrey
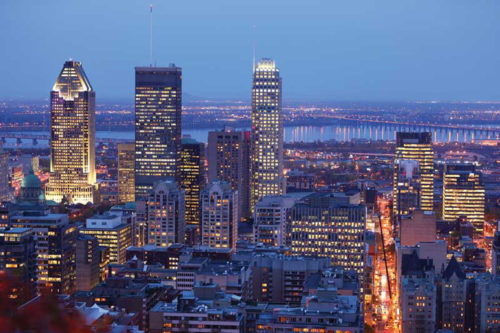
While Canadians often think of cars and heavy industry as the most significant contributors of greenhouse gas (GHG) emissions, the buildings people live and work in should not be ignored. According to the Canada Green Building Council (CAGBC), the operation of buildings alone is responsible for 17 per cent of Canada’s total carbon emissions. This number skyrockets to 30 per cent when embodied carbon emissions are taken into account, as this is the pollution generated from manufacturing, transportation, installation, maintenance, and disposal of building materials.
With Canada’s population expected to rise by approximately 25 per cent between 2018 and 2049, the demand for new buildings is set to soar. As the construction industry prepares for this influx of residents, it is crucial to re-evaluate the approach to construction to ensure a sustainable future.
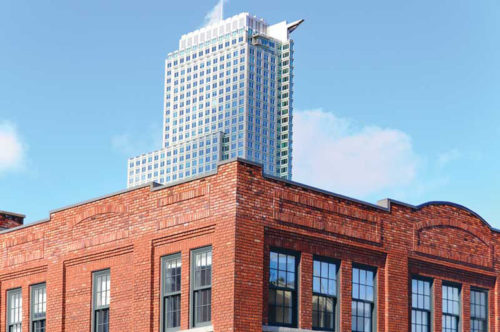
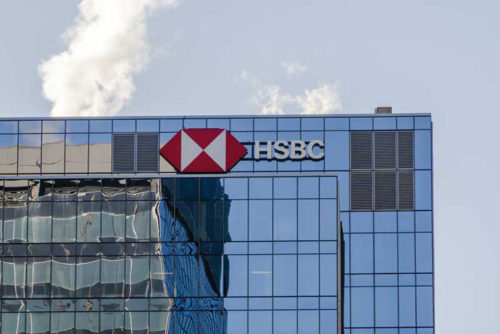
Retrofit versus demolition
One critical decision facing the construction industry is whether to retrofit existing buildings or opt for demolition and new construction.
Retrofitting a building involves making modifications or additions to an existing structure to improve its functionality, energy efficiency, safety, or esthetics. Extending the life of an existing building is a key principle of the circular economy—an alternative to the linear “take-make-use-dispose” system. This starts with designing building or construction materials to be durable, easily repairable, refurbished, disassembled, and reused indefinitely. Transitioning to this circular approach can help to significantly diminish resource demand, eliminate waste, and reduce pollution.
CSA Group’s research report Exploring Circular Strategies to Extend the Life of Existing Buildings1 presents a case study on the entire life cycle environmental impact of six buildings across three major Canadian cities: one high-rise and one low-rise in Toronto, Edmonton, and Vancouver. In each case, retrofitting resulted in significantly lower whole-life emissions than demolition and new construction. The most significant reductions were seen when a large part of a project’s lifespan emissions came from the materials used.
One example of the value of retrofitting an existing building is the 16-storey HSBC Place in downtown Edmonton. Stripping the structure and integrating modern systems within a refreshed envelope, not only spared the environmental impact of demolition, but also garnered various sustainability certifications when it was completed in 2020.
Alternative circular options
While the research shows retrofitting existing buildings leads to 26 to 70 per cent lower whole-life carbon emissions compared to demolition and new construction, sometimes retrofitting is not feasible or practical. However, this does not mean sustainable options are off the table.
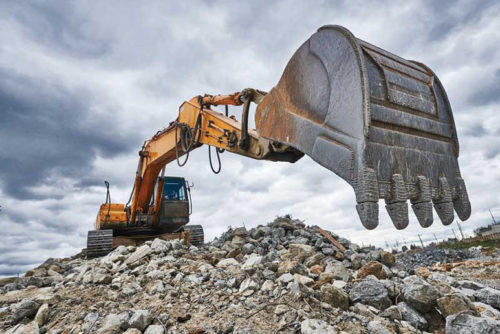
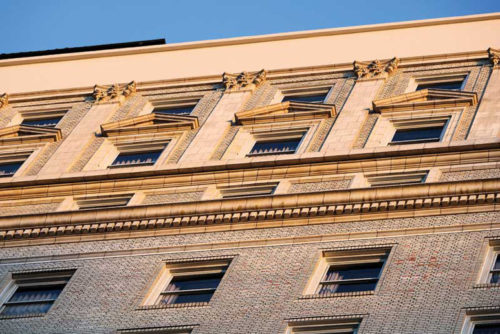
If new construction is required, it is beneficial to prioritize low embodied carbon materials, such as low-carbon concrete and steel, and bio-based materials such as wood.
It is also important to think of the waste created during demolition and construction. A significant portion of demolition materials in Canada ends up in landfills and a considerable percentage of construction materials is wasted during the building process. For instance, in 2015, non-residential activities in Canada generated approximately 1.5 million tonnes (1.65 million tons) of waste,2 with a staggering 95 per cent produced during renovation and demolition phases. Only 27 per cent of construction, renovation, and demolition waste is diverted from landfills, representing missed economic opportunities and untapped resources.
Some options to divert waste from landfills include carefully dismantling buildings to salvage reusable materials for use in other construction projects and transforming salvaged materials into other products such as furniture.
Moving forward
While many circular strategies are already in practice in Canada on an ad hoc basis, there is room for wider adoption. However, this transition requires more than just industry initiatives. Policy support, financial incentives, and voluntary programs play crucial roles in incentivizing circular practices. Standardization is also important to help ensure consistency and accuracy in information and practices associated with products and buildings. CSA Group’s research has identified gaps in local policies, building regulations, data management, procurement standards, and industry training—hindering the widespread adoption of circular strategies.
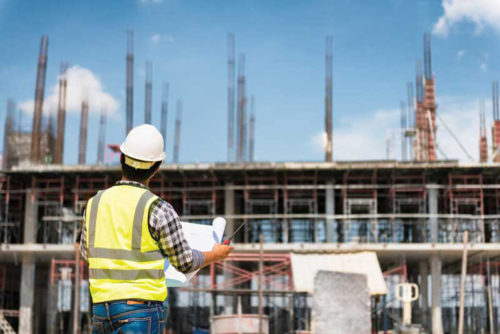
Commercial real estate (CRE) plays a crucial role in driving sustainability initiatives within the construction industry. With commercial buildings accounting for 25.5 per cent of total floor space in Canada, according to Natural Resources Canada (NRCan), there is a significant opportunity to implement circular economy practices and reduce carbon emissions. Larger CRE projects often have the resources and capacity to be early adopters of innovation, paving the way for sustainable practices to become the norm across the industry.
With the construction industry poised for growth, there is a unique opportunity to shape a more sustainable future. CSA Group will continue to research this area while collaborating with other organizations, including Circular Economy Leadership Canada (CELC).3
Embracing circular economy principles, prioritizing building retrofitting, and reimagining the way buildings are designed, constructed, and operated are important steps that can contribute to achieving Canada’s climate targets and help pave the way for a greener, more resilient built environment.
Notes
1 Access the full report at www.csagroup.org/article/research/exploring-circular-strategies-to-extend-the-life-of-existing-buildings.
2 Review “Characterization & management of construction, renovation & demolition waste in Canada,” by G. A. Perry and M. VanderPol, presented at RCA Conference, Lake Louise, Alta., Oct. 1-3, 2014.
3 There are several CSA Group reports that delve into more specifics available online, such as The Circular Built Environment in Canada: A Review of the Current State, Gaps and Opportunities and The Circular Built Environment in Canada: A Strategic Framework for Future Action.
Dwayne Torrey is the director of construction and infrastructure standards at CSA Group, a global organization dedicated to safety, social good and sustainability. In his role, Torrey is responsible for developing the strategic path for Canada’s built environment standards through continuous assessment of emerging construction trends and critical issues. He provides oversight to more than 250 codes and standards focused on safety and reliability of structures, construction materials, products, systems, and mechanical safety equipment. Torrey has more than 25 years of experience in construction and engineering.