Specifying structural steel for bridges
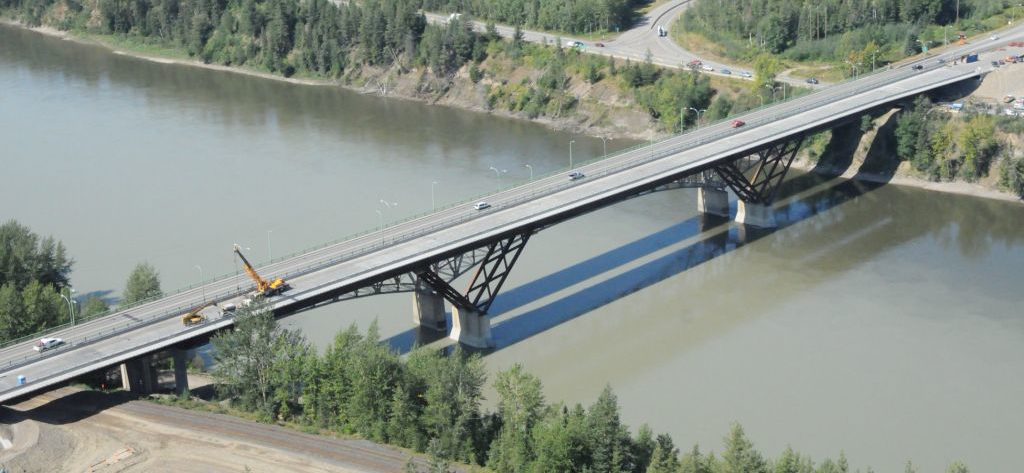
By Peter Taylor, PhD., P.Eng., PE, and Andrew Brooks
Canada’s urban infrastructure growth is creating significant demand to increase the capacity of major waterway crossings, either by widening or replacing existing bridges, or building on new alignments. This article examines four major bridge projects in Québec and British Columbia.1
Canada has an extensive bridge infrastructure, but the country’s population is relatively small. Therefore, designers are accustomed to creating understated, cost-effective bridges constructible in the climate. The growing use of design-build delivery methods meets these criteria and adds the discipline of tight schedules.
Structural steel was selected for these projects because it enabled design solutions that best met the above criteria. The material provides design versatility, and its high strength-to-weight ratio enables longer spans for bridges, effective seismic performance, durability, and sustainability. Areas relating to code compliance, safety, security, innovation, and the environment are all key issues related to bridge building.
The Canadian Institute of Steel Construction (CISC) is developing future bridge inspection programs in an effort to optimize decision-making for replacement, restoration, and maintenance issues. More than 40 per cent of Canadian bridges currently in use were built over 50 years ago (Figure 1) and a significant number of these structures need reinforcement, rehabilitation, or replacement.
Steel has high tensile and compressive strengths, easily meeting structural requirements. Further, the installation of steel bridges can be more versatile and efficient than other traditional materials. It offers cost savings in using skilled labour, as steel is produced in the workshop. Transportation, demolition, and facility in conducting repairs are also strong advantages offered with steel bridge construction. The material’s capacity to better withstand stress and fatigue, and its higher seismic resistance, are also benefits. Steel bridges also offer economic advantages, are durable, and are adaptable to different locations.
Autoroute 25 completion project in Montréal
Autoroute 25 is a $485-million public-private partnership (P3) project that comprises 7.2 km (4.5 mi) of highway, 10 grade-separation structures, and a 1.3-km (0.8 mi) bridge crossing the Rivière des Prairies in Montréal. At the crossing location, the river has environmental constraints in the shallow water at the south side and protected sturgeon habitat in the main channel. Innovative design and construction practices were necessary to deal with not only these constraints, but also difficult river conditions and an aggressive project schedule.
The selection of structural steel framing for the 632-m (2073-ft) south approach permitted girder fabrication to proceed during the site’s winter shutdown. The concrete deck was supported by five steel plate girders 3.7 m (12.1 ft) deep, which were continuous over seven spans. The length, height, and weight of the girder segments were optimized for over-land shipping and erection efficiencies, and the shear studs were shop-installed to minimize fieldwork.
Girders were erected with a gantry travelling along falsework trestles on each side of the approach spans. Each girder was supported on lead-core rubber bearings, which, through their deformation, accommodate the thermal and seismic movements of the continuous girders and distribute the horizontal loads uniformly to each pier.
The bridge over the main channel is cable-stayed, similar to the steel Pont Papineau bridge a few kilometres upstream, with a span of 280 m (918 ft) and two sidespans of 116 m (380 ft). The bridge towers consist of twin concrete columns 70 m (229 ft) high with a single cross-strut beneath the deck. For simplicity, the cables and edge girder are aligned on the tower centreline. The tower columns obstruct the in-line continuity of the edge girders, which is necessary for transferring the girder thrust.
As with typical composite cable-stayed construction, the concrete deck is fully composite with all steel-framed elements. It is supported by 80 stay cables.
Port Mann Bridge in Vancouver
Unlike Autoroute 25, which was an entirely new section of infrastructure, Vancouver’s $2.5-billion Port Mann Bridge/Highway 1 project involved construction of a 10-lane bridge across the Fraser River, and an upgrading of the capacity of 37 km (23 mi) of the Trans-Canada Highway. Undertaken to relieve traffic congestion, the project was financed publicly, but will be paid for by tolls.
Built under a design-build contract, the bridge over the Fraser River is a three-span composite cable-stayed structure with spans of 190, 470, and 190 m (623, 1541, and 623 ft). Its twin decks are approximately 23 m (75 ft) wide, and on each side of 158-m (518 ft) high slip-formed concrete pylons where the four planes of cable stays are anchored. Steel tie boxes cast into the upper pylons incorporate the upper stay anchors. The lower stay anchorages are attached to brackets cantilevered out from the girder webs.
The twin decks are separated by pin-ended struts and will be supported by 288 cable stays having 23 to 73 strands per cable. The superstructure is being erected by deck-mounted derricks.
The twin deck concept with a single central pylon and four planes of cables was first used at Ting Kau Bridge in Hong Kong. Similar to that structure, the new Port Mann Bridge has outriggers below the deck at each pylon to support bracing cables for the upper pylon.
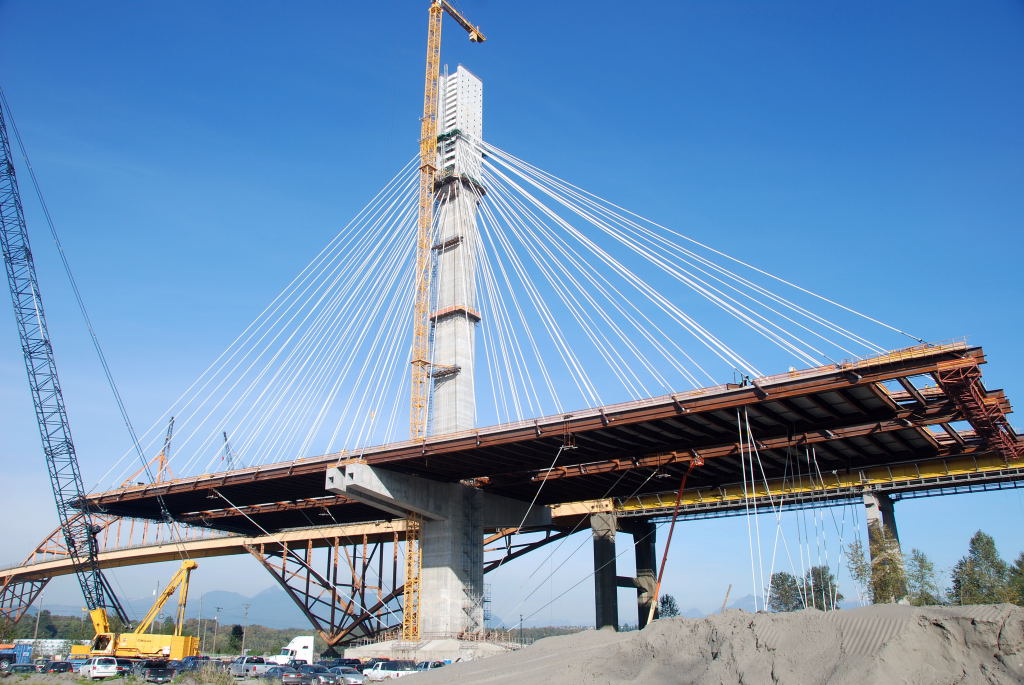
Simon Fraser Bridge–Prince George, B.C.
The existing two-lane truss bridge at Prince George also crosses the Fraser River, but more than 500 km (310 mi) upstream of Port Mann Bridge. It also was experiencing traffic congestion and the Ministry of Transportation and Infrastructure of British Columbia decided to commission a design for the addition of two more traffic lanes.
The existing truss spans 127 m (416 ft) between piers; it was clearly desirable to match pier locations for the new twin two-lane structure. Plate girders offered the most economical solution, but deep girder sections would be necessary to match the existing span. The height of the bridge deck above the Fraser River permitted the insertion of steel delta frames below deck level, which in effect reduced the span of the girders. This innovative solution had two benefits:
- It permitted the twin structure to share the same pier spacing as the existing bridge.
- It allowed the use of economical plate girders only 2.7 m deep.
Heavy shop-welding was necessary to achieve load transfer into the delta legs; they were trial-assembled to ensure field fit-up.
The new twin bridge has a total length of 400 m (1312 ft), and supports a concrete deck with two traffic lanes and a wide sidewalk on three composite plate girders, giving it structural redundancy. Each plate girder is supported by a steel delta frame that sits on one of the new concrete piers. In turn, these are supported by steel pipe piles drilled into the riverbed. The total weight of structural steel amounts to 344 kg/m2 (70.3 lb/sf) of deck area.
Autoroute A30 project—Montréal
The $1.5-billion A30 project is a new 42-km (26-mi) section of urban infrastructure that completes the urban highway connection along the south shore of the St. Lawrence River to the westbound Highway 20 leading to the Ontario border. The terms of the P3 were signed in 2008, with the project completed four years later.
The most difficult component of this project was the 2550-m (8366-ft) highway bridge at Beauharnois. At this location, the power canal carrying water to the Hydro Québec Generating Station immediately downstream is side-by-side with the Beauharnois Lock of the St. Lawrence Seaway. The bridge crosses both waterways.
The project design criteria penalized flow obstruction by bridge piers or construction activities in the power canal. Also, a high 38-m (124-ft) clearance box was required over the seaway, and span erection there was only permitted during the short mid-winter closure to shipping. Both these design challenges were met with use of structural steel.
Long spans of 81.9 m (268-ft) with few piers were achieved in the power canal by employing composite trapezoidal box girders. Each girder supports three lanes of traffic and is 3.7 m (12.1 ft) deep and 7.2 m (23.6 ft) wide at the top flange. The steel boxes weighed up to 300 tonnes each and were shipped to the site by barge. Erection of the box girders was by push-launching from the east abutment, which meant no erection equipment was required in the channel.
The mainspan crossing of the Seaway at 150 m (492 ft) is longer than the typical east approach span and the navigation clearance box extends close to the piers, which are sited beside the lock. This geometry did not permit delta frames, as were used at Simon Fraser Bridge, nor did it permit normal girder haunch profiles without significant elevation of the highway grade. This resulted in an increase in approach bridge length.
The design resolved the geometric challenge by adding triangular reinforcing elements at each main pier. These were field-connected beneath each typical box after the box girder had been launched over them, using a temporary cable stay for the 150-m launch.
Conclusion
These four different projects illustrate the versatility of composite structural steel in meeting the design and construction challenges of Canadian bridges. The Simon Fraser Bridge in Prince George and the Beauharnois Bridge in Québec each show how innovative design of the girder support details at the piers permitted the span of simple economical steel framing to be stretched to meet project span demands.
Further, the A25 and Beauharnois bridges both used innovative framing and original erection schemes to meet environmental challenges in their approach spans. The competitive design-build environment at both A25 and Port Mann bridges demonstrated once again the advantages of composite steel plate girder framing for these major cable stayed bridges.
Notes
1 An earlier version of this article appeared in the Spring 2012 issue of Advantage Steel Magazine. (back to top)
Peter Taylor, PhD., P.Eng., PE is the co-founder of Buckland & Taylor Ltd. He has spent 48 years working in the design and construction of bridges in Canada, North and South America, Europe, and China. Taylor can be reached by e-mail at prt@b-t.com.
Andrew Brooks is a Toronto-based freelance writer and editor. He works in a wide range of sectors, including construction, transportation, airport management, automotive, information technology, and steel fabrication. Brooks can be contacted at ahbrooks@rogers.com.