Assessing mass concrete with thermal control plan
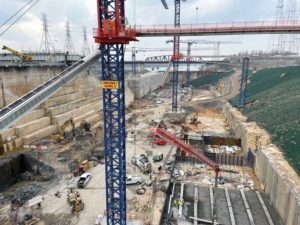
By Eric Van Dixhorn
As schedules on construction projects continually accelerate and service life requirements become more demanding, structures are being built larger and to last longer. As a result, more attention has been placed on the internal heat generation that takes place while the concrete cures. If ignored, this heat can lead to thermal cracking and reduced long-term strength. Concrete elements that require a thermal analysis are labeled as “mass concrete.”
Traditionally, mass concrete is widely used in dam structures, bridge piers, mat foundations, and other large structures that require substantial volumes of concrete. Thermally controlled concrete (referred to here as mass concrete), which may not have the same volume and dimensional characteristics as traditional mass concrete that may be found in a bridge footing or pier cap, but it also requires thermal considerations because of the higher cementitious content that leads to high internal temperatures.
There is no universal definition of mass concrete. In many cases, if the element’s smallest dimension is greater than 1.2 m (4 ft), then it should be categorized as mass concrete. According to the American Concrete Institute (ACI), mass concrete is “any volume of structural concrete in which a combination of dimensions of the member being cast, the boundary conditions, the characteristics of the concrete mixture, and the ambient conditions can lead to undesirable thermal stresses, cracking, deleterious chemical reactions, or reduction in the long-term strength as a result of elevated concrete temperature due to heat from hydration.” If precautions are not implemented on a mass concrete pour, these undesirable results can have substantial performance, durability, and ultimately financial consequences.
ACI 301, Specifications for Structural Concrete, states the maximum temperature after placement should not exceed 71 C (160 F), and the maximum temperature difference (ΔT) between the core and the surface should not exceed 19 C (35 F)—which is differential and not absolute temperature. In the absence of a more thorough analysis, these are generally considered to be safe and cautious specifications. Thankfully, ACI provides a guide (ACI 207) that allows specifiers and engineers to deviate from these requirements through the development of a thermal control plan (TCP).
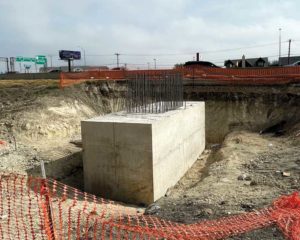
Thermal control plan
A TCP is a document typically prepared by an experienced licensed engineer who is knowledgeable on the thermal behaviour of concrete. A TCP provides a foundation to ensure high thermal stresses and cracking of mass concrete will be avoided, and that its long-term durability will not be negatively affected. This is attained through the control of both the maximum temperature in the concrete (at the core or centre of mass) and the temperature differential between the core and the outside faces of the concrete elements. It is an action plan for the contractor that includes information on mix design optimization, concrete cooling options, allowed concrete temperatures at point of placement, expected temperature rise, requirements for form insulation, anticipated duration of the thermal control period, requirements of the number and location of concrete temperature sensors, and more.