Sustainable construction practices with concrete masonry
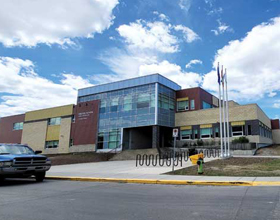
By Mark D. Hagel, PhD., P.Eng, Mike Lafontaine, CTR., SSG., SD
Hollow concrete block masonry was first used as a building material around 1870, when wooden moulds were developed to produce concrete block units from a relatively dry mixture of sand, cement, and water. Around 1900, the first cast iron block producing machine was patented and a decade later, there were more than 1,000 producers of concrete block in North America.
In current construction, concrete masonry units (CMUs) are used as both structural and architectural building materials. CMUs are ideal candidates for carbon dioxide (CO2) sequestration because they are porous and carbonate quickly when left exposed to the atmosphere (weathering carbonation) and can also be cured with CO2 in a closed chamber with either low pressure or high-pressure steam (pre-carbonation). For CMUs, CO2 absorption by mass of cement binder is roughly 6.3 per cent. This translates to approximately 0.250 kg (0.5 lb) of CO2 sequestered per standard 198 mm (7.8 in.) hollow CMU. The carbonation of concrete masonry is not only environmentally friendly, but it can also achieve higher early strength.
Concrete block masonry and architectural block masonry also support resilient building. The more extreme weather events being experienced in Canada can be mitigated with concrete masonry as it is fireproof, highly impact resistant, and can store moisture without degradation. A fireproof material provides resiliency against forest fires, while the high impact resistance provides resiliency against hail damage and impact damage during high wind events such as tornadoes. Concrete masonry’s ability to store water provides resiliency against floods and can also reduce water loads on storm water systems when used as veneers, as concrete masonry can absorb more water during heavy rain events than siding or glazing, which shed water to the ground and storm drains, and they can absorb water without degradation to the cladding. Although there is no lab testing for resiliency against floods, there is decades of proven performance where concrete block does not mould rust, or rot. The location of the rebar, when fully grouted, provides adequate protection for a single wythe masonry wall, 95 mm (3.7 in.) of concrete cover for rebar, and is typically protected by an air vapour barrier that is highly resistant to even standing water.
Achieving more climate friendly concrete masonry involves reducing the amount of embodied carbon, as well the amount of operational carbon in the buildings constructed with concrete block masonry. Embodied carbon is the carbon emissions resulting from the extraction, manufacturing, delivery, and installation and disposal of the product, whereas operational carbon are emissions resulting from use of the building such as HVAC, lighting, and power. With concrete masonry, substituting Portland Limestone cement (GUL) for General Use Portland cement (GU) in the manufacture of concrete masonry products and accelerating carbon sequestration by pre-carbonation can reduce embodied carbon emissions. Operational carbon can be reduced by taking advantage of the thermal mass effects of concrete masonry and improved thermal modelling to create concrete masonry assemblies that mitigate the loss of thermal energy and reduce the amount of heating or cooling a building requires during operation. Concrete masonry can be used to create backup walls and claddings that can meet the requirements of net-zero energy building envelopes, eliminating operational carbon from heating. Their long service lives with very little maintenance require concrete masonry buildings and offer an even better carbon footprint when the embodied carbon and operational carbon are amortized over the life of the building. These products are cradle-to-cradle rather than cradle-to-grave, as concrete masonry is 99 per cent recyclable at the end of service.
This article will explore Environmental Product Declarations (EPDs) currently available for concrete masonry products and carbon sequestration of concrete masonry units in the forms of weathering carbonation and pre-carbonation of CMUs. The article will also explore achieving net-zero energy buildings (passive house) by introducing improved values to more accurately account for thermal bridging in concrete block-brick veneer walls and explained using a low-rise concrete masonry building achieving the net-zero energy requirements for opaque and fenestration and doors of passive house.1 The article will conclude with the benefits of the thermal mass effects of concrete masonry on reducing operational carbon.
EPDs for concrete block
An Environmental Product Declaration (EPD) is a document that communicates the environmental impact of any product or material over its lifetime. In the construction industry, EPDs support carbon emission reduction by providing comparisons of the impacts of different materials and products to select the most sustainable option. Architects, engineers, and designers can choose the most sustainable option for their project, while manufacturers are able to optimise the impact of their products and market their carbon transparency. An EPD is usually valid for five years, and is generated according to ISO 14040/14044, ISO 14025, EN 15804, or ISO 21930 standards.2