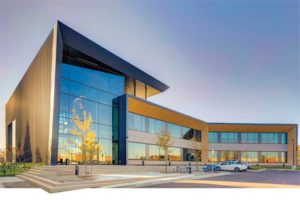
By Greg Koch
As energy codes and sustainability standards continue to drive industry innovation, specifiers can now choose curtain wall systems that waste significantly less energy than their predecessors.
Some manufacturers are using fibre-reinforced polymer (FRP) technology to create curtain wall components, reinforcements, and pressure plates that can be incorporated into the hollow chambers of aluminum frames to significantly bolster the system’s overall energy performance.
During the energy crisis in the 1970s and 1980s, it was discovered that a thermal break in the middle of an aluminum frame could deliver much greater thermal efficiency. Since then, this technology has progressed, but very slowly. From polyamide 6.6 to today’s polyester and polyurethane thermal blocks, and new part innovations, the industry is beginning to develop more ways to use FRP technology. It has been a very slow process, but material developments in this sphere are now gaining in popularity.
FRP materials can be manufactured with the same strength and stiffness as metal, and they exhibit almost zero creep under structural loads. FRP components possess a flexural modulus of up to 51,710 MPa (7,500 ksi), versus the flexural modulus of aluminum, which is 68,947 MPa (10,000 ksi). This difference of 25 per cent allows FRP materials to have 25 per cent more relevant cross-sectional area to match the strength of aluminum. This also provides them with higher resistance to linear compression, screw pull-out, abrasion, cracking, splitting, and flexural fatigue. They are also unaffected by environmental conditions such as salt air/water corrosion, water absorption, extreme hot/cold climates, and common chemicals. The result is a material as strong as aluminum yet boasting better environmental and thermal properties.
In terms of thermal efficiency, FRP materials can boast up to 900 times the thermal effectiveness of aluminum.2 This translates to savings for large-scale commercial structures. It helps structures make the most use of the energy being used to moderate their interior temperatures by not allowing nearly as much heat loss or gain to occur through the building envelope.