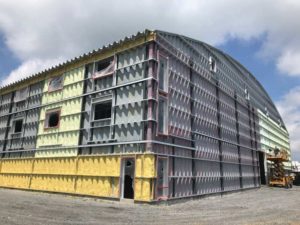
By Maxime Duzyk
The growing demand for energy-efficient and sustainable building solutions drives building engineers and architects to search for innovative and cost-effective ways to optimize insulation. One such cutting-edge insulation technology is hydrofluoroolefins-blown (HFO-blown) spray foam insulation, a high-performing, eco-friendly alternative to traditional insulating materials such as fibreglass or mineral wool. The true strength of HFO-blown spray foam insulation lies in its versatility, with its ability to function as an effective air barrier and waterproofing solution, and as a high-performance insulation.
This article will dive into the many benefits of HFO-blown spray foam insulation, from its unparalleled R-value, flexibility, how it can function as an air barrier and waterproofing solution, and how it alleviates pain points often experienced by building professionals, architects, and contractors.
Overview of HFO-blown spray foam insulation
HFO-blown spray foam insulation is a two-component, polyurethane-based foam applied using specialized spray equipment. The foam is created from a combination of hydrofluoroolefin (HFO) blowing agents and other chemicals, resulting in a lightweight, high R-value insulation material. The HFOs used as blowing agents have a significantly lower global warming potential (GWP) than traditional hydrofluorocarbon (HFC) blowing agents, making them a more environmentally friendly choice. In the past, HFC-blown spray foams cultivated a somewhat negative reputation, due to their high GWP. The GWP difference between HFC and HFO blowing agents is a 99.9 per cent reduction.1 In addition, HFO blowing agents have zero ozone depletion potential (ODP), making them a more climate-friendly option in more ways than one.
Some high-quality spray foam insulation products even offer a product-specific environmental product declaration (EPD), which is a rare sight seeing as most products are backed by industry average EPDs. Through this EPD, top-tier products are shown to possess a GWP of 39 per cent lower than the industry average for HFO spray foam, which is up to 96 per cent lower than HFO blowing agent extruded polystyrene (XPS), and 77 per cent lower than high density mineral wool. These numbers comparing the GWP potential consider everything, from the manufacturing of the products to their end of life, which is estimated at 75 years.
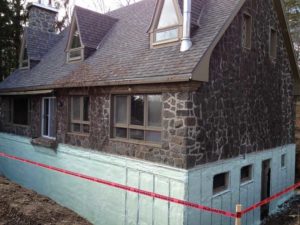
Designing and specifying buildings for the future is not just about reducing carbon emissions during construction, but also for the lifetime of the building, and in its actual day-to-day use. For all sorts of projects, this translates to lowered energy usage by residents and users, as they enjoy more efficiently insulated buildings, leading to reduced operational carbon emissions for decades to come.
Upon application, closed-cell spray foam rapidly expands to fill gaps, cracks, and other openings, forming a seamless, continuous layer of insulation. As it cures, the foam hardens and adheres to the building’s structural elements, effectively creating a monolithic building envelope that is both energy-efficient and resistant to moisture, air infiltration, and thermal bridging. The ability of spray foam to fill gaps, cracks, and other openings so efficiently greatly contributes to its effectiveness as an air barrier.
Air barrier capabilities
One of the most significant advantages of HFO-blown spray foam insulation is its ability to serve as an air barrier. Traditional insulation materials, such as fibreglass or mineral wool, are often unable to prevent air infiltration effectively, leading to energy loss and higher utility bills.
You have so incredible knowledge to share with others. Regards for spreading it. Please keep supporting us by giving us the services of the spray foam insulation Barrie