Rehabilitating Runnymede Subway Station: Maintaining service with accelerated construction
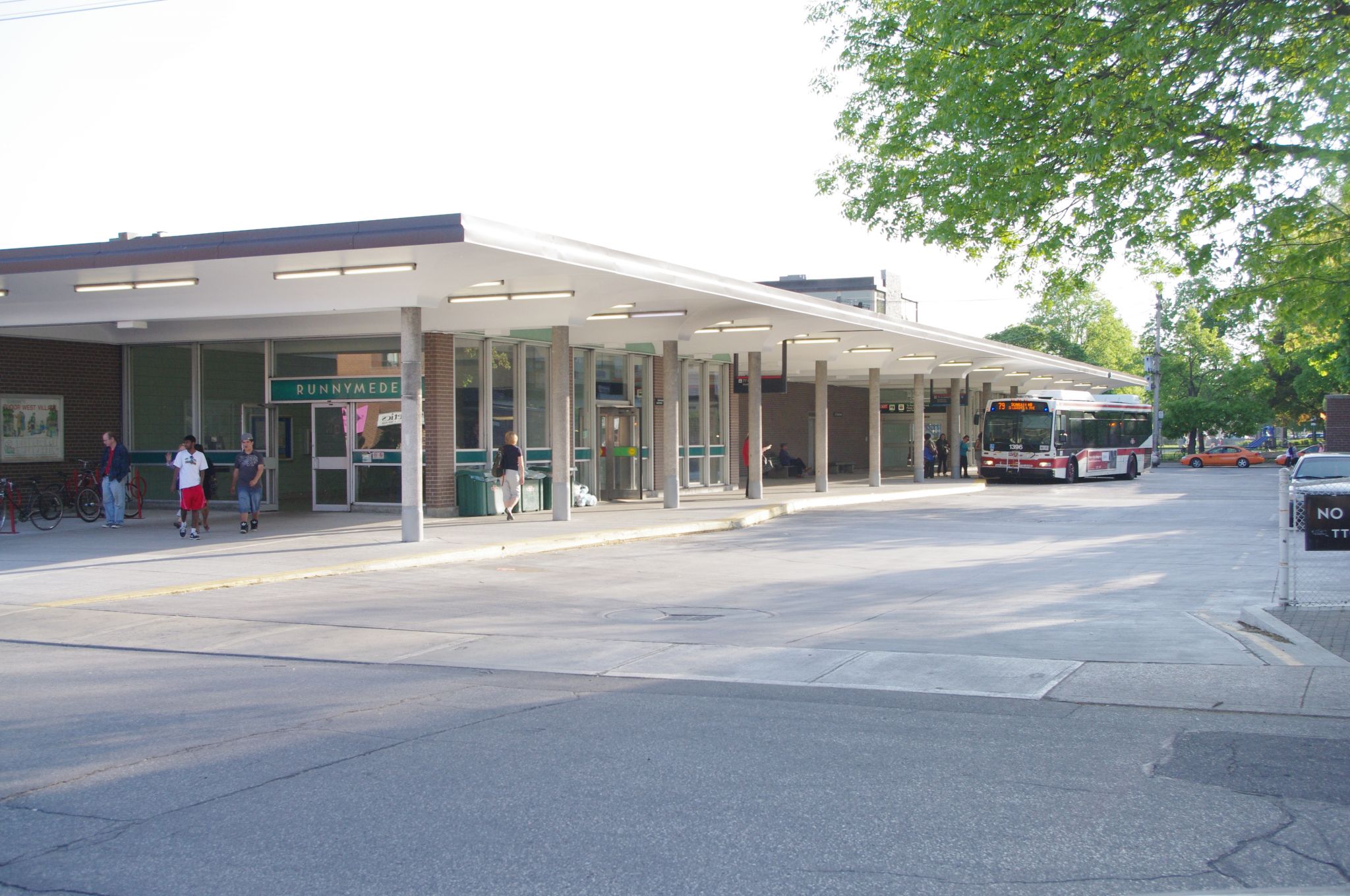
By Sameh Salib, PhD, P.Eng., BDS, PE, and Jonathan Werner, M.A.Sc., P.Eng.
Infrastructure maintenance has been a major concern all over the world, especially in countries with a cold-winter climate. Full or partial shut-down of transit-related facilities during rehabilitation imposes significant inconvenience to the public.
The project presented in this article represents an innovative approach to infrastructure rehabilitation in general, and for the subway sector in Canada, in particular. The developed plan, along with the proposed construction phasing, introduced a new structural slab for a Toronto subway station’s underground structure while maintaining the existing slab in-place.
Traditional slab removal and its associated work of re-routing wiring and utilities in some heavily congested electrical/mechanical areas were completely eliminated. Replacing the entire existing structural pavement and passengers’ platform with new concrete slabs reinforced with advanced composite materials (glass-fibre-reinforced polymer [GFRP] reinforcement bars), as well as strengthening the canopy columns with fibre-reinforced polymer (FRP) fabric wrapping, were also part of the project. All construction was completed while maintaining uninterrupted subway service and with significant savings in both time and cost.
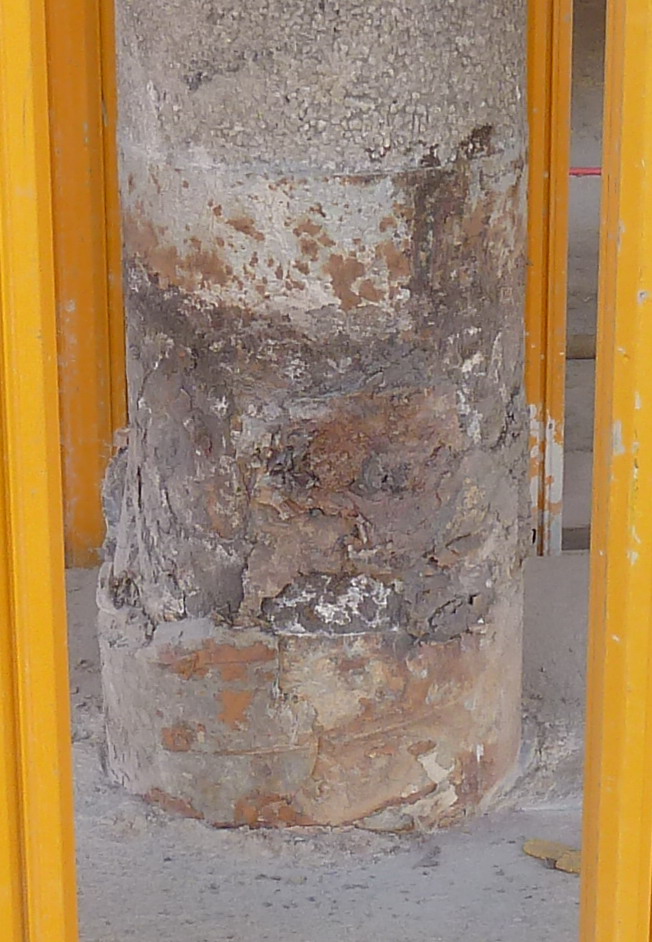
Structure description and existing conditions
The Toronto Transit Commission’s (TTC’s) Runnymede Station has a single at-grade level and two below-grade levels. The latter consists of a mezzanine level just below grade with vertical access to the subway platform at the lowest level. The exterior portion of the grade-level structure serves as a bus terminal, accommodating a driveway and a passengers’ platform covered by a canopy. The ceiling or roof slab for the station’s below-grade mezzanine level is located underneath part of the driveway and platform.
The structural systems in the bus terminal area are primarily composed of conventionally reinforced concrete elements. This includes the canopy columns, the driveway structural paving, and the platform slab. Having been in service for more than 40 years in harsh weather conditions, many structural members were exhibiting significant corrosion, along with concrete delamination and spalling. Some of these elements—such as the mezzanine slab underneath the structural pavement and the steel collars at the canopy column bases—were inaccessible for previous inspection and maintenance, yet they were still subject to significant exposure to water and de-icing salt.
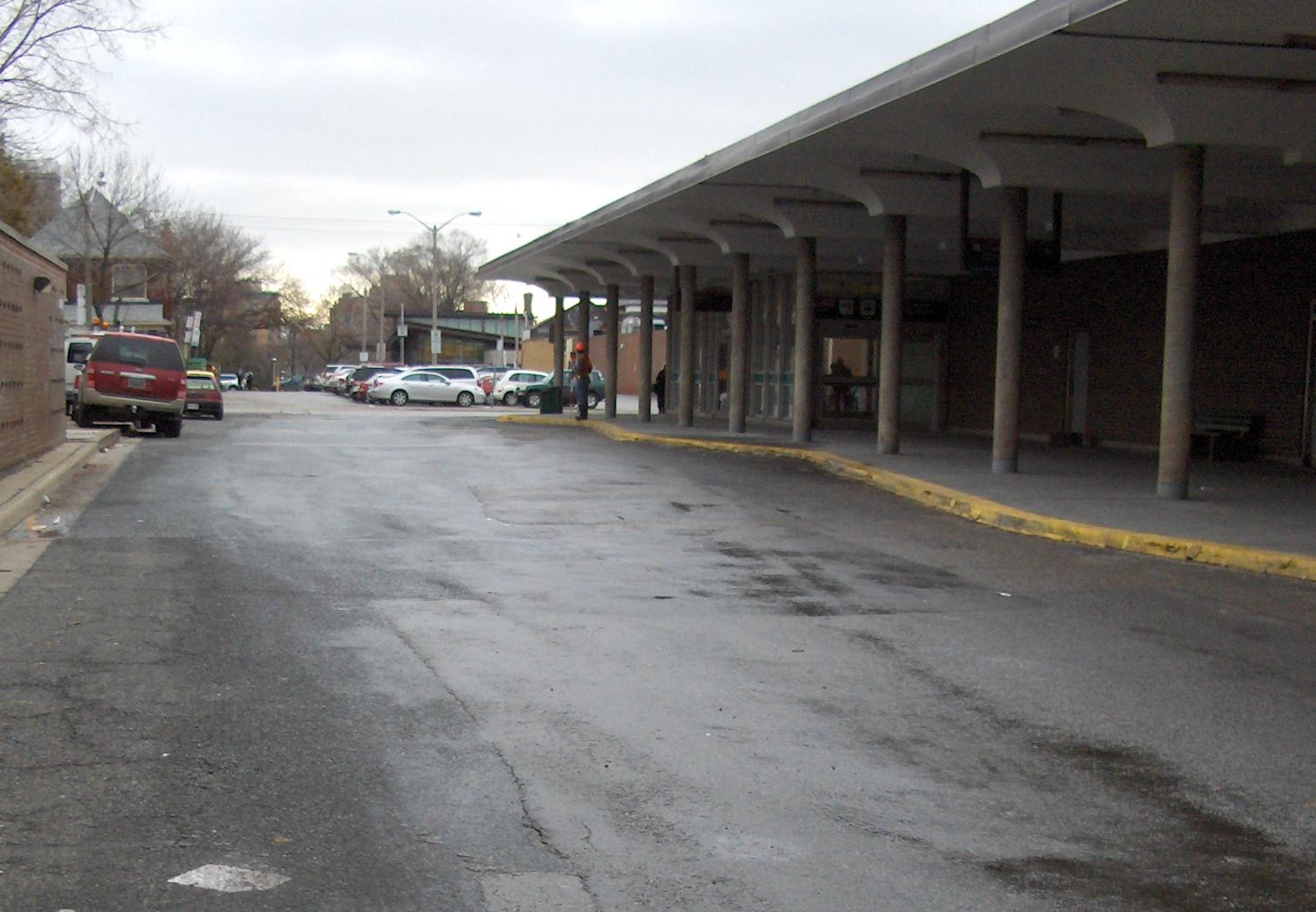
FRPs versus traditional construction materials
Concrete and steel have traditionally been used for rehabilitating existing structures. Reinforced concrete jackets, mechanically fastened steel plates, and external post-tensioning systems have been among the common techniques. Unfortunately, significant changes in the original weight, dimensions, and appearance of the rehabilitated components are usually associated with such techniques. Moreover, durability problems with the rehabilitation system itself, such as steel corrosion and concrete cracking, frequently degrade both structural performance and appearance.
Recently, FRPs have been closing the gap between the structural and architectural demands regarding rehabilitation systems. These products have superior characteristics over steel with respect to tensile strength, weight, and corrosion/chemical resistance. At the same time, the effect of FRP systems on the original weight, dimensions, and appearance of the rehabilitated structural member can be quite minimal.
Further, while conventional rehabilitation systems usually involve major construction work, FRP systems are generally installed in less time and with less effort. Consequently, both the direct cost of construction and the indirect costs associated with the facility shut-down/traffic detours during the rehabilitation process can be significantly reduced.
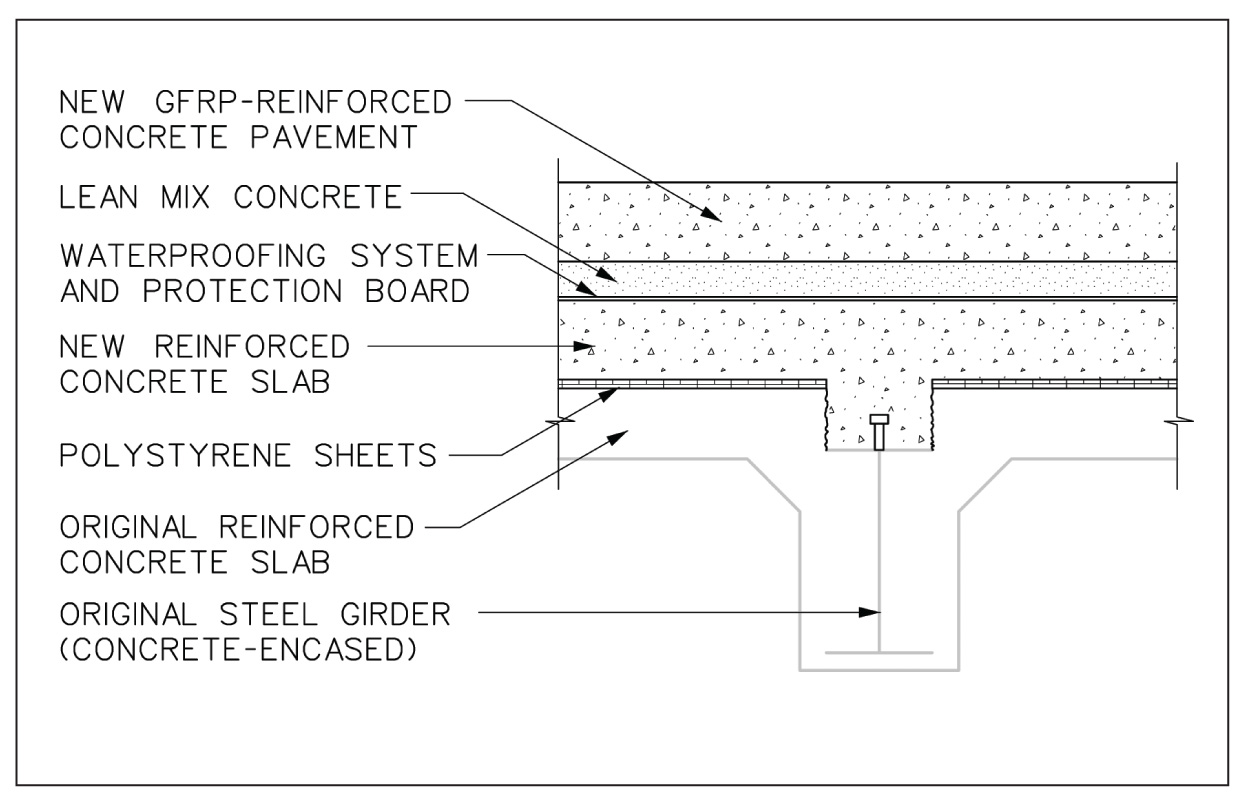
During the last decade, many steel-reinforced concrete structures in Canada have been deemed appropriate for rehabilitation using FRP. In some of these projects, significantly deteriorated elements were replaced with new FRP-reinforced concrete elements. Currently, the design, fabrication, and service life performance of various FRP structural applications are covered by the Canadian Standards Association (CSA), including:
- CAN/CSA 806, Design and Construction of Building Structures with Fibre-reinforced Polymers;
- CAN/CSA 807, Specification for Fibre-reinforced Polymers; and
- CAN/CSA S6-06, Canadian Highway Bridge Design Code (CHBDC).
Rehabilitation requirements
For the Runnymede project, the original scope of the rehabilitation was primarily limited to replacement of the concrete structural paving slab for the buses and the concrete slab-on-grade that forms the at-grade platforms. Some patch repairs to the top surface of the below-grade reinforced concrete mezzanine slab were also expected.
However, after partial removal of the existing driveway concrete pavement and passengers’ platform from around the canopy columns and from over the mezzanine slab, the chloride contamination and concrete delamination levels within the top part of the slab indicated the need for replacement. It was also found the original functions of the deteriorated steel collars at the platform column bases (i.e. structural confinement of concrete and protection from moisture and de-icing salt) needed to be restored.
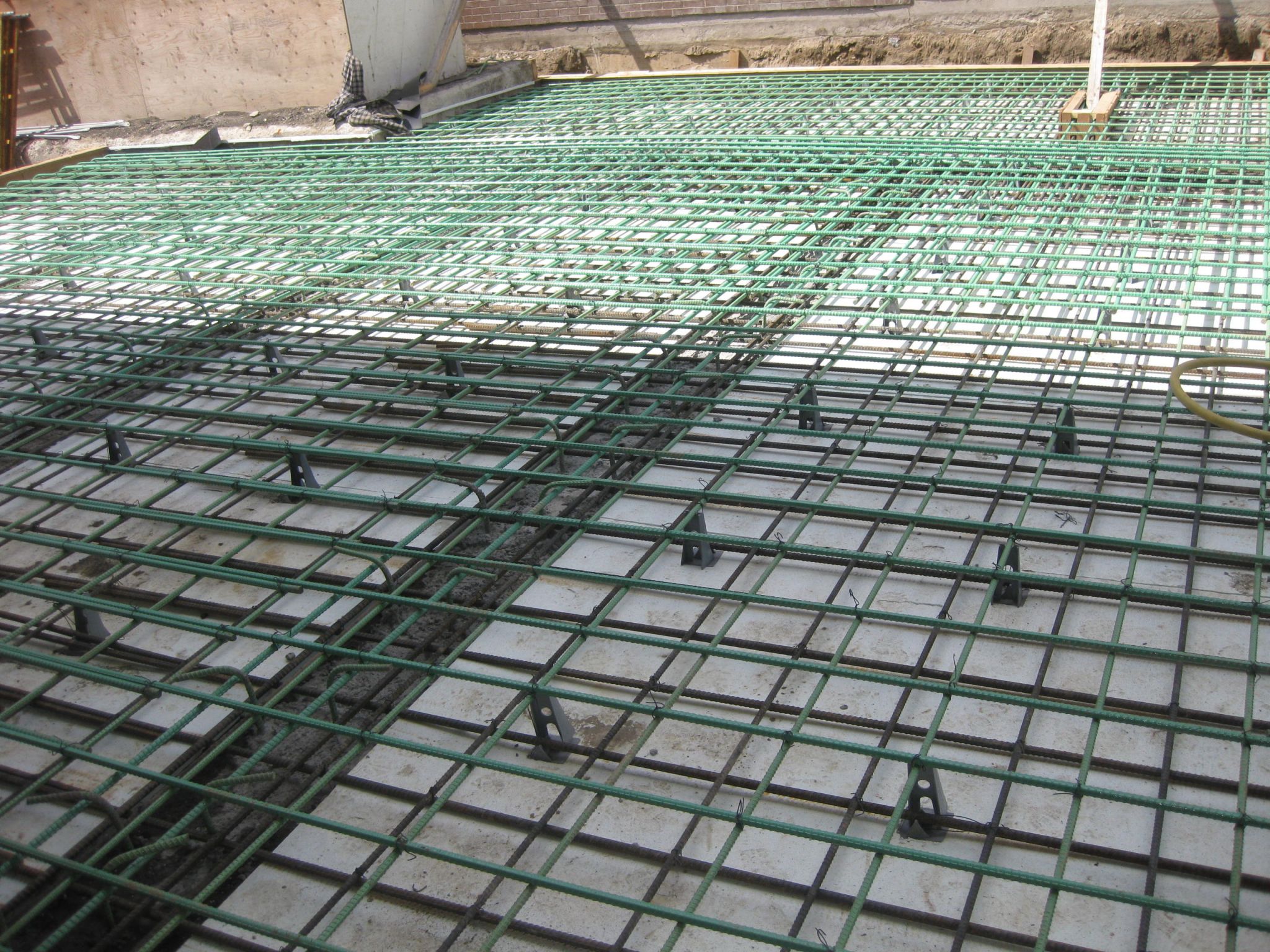
Investigated rehabilitation options
Both conventional and FRP systems were investigated for rehabilitation of the structural components. Rehabilitation methods were assessed, considering esthetics, constructability, and durability. Additionally, the assessment addressed each method’s ability to satisfy the project time and budget constraints not only in the short term, but also accounting for future maintenance, repair, and replacement.
Mezzanine roof slab under the bus driveway
Typically, replacing an existing structural slab has two main steps: the first is to remove the existing slab, and the second is to build the new one. While this may seem to be a simple process, it would have meant a full shut-down of subway station service for months, since removing the existing slab would require full closure of the area below for public safety. Additionally, before slab removal, re-routing the wiring and conduits from underneath the slab would have required weeks of work, especially in the heavily congested electrical/mechanical rooms. Further, after the existing slab was removed, the construction of a new reinforced concrete slab would have required several more weeks for formwork installation.
As an alternative to such a traditional approach, the option of introducing a new slab while maintaining the existing one in place was investigated. This is broken down into a few construction phases. First, the existing slab is shored and then concrete is removed from overtop of the supporting steel beams and concrete walls. During this removal, the existing slab reinforcing steel is maintained. New reinforcing and concrete is placed to form the bearing area for the new slab. Afterward, sheets of compressible material (i.e. expanded polystyrene [EPS]) cover the top surface of the existing slab before placing reinforcement for the new one. This allows use of the existing slab as formwork for placing the new concrete, while keeping the two relatively independent of one another.
Once the new slab’s concrete has reached its specified strength and the formwork shoring is removed, the existing slab is required to carry little more than its own weight and that of the conduits underneath. The original slab, in its current condition, was found to have sufficient capacity to support such loads. Further, having the new and existing slabs relatively structurally independent allows future demolition of the existing slab without compromising the structure’s integrity.
Column bases
A common conventional column repair/strengthening method is to provide a steel-reinforced concrete jacket around each column within original collar height with vertical dowels into the column footing and horizontal dowels into the column. However, the onsite installation cost (time and labour) is relatively high. Further, the new jacket is subject to the same durability problems as all conventional steel-reinforced concrete components (i.e. steel corrosion, rust staining, and concrete spalling/delamination). Having the jackets projecting from the columns above the top of the platform also constitutes a tripping hazard within the pedestrian traffic area.
On the other hand, wrapping the column within the original collar height with FRP fabric requires much less time and labour. The entire process for FRP-wrapping involves preparing the concrete surface, applying resin to both surface and fabric, wrapping the fabric around the column, and curing for a few hours. Then an exterior protective paint is applied with an option of colour-matching the original collar.
Bus driveway pavement and passengers’ platform
Concrete pavements and platforms are traditionally reinforced with standard (i.e. black) steel bars as bottom reinforcement along with an (optional) upgrade to epoxy-coated bars for the top reinforcement. In practice, using epoxy-coated bars delays steel corrosion without solving the problem itself. Over time, rust stains and concrete delamination/spalling will take place requiring localized repair, until replacing the entire concrete pavement/platform becomes the optimal solution. Such frequent repair and replacement cycles, mainly because of steel corrosion, can be significantly reduced through corrosion-free reinforced concrete (e.g. concrete reinforced with GFRP bars).
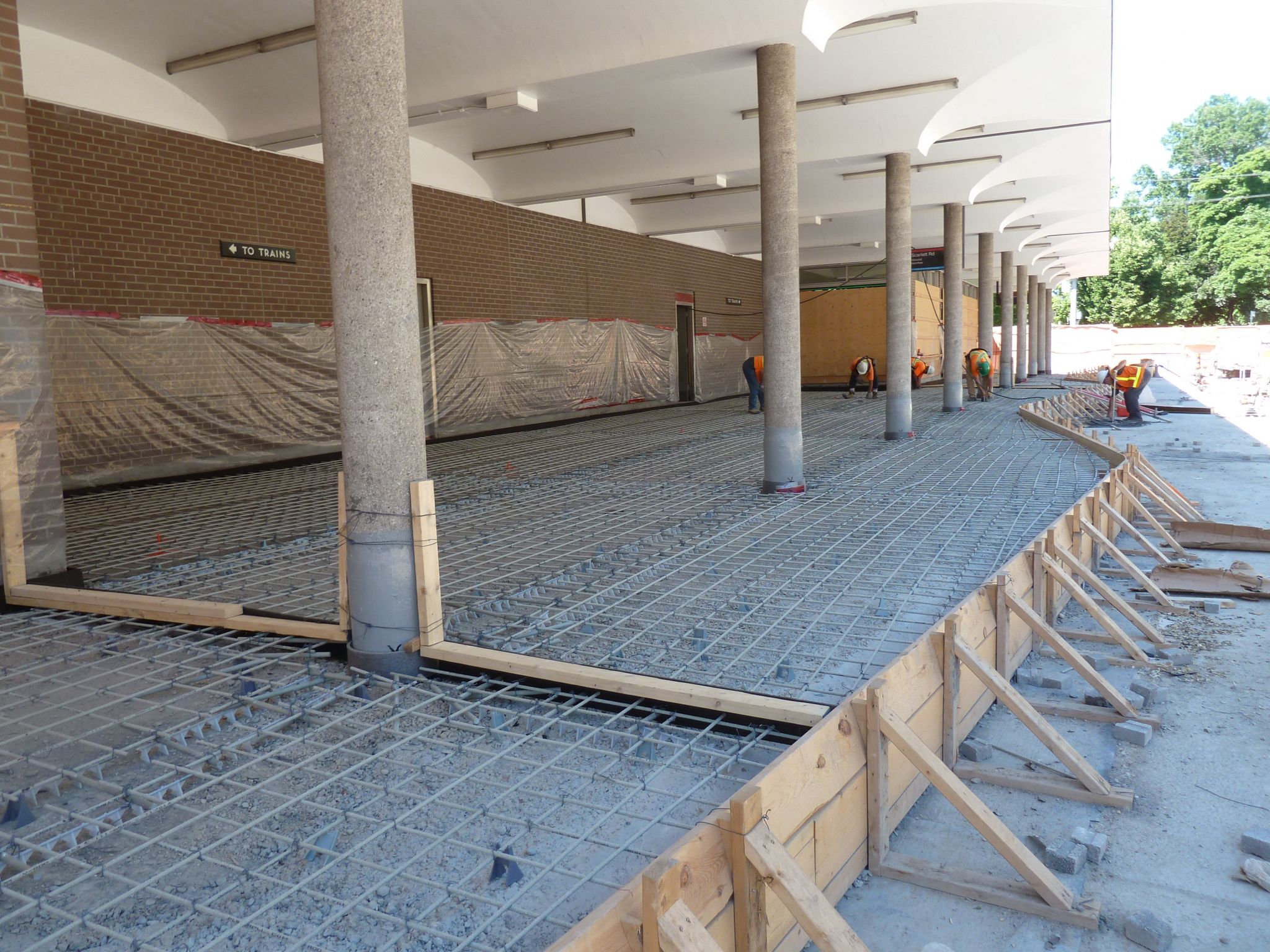
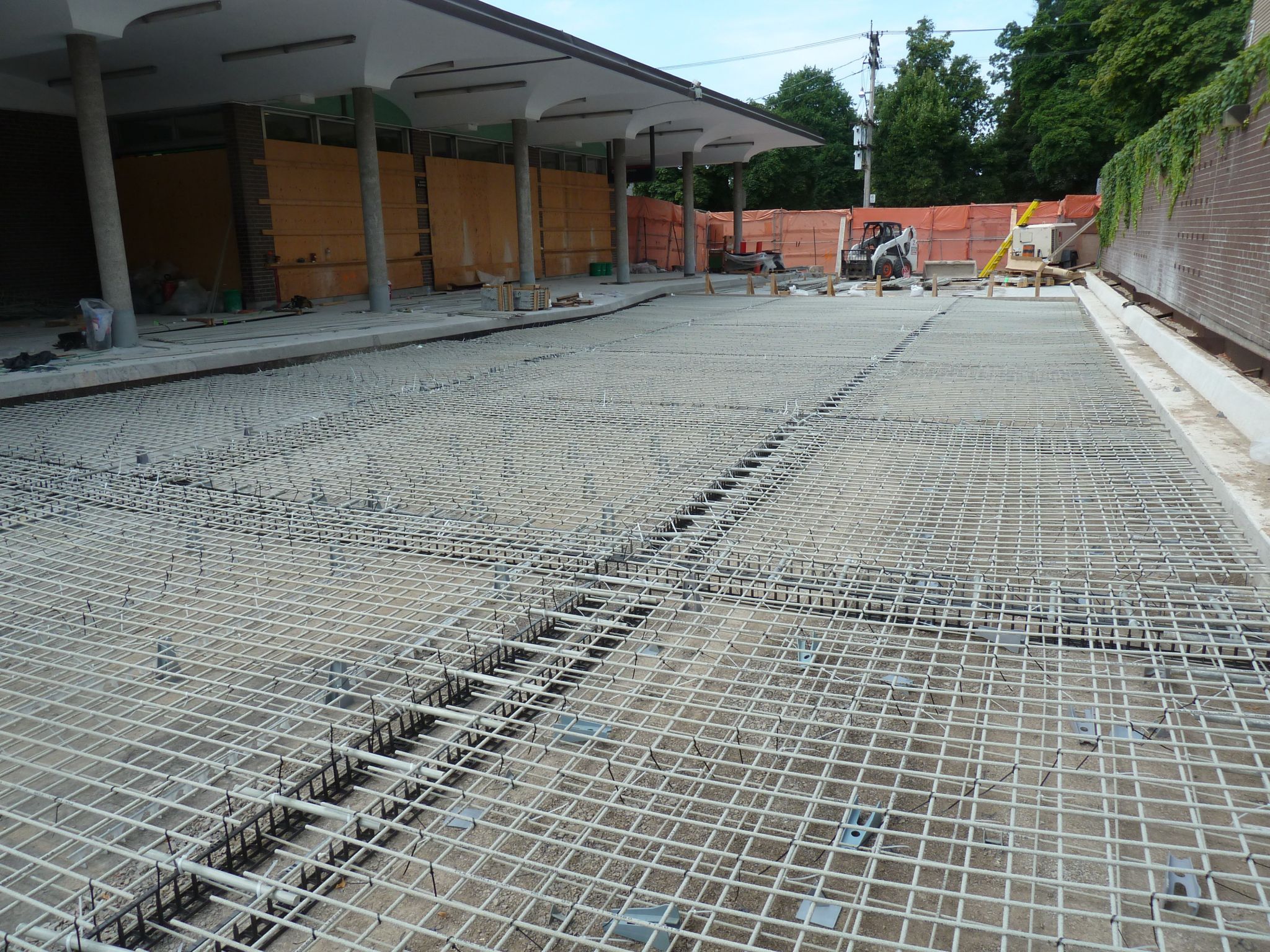
Recommended rehabilitation scheme
Based on the assessment of the investigated options, the recommended (and executed) rehabilitation scheme is outlined in the following paragraphs.
Mezzanine roof slab under the bus driveway
The alternative of constructing a new slab while keeping the existing slab in place was accomplished by:
- Shoring installation under the slab and concrete removal of the existing slab at designated support lines (without damaging existing reinforcing steel bars).
- Placing new concrete for the new slab bearing at the previously removed concrete locations (including new reinforcement).
- Placement of EPS sheets, as a compressible separation material, over the entire top surface of the existing slab, except at the support lines.
- Reinforcement installation for the new slab.
- Concrete placement and removal of shoring after concrete curing.
Column bases
It was decided the columns should be wrapped with carbon FRP (CFRP) fabric and painted to match the original collar. The concrete’s exposed surface within the height of the original, removed, collar was sand-blasted and prepared as per applicable CSA standards and the FRP manufacturer’s specifications before fabric-wrapping.
Driveway and platform
GFRP was selected for the entire concrete reinforcement (bars and dowels). Early strength concrete was specified for most of the project’s concrete work as another tool to save time. The construction zone was re-opened for both vehicular and pedestrian traffic just a few days after the last phase of concrete placement for the bus driveway. The completed works have been in service for about a year.
Conclusion
With much of Canadian infrastructure due for major rehabilitation, innovative options must be considered to meet schedule, construction costs, and other criteria such as minimizing inconvenience to the public. This project demonstrates it is possible to replace a key structural element while maintaining the original element, thereby significantly reducing service disruption. Further, fibre-reinforced polymer rehabilitation systems and reinforcement can improve the esthetics, durability, and performance of structural components and considerably increase time to the next structural rehabilitation.
Sameh Salib, PhD, P.Eng., BDS, PE, is a senior structural engineer at Delcan Corp., in Markham, Ont. For more than two decades, he has been working in both consulting and research on various issues of structural engineering, including fibre-reinforced polymers (FRPs) and soil-structure interaction (SSI). Salib is an adjunct professor at Toronto’s Ryerson University, and a member of the Canadian Highway Bridge Design Code (CHBDC) technical sub-committee for Chapter 7, “Buried Structures.” He can be reached via e-mail at s.salib@delcan.com.
Jonathan Werner, M.A.Sc., P.Eng, is a senior principal and division manager of the Structures Group in the Markham Office of Delcan Corp. He has more than 20 years of experience in the design and management of infrastructure projects, including bridges and below-grade structures. Werner can be contacted at j.werner@delcan.com.