Waterproofing construction joints
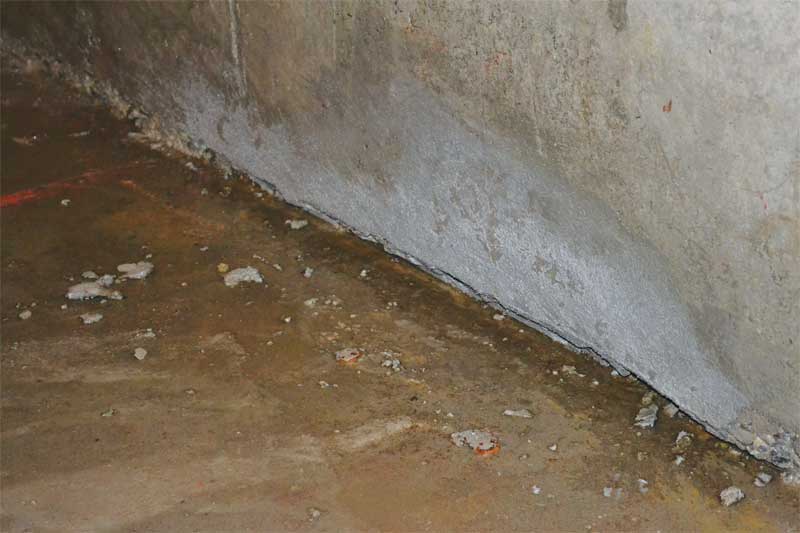
Images courtesy Kryton International
Correct products create correct systems
When discussing the waterproofing of a concrete structure with below-grade aspects, it is important to consider complete systems rather than individual products. For instance, using just an external membrane to waterproof a concrete structure leaves other, overlooked aspects at risk. The same can be true for other surface-applied membranes, as well as integral waterproofing products. These products are only components of concrete waterproofing—more is needed to make a completely watertight structure.
In fact, the American Concrete Institute (ACI), an authority on concrete best practices, has communicated a complete waterproofing system is needed. (For further reading, visit www.concrete.org.) The revised edition of ACI 212.3R, Reports on Chemical Admixtures for Concrete, calls for the use of a waterstop and other products to supplement the main waterproofing aspect. That is, a complete system, rather than a single product, must be used to effectively waterproof concrete structures.
ACI 350, Code Requirements for Environmental Engineering Concrete Structures, supports this point in more general terms, pointing out the correct waterproofing system will fully protect a concrete structure from water ingress when combined with the correct jointing system. Put plainly, a waterproofing system needs to be supplemented by a jointing system to have waterproofing success.
Regardless, in some circumstances, the construction joints and penetrations of concrete—which provide a path for water and waterborne chemicals—are overlooked. A construction joint is created when one slab or form of concrete ends and another begins. This forms a weak area where water can infiltrate the concrete structure.
The different kinds of joints are:
- expansion joints (separations between adjoining parts of a structure to allow movement from thermal expansion);
- control joints (created to prevent random cracking in concrete for ease of fill once hardened); and
- construction joints (stopping points in the construction process where new concrete is poured against existing concrete).
Over time, it is quite common for a construction joint to start leaking water, especially in below-grade applications where hydrostatic water pressure is present. In fact, construction joints and penetrations are the most common cause of leakages in a below-grade structure. Protecting the joints in concrete is therefore vital, especially considering the disastrous implications if ignored or when the correct product within the correct system is not used. Due to the presence of this water pressure in many below-grade concrete structures, the designer usually specifies some type of joint protection material.
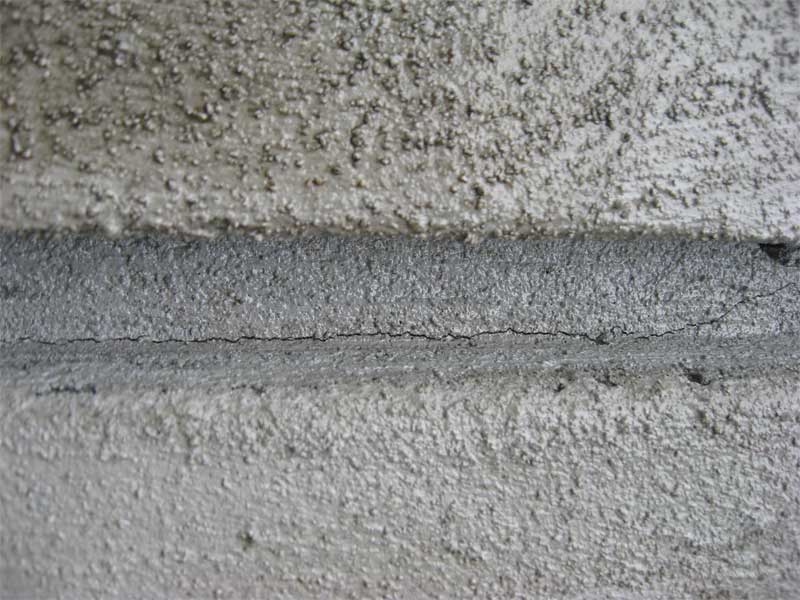
Joint protection
To ensure a concrete structure is completely watertight, all aspects—including the construction joints—must be protected. Waterproofing systems are normally supplemented, in specifications or otherwise, through some type of waterstop. The waterstop is placed at the construction joints, with concrete then poured over it. As water infiltrates the joint, the waterstop blocks or absorbs the moisture, stopping it from proceeding through the entire joint.
There are a number of different options and materials available for waterstops, including:
- polyvinyl chloride (PVC) waterstops;
- bentonite strips;
- synthetic swelling rubber strips;
- injection hose systems;
- metallic extrusion; and
- rubber non-swelling strips.
For the most part, the first three technologies dominate the waterstop landscape. These products are placed between the rebar of a construction joint and either nailed or glued into place before concrete is poured. As concrete shrinkage occurs, the waterstop fills the space in the concrete joint and blocks the flow of water.