Low-impact Development: Concrete options for porous pavements
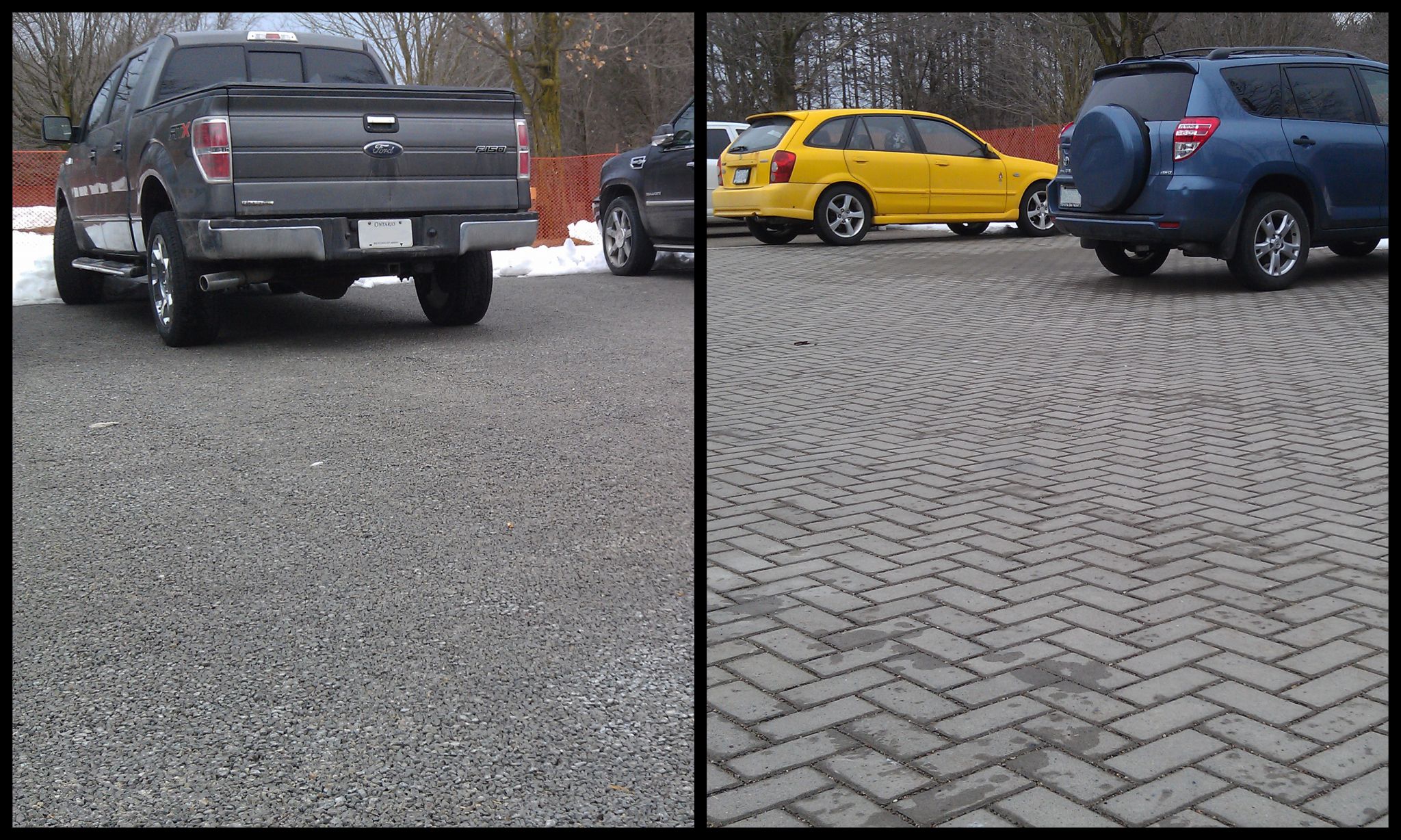
By Sherry Sullivan, P.Eng, MASc., LEED AP, and Robert Bowers, P.Eng.
Urban development significantly alters the natural landscape of Canadian communities, creating hardscape surfaces that prevent infiltration of water into soil surfaces and the subsequent increased runoff (Figure 1).1 These impervious surfaces disrupt rainwater from soaking into the ground, causing it to run across parking lots and streets, where it collects used motor oil, pesticides, fertilizers, and other pollutants on its way to local streams.
This stormwater is generally much warmer than the streams into which it flows. This is a problem because a sudden burst of runoff from a rainstorm (with a temperature increase of just one or two degrees that lowers the levels of oxygen in the water) can stress or kill fish and other aquatic organisms.2
By implementing low-impact development (LID) strategies in our communities, urban development can be managed in a more sustainable manner. LID strives to address stormwater issues at its source rather than moving stormwater offsite though a conveyance system. The overarching goal is to restore the natural ability of an urban site to absorb stormwater. This can be done simply and effectively by using a range of economical devices that control runoff at the source, including porous pavements.3
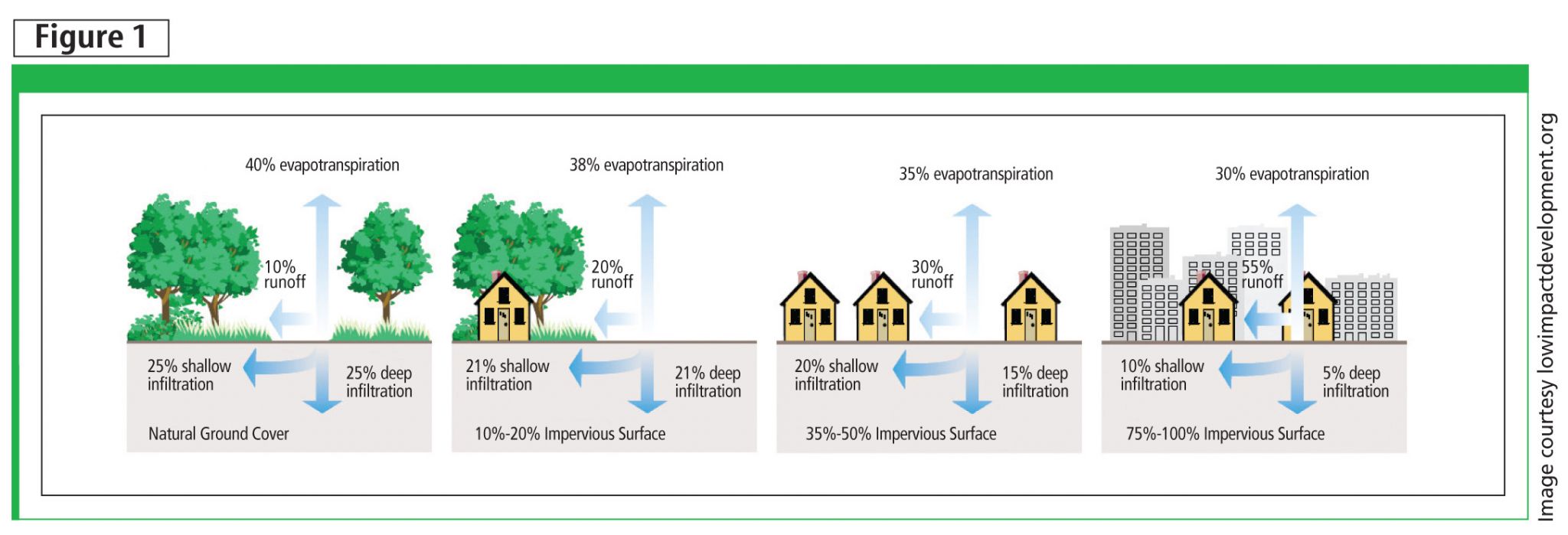
A porous pavement is one with porosity and permeability high enough to allow water to readily pass through and significantly influence hydrology, rooting habitat, and other environmental factors. Porous concrete pavements can be permeable interlocking concrete paving systems (PICP) or pervious concrete pavements (PCP).
Permeable interlocking concrete pavement is manufactured in a factory and delivered and assembled onsite. In contrast, pervious concrete pavements are supplied in a plastic state and formed at the project’s location. The different cross-sections can be seen in Figure 2. Both systems are recognized by stormwater and transportation agencies as a Best Management Practice (BMP) and LID tool to reduce stormwater runoff and water pollution.
Before delving into options for porous pavements, it is important to have a basic understanding of the materials comprising the two major system types to see the similarities and differences. All aggregate gradations noted in this article come from ASTM D488, Standard Classification for Sizes of Aggregate for Road and Bridge Construction.
Materials for PICP
Regardless of the PICP system’s purpose, the type of materials used will be similar. These materials can be seen in Figure 3.
Concrete pavers
These assemblies include solid concrete pavers with moulded joints and/or openings that create an open area across the pavement surface. Concrete pavers should conform to Canadian Standards Association (CSA) A231.2, Precast Concrete Pavers. Pavers are typically a minimum of 80 mm (3 1/8 in.) thick for vehicular areas, and pedestrian areas may use 60-mm (2 3/8-in.) thick units. Pavers are manufactured in a range of shapes and colours. Filled with permeable joint material, the openings allow water from storm events to freely infiltrate through the pavement surface.
Permeable joint material
The joint material typically consists of ASTM No. 8, 89 or 9 stone. The permeable joints allow stormwater to infiltrate through joints in the pavement surface.
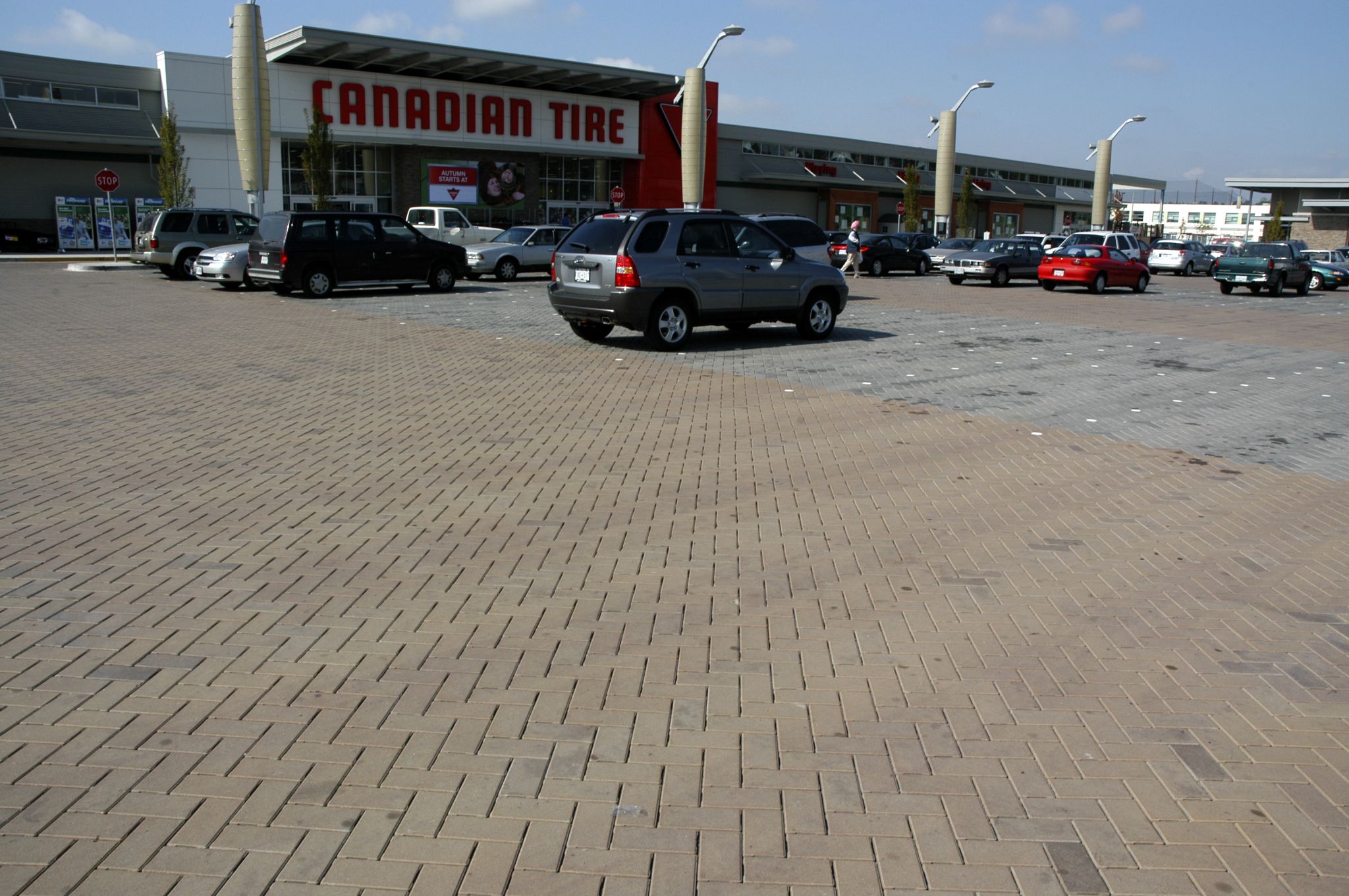
Open-graded bedding course
This permeable layer is typically 50 mm (2 in.) thick and provides a setting bed for the pavers. It consists of small-sized, open-graded angular aggregate, typically ASTM No. 8 stone or similar-sized material.
Open-graded base reservoir
This is an aggregate layer that is typically 100 mm (4 in.) thick. The base material is primarily made of crushed 25 to 13-mm (1 to ½-in.) stones, typically ASTM No. 57 stone. For pedestrian applications, the base layer is a minimum of 150 mm (6 in.) and the subbase may be omitted. Besides providing water storage capacity in the spaces among the stones, this highly permeable material also serves as a choking layer between the bedding and subbase layers.
Open-graded subbase reservoir
The stone sizes are larger than the base, primarily 75 to 50 mm (3 to 2 in.), typically ASTM No. 2, 3, or 4 stone. Like the base layer, water is stored in the spaces between the stones. The subbase layer thickness depends on water storage requirements and traffic loads. A subbase layer may not be required in pedestrian or residential driveway applications. In such instances, the base layer thickness is increased to provide water storage and support.
Underdrain (as required)
Where PICP is installed over low-infiltration soils, underdrains facilitate water removal from the base and subbase. These underdrains are perforated pipes draining to a swale or stream, or connecting to an outlet structure. They can also connect to plastic or concrete vaults or infiltration galleries, storing significant amounts of stormwater. The outflow is typically raised to leave some water in the subbase to infiltrate into the subgrade.
Geotextile
This functions primarily as a separation material between the subbase and subgrade by preventing soil migration into the aggregate subbase or base. Geotextiles are required along the sides of most PICP applications. The engineer may also choose to place geotextile across the bottom of the system.
Subgrade soil
This is the layer of soil immediately beneath the aggregate base or subbase. The infiltration rate of the saturated subgrade determines how much water can exfiltrate from the aggregate into the underlying soils. The subgrade soil is generally not compacted, as this can substantially reduce soil infiltration. However, some poorly draining clay soils are often compacted to help ensure structural stability especially when saturated. Since compaction reduces infiltration, managing the excess water must be considered in the hydrologic design via the base/subbase thickness and use of perforated pipe underdrains.
Pervious concrete pavement materials
The PCP system uses similar base material and construction details as the PICP assembly. The pervious concrete surface layer is unique to PCP, and its constituent materials are discussed in the following subsections.
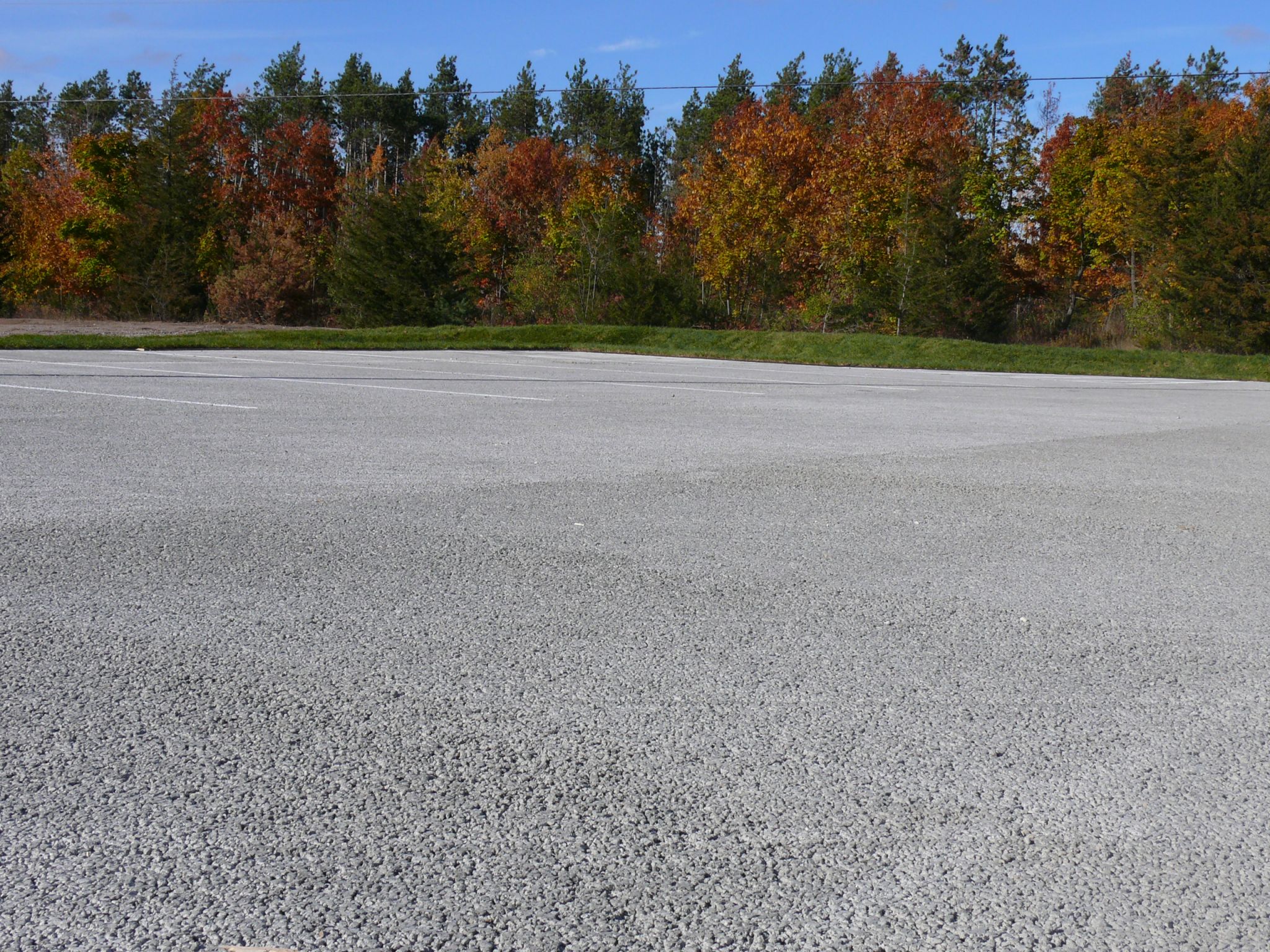
Cementitious materials
As with traditional concrete pavements, portland cements and blended cements may be used in pervious concrete. In addition, supplementary cementitious materials (SCMs) such as fly ash and ground-granulated blast-furnace slag may be used.
Aggregate
In pervious concrete, the amount of fine aggregate used is limited and the coarse aggregate is kept to a narrow gradation. Different aggregate sizes can be used to create different surface textures.
Water
Typical water-to-cementitious materials (w/cm) ratios are between 0.27 and 0.30. Ratios as high as 0.40 have been used successfully.
Chemical admixtures
Chemical admixtures—such as set retarders or hydration-stabilizing admixtures—are commonly used to combat the rapid setting time associated with pervious concrete.
Porous concrete pavement options
Two factors determine the design thickness of both PCP and PICP pavements:
- hydraulic properties, such as permeability and volume of voids; and
- mechanical properties, such as strength and stiffness.
These pavement systems must be designed to support the intended traffic load and contribute positively to the site-specific stormwater management strategy. The designer selects the appropriate material properties, pavement system thickness, and other characteristics needed to simultaneously meet the hydrological requirements and anticipated traffic loads. Separate analyses are required for both the hydraulic and structural requirements, and the larger of the two values for pavement system thickness will determine the final design thickness. To develop the required pavement system thickness, PICP will vary the subbase thickness, whereas PCP can vary the thickness of the concrete and the subbase.
PICP and PCP can be built with the purpose of full, partial, or no exfiltration of the open-graded stone base into the soil subgrade depending on the objectives of the project and site constraints. Silt and clay soils are considered to be ‘low-permeable,’ whereas sand and gravel soils are considered to be ‘highly permeable.’ Determining when a full exfiltration or partial exfiltration system is based on the subgrade’s ability to absorb the design storm event within 48 to 72 hours. If the water cannot be absorbed in that period, a partial exfiltration design utilizing subdrains should be considered. Allowing the collected water to saturate the subgrade for longer will risk weakening the subgrades.
The aggregate base/subbase used in porous concrete applications is non-frost-susceptible and itself does not suffer from the effects of frost heave. Research has also demonstrated frost penetration beneath the pavement is less than other pavement systems and is attributed to the heat-insulating effect of air in the pavement and moisture in the base course, which increases the latent heat available.4
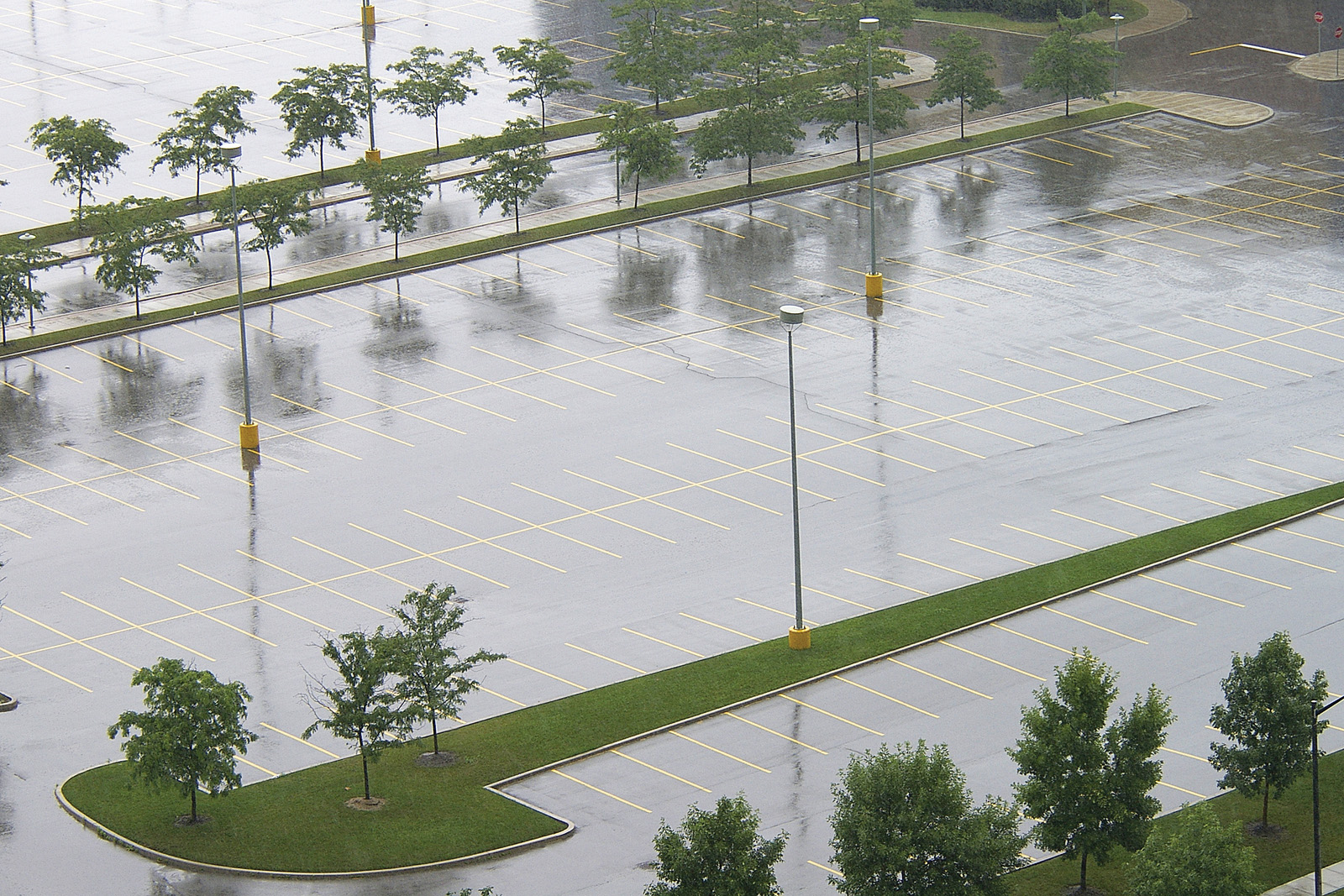
Full exfiltration
Directing all water through the base/subbase and exfiltrating it to the soil subgrade is the most common application over high-infiltration soils such as gravels and sands. Overflows are managed via perimeter drains to swales, bio-retention areas, or storm sewer inlets. An under drain could be included as a way to manage overflow drainage that would otherwise be runoff from the surface.
Partial exfiltration
This method relies on drainage of the base/subbase into the subgrade soil and drainage pipes to direct excess water to a sewer, daylight, or a stream. It controls the amount of time the subgrade is saturated. This design is common to lower infiltration rate soils such as silts and clays. The outflow from the drain pipes are typically raised above the soil subgrade to allow some water capture and infiltration into the soil subgrade. Water is typically detained for only 24 to 48 hours. Soils with infiltration rates as low as 7 x 10-6 cm/sec (0.01 in./hr) can infiltrate about 13 mm (1/2 in.) over 48 hours. Therefore, this approach can be used in some clay soils.
No exfiltration
This strategy is required when the soil has very low permeability or strength, or there are other site limitations. The assembly is a detention pond with an outlet. An impermeable geomembrane may be used when the pollutant loads are expected to exceed the capacity of the base/subbase and soil subgrade to treat them. The geomembrane can be high-density polyethylene (HDPE), ethylene propylene diene monomer (EPDM), polyvinyl chloride (PVC), or another similar material. Geomembranes typically require a non-woven geotextile for additional protection during aggregate filling and compaction. No-exfiltration strategies are also used for creating a reservoir for water harvesting or horizontal ground source heat pumps that augment nearby building heating and cooling needs.
Further resources for design, construction, and maintenance
PICP and PCP offer unique design opportunities for addressing overloaded stormwater infrastructure with environmentally responsible alleys and streets, parking lots, and pedestrian surfaces. Traditional stormwater management solutions focus on collecting, concentrating, and centralizing the disposal of stormwater. Both PICP and PCP are key BMP and LID tools helping disconnect, decentralize and more widely distribute runoff through infiltration, detention, filtering, and treatment.
Permeable interlocking concrete pavement
The Interlocking Concrete Pavement Institute (ICPI) provides several tools for the design, specification, and construction of PICP. This includes the comprehensive, 92-page manual, Permeable Interlocking Concrete Pavements, which provides extensive information from academic research and practical field experience. A Tech Spec bulletin for contractors and inspectors is also available to provide a summary of construction techniques outlined in the manual, as well as further guidance on best construction practices. Another popular tool is the PICP Permeable Design Pro software, which evaluates the structural and hydrologic performance of a PICP system subject to model storm events.5
Pervious concrete pavement
The University of Waterloo has developed a guide for the design, construction, and maintenance of pervious concrete pavement in Canada, based on a cross-Canada multiyear study. This was developed in partnership between the Cement Association of Canada (CAC) and the Centre for Pavement and Transportation Technology (CPATT) at the University of Waterloo, along with various industry members. This guide incorporates best practices from both existing literature and the results of this cross-Canada study. Recommendations have been provided for the following areas:
- design (i.e. application, pavement structure, and mix design);
- construction (i.e. constructability and staging, construction methods, curing, joints, and testing);
- warm- and cold-weather maintenance (including distress maintenance); and
- project examples.
The study shows pervious concrete pavements can be successfully designed and constructed in Canada following the presented best practices.6
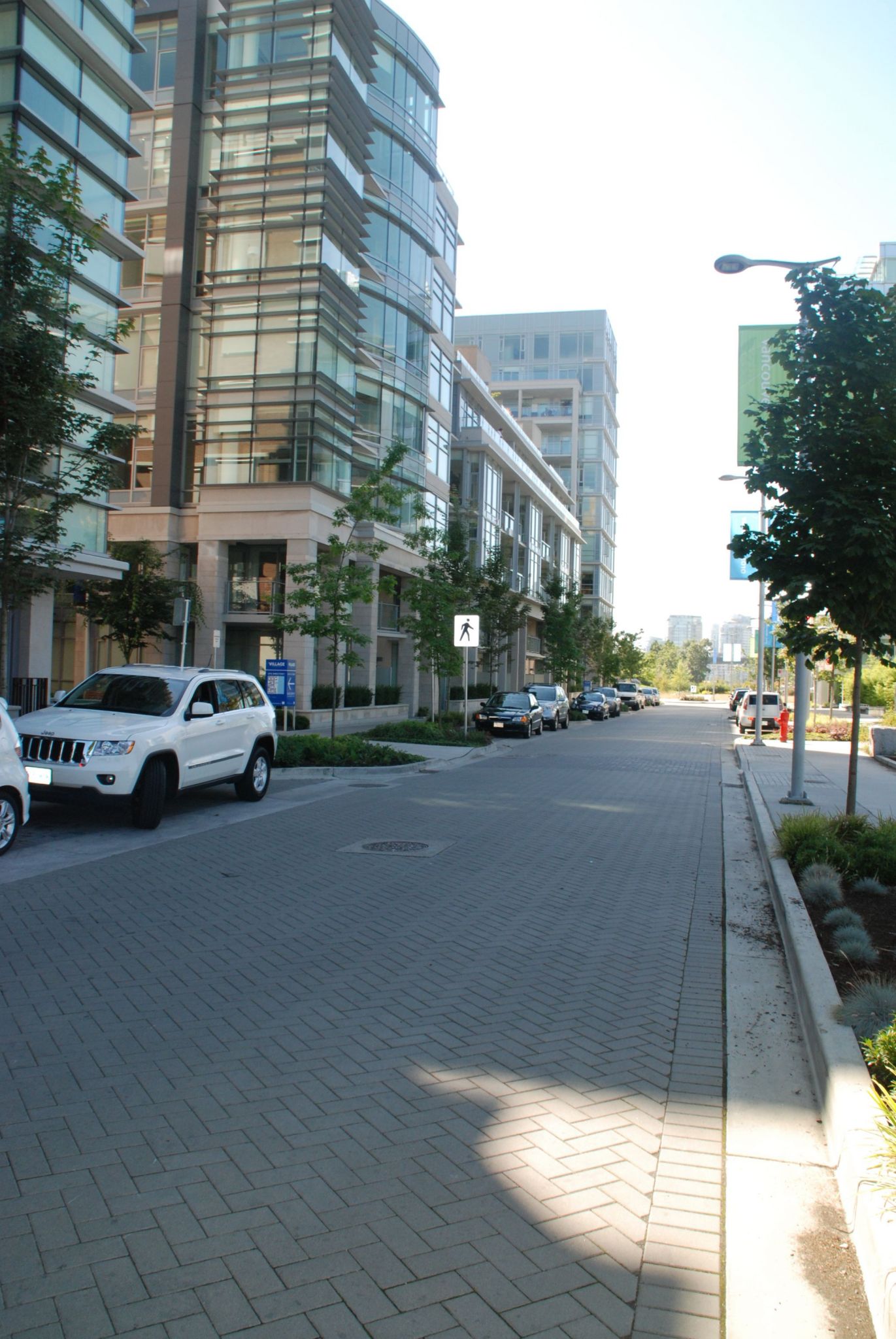
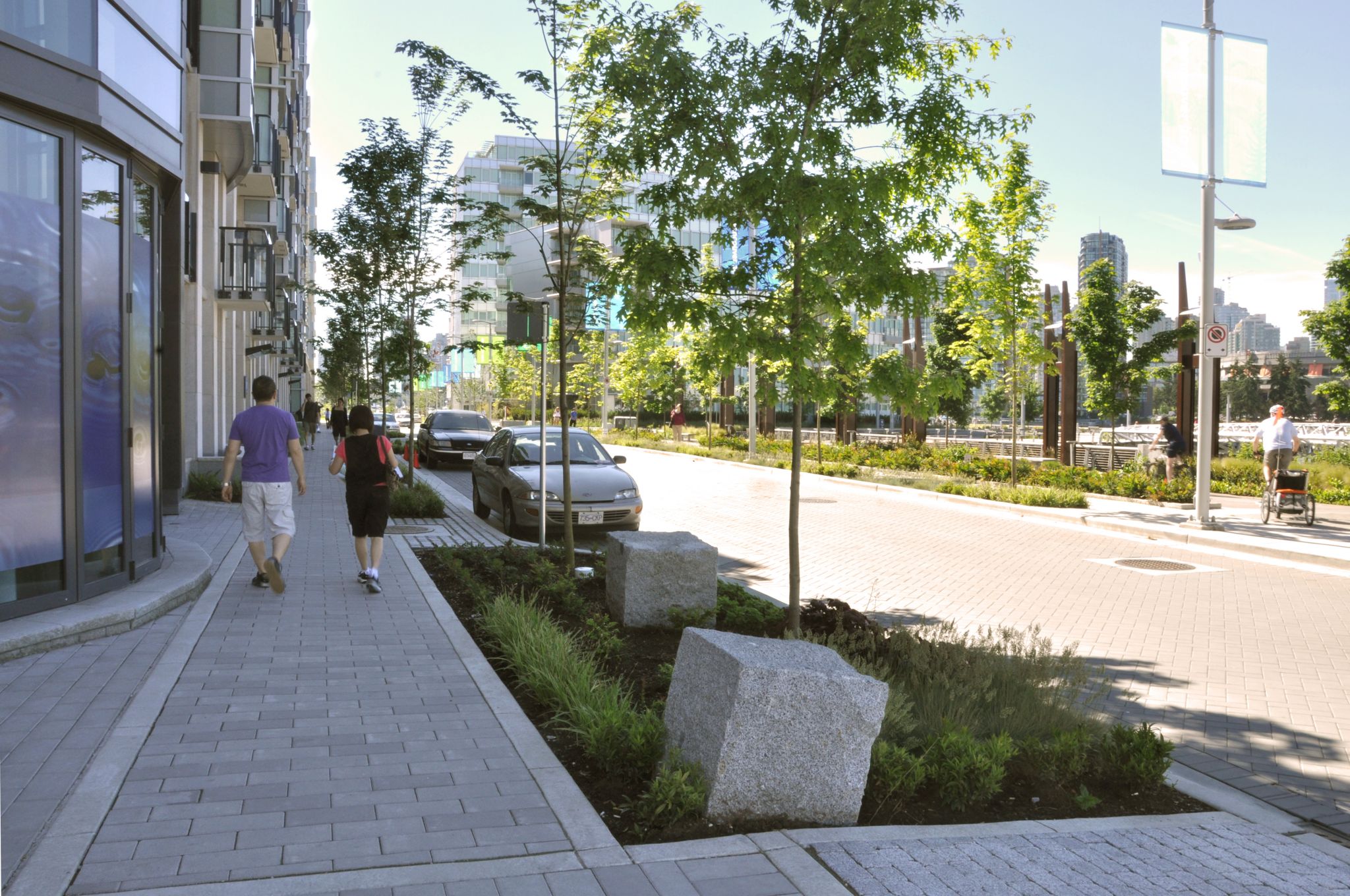
Conclusion
The way Canadian design/construction/planning professionals currently develop in urban areas significantly alters the natural landscape. Porous concrete pavement—whether permeable interlocking concrete or pervious concrete—is a proven solution to provide low-impact development, restoring the natural ability of an urban site to absorb stormwater.
Notes
1 For more, see the Federal Interagency Stream Restoration Working Group’s (FISRWG’s) Stream Corridor Restoration: Principles, Processes, and Practices (PB98-158348LUW). (back to top)
2 Visit www.newjerseynewsroom.com/science-updates/fish-kill-in-delaware-bay-still-a-mystery-to-nj-dep. (back to top)
3 Visit cfpub.epa.gov/npdes/stormwater/menuofbmps/index.cfm. (back to top)
4 Visit www.icpi.org. (back to top)
5 This information comes from the University of Waterloo’s Centre for Pavement and Transportation Technology (CPATT) and its 2013 Design, Construction and Maintenance of Pervious Concrete Pavement in Canada. Visit www.cement.ca. (back to top)
6 For more, see the November 2008 report, “Performance Evaluation of Permeable Pavement and a Bioretention Swale, Seneca College, King City, Ontario,” by Tim Van Seters of the Toronto and Region Conservation (TRCA). See also the December 2012 report, “Evaluation of Permeable Pavements in Cold Climates: Kortright Centre, Vaughan,” by Jennifer Drake and Andrea Bradford (University of Guelph, School of Engineering) and Tim Van Seters and Glenn MacMillan (TRCA). (back to top)
Sherry Sullivan, P.Eng., MASc, LEED AP, is the director of transportation and built Environment for the Cement Association of Canada (CAC). Sullivan has over a decade of experience in the cement/concrete industry, previously working as a concrete engineer with the Ready Mixed Concrete Association of Ontario (RMCAO) and a technical services representative for St. Marys Cement in Ontario. She is an experienced examiner of the National Ready Mixed Concrete Association (NRMCA) Pervious Concrete Contractor certification course, and plans to host courses in Alberta, Saskatchewan, and Manitoba in 2013/2014. Sullivan can be contacted at ssullivan@cement.ca.
Robert Bowers, P.Eng., is the director of engineering for the Interlocking Concrete Pavement Institute (ICPI), and has more than 20 years of experience in the hardscapes industry. He is responsible for ICPI programs directly related to the installation of interlocking concrete pavers, including the Installer Development Program and the development and delivery of technical installation materials. Bowers chairs the Canadian Standards Association (CSA) A231 Committee, which is responsible for the development of the standards for concrete pavers and slabs. He can be reached at rbowers@icpi.org.
To read about pervious concrete for the Evergreen Brickworks, click here.
To read about pervious concrete for Marine Way, click here.