Garage Traffic Toppings: A tale of two systems
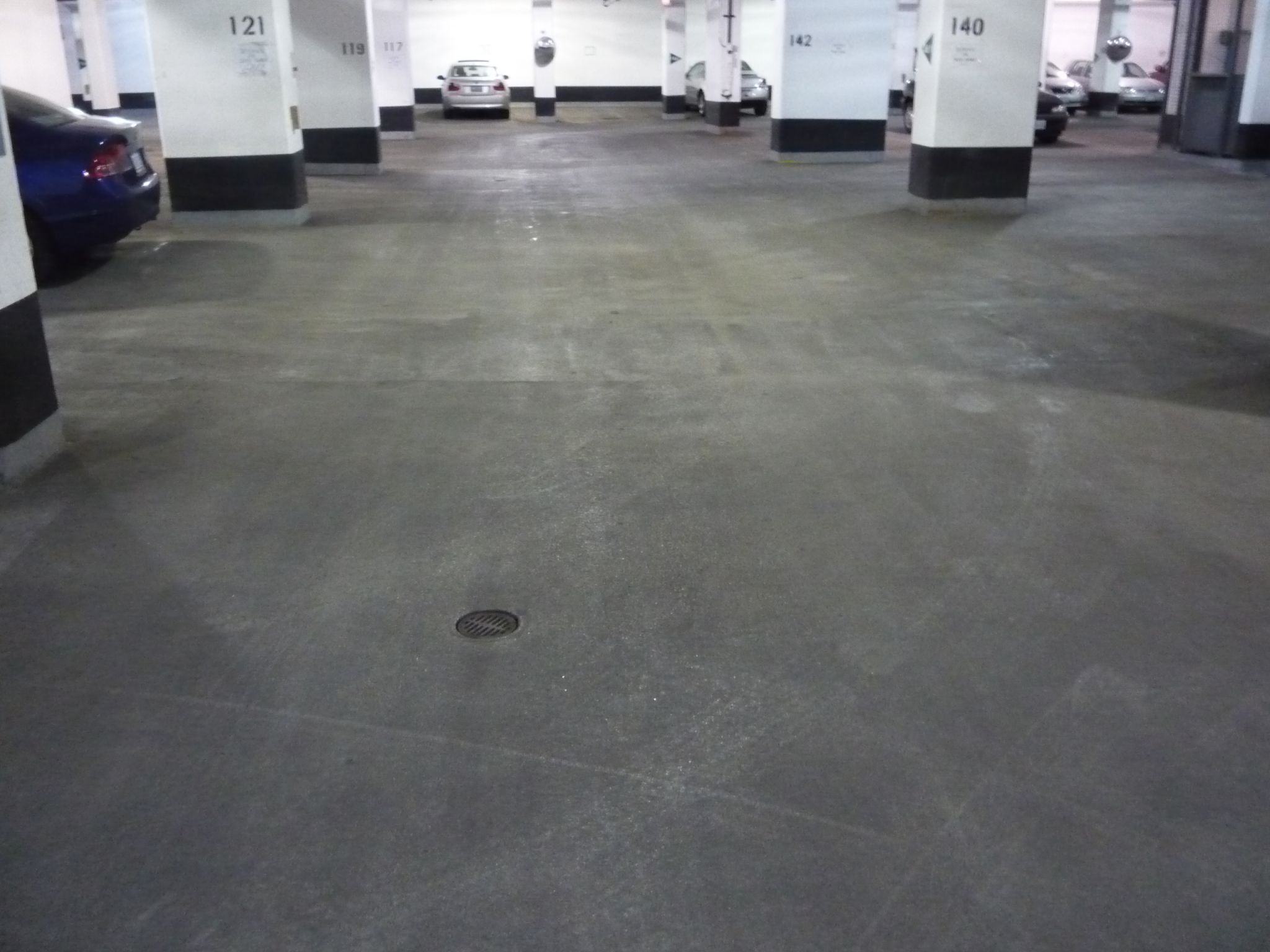
By David Uren, P.Eng.
Traffic topping systems for suspended concrete slabs found in parking garages come in two basic types: ‘thin’ and ‘thick.’ (While these are unofficial ‘categories,’ they are nonetheless fitting.) This article reviews both variations, outlining the physical properties and noting differences in terms of performance, design, cost, lifecycle, and maintenance. With this information, architects, engineers, and specifiers should be better able to help their clients evaluate the options and chose the most appropriate system for their particular parking garage.
The basic function of a garage traffic topping system is to protect the underlying structure from water, which can cause corrosion or other types of damage. Garage systems also have to resist attack from chemical fluids such as gas or oils that may leak from poorly maintained vehicles.
In Canada’s cold climate, the traffic topping system also protects against de-icing products carried into the garage from vehicles. These chemicals are a particular enemy of the reinforcing steel embedded in the concrete. When the chemicals reach the level of the steel, the material corrodes and expands, causing the concrete to crack. This leads to concrete deterioration and, if left alone, can result in serious safety concerns.
Unlike roof systems, which also protect from water, but simply lie atop the structure, garage traffic toppings have to stand up to vehicle traffic. Therefore, it is essential the system have performance characteristics to resist loading, shearing forces, and abrasion. Otherwise, it will tear up in no time.
Through thin and thick
Thin systems generally comprise elastomeric traffic toppings with an overall thickness less than 2 mm (80 mils). Thick systems, on the other hand, traditionally employ asphaltic traffic toppings and will have a total system thickness ranging between 12 and 33 mm (15/32 and 2 19/64 in.)—six to 16 times thicker than the thin system.
Thin
Most traffic toppings have two constituent layers to achieve required performance qualities—a flexible waterproofing layer and a protective wear course that will stand up to traffic. In thin elastomeric systems, the flexible waterproofing layer adheres to the concrete. It is then protected with a thin abrasion-resistant top wear course that is adhered to the waterproofing providing an integral system (Figure 1).
In these systems, the waterproofing layer has a minimum thickness typically between 0.75 to 1 mm (30 to 40 mils), and the wear course is between 0.25 to 0.5 mm (10 to 20 mils) thick, depending on the manufacturer’s requirements. An aggregate is integrated into the wear course to provide a slip-resistant surface. Numerous manufacturers provide this type of product, and most systems are urethane-based.
Thick
Thick asphaltic systems have the same two layers, but both are much thicker. The flexible waterproofing layer is typically a hot-applied rubberized asphalt 2 to 3 mm (40 to 120 mils) thick, and the wear course layer is a bonded asphalt or mastic asphalt pavement. When an asphalt pavement wear course is used, it is typically 30 mm (1 3/16 in.), as shown in Figure 2. Mastic asphalt provides a denser and less porous layer than regular asphalt, so a thinner wear course layer can be used, typically 10 to 15 mm (25/64 to 19/32 in.), as shown in Figure 3.
Performance considerations
A key performance requirement of a garage traffic topping system is the waterproofing membrane’s ability to bond to the concrete slab. One of the pathways for salt-laden water to reach reinforcing steel is through cracks in the concrete. Cracking from concrete shrinkage is inevitable, so the waterproofing membrane needs to be good at bridging cracks; it must also be properly detailed at joints allowing for expansion and contraction within the structure.
When it comes to bridging cracks in concrete, thick asphalt-based systems are generally superior because of the rubberized membranes’ flexibility. Thin elastomeric systems can effectively bridge minor cracks (i.e. < 1.5 mm [60 mils]), but they do not perform as well when dealing with wider cracks (i.e. > 1.5 mm) or those that move significantly.
Given elastomeric systems are thin, they wear sooner in the high-traffic-drive aisles, ramps, and sharp turn areas. To address this, the wear course at these areas is applied at double or triple the thickness than in the parking stalls. It may also have a coarser aggregate.
Asphaltic systems do not exhibit the same level of wear or thinning, but they are not invulnerable when it comes to vehicle traffic. Asphaltic systems, particularly mastic, are susceptible to tire shears when wheels are turned on the spot (Figure 4). This is often seen in parking stalls where drivers do fine manoeuvres to straighten their cars.
Additionally, asphaltic systems are more susceptible to damage from vehicle fluid leaks or spills. Gas spills in particular will soften the asphalt or mastic, weakening the wear course. Vehicle leaks are typically more problematic in garages where there is assigned parking because the cars are in the same spot day in and day out, causing fluids to accumulate. Issues with vehicle leaks should be less frequent in public parking garages serving retail or assembly occupancies.
Design choices
Specifiers, architects, and engineers choosing between elastomeric and asphaltic toppings must consider the parking garage’s overall design. For example, thin elastomeric systems do not add any significant load to the structure. The thicker asphaltic system, however, is heavier and generally increases the load on the slab by about 0.5 to 0.75 kPa (10 to 15 psf).
Door transitions—and other areas where the slab meets a different floor surface—must also be considered when applying a thick system, as the finished floor elevation will be significantly higher than the slab elevation.
Colour is another factor to consider. The black colour of asphaltic systems is light-absorbing and reduces effective light levels. If an asphaltic system was not considered in the design or is being used to replace a non-asphaltic system, it may be necessary to add lighting fixtures to maintain appropriate illumination levels.
In comparison, elastomeric systems are available in a wider selection of colours, with shades ranging from light to dark grey. Applying a topping system in a lighter shade can make a garage appear brighter overall, without changing the actual lighting system. Elastomeric systems also come in customized colours, including blues and greens that may suit a building owner’s particular design needs.
Consideration must be given to the potential for ultraviolet (UV) exposure. Certain manufacturers of thin elastomeric systems provide special UV-stable formulations or require the application of an additional UV-resistant top coat. (This would be typical for an open-air structure.) Further, depending on the climate and design, snowplowing may be needed on, for example, rooftop parking. Regular use of plows can physically damage a thin elastomeric system.
Cost, lifecycle, and maintenance
When installation and maintenance costs are taken into account, the two systems are basically comparable. Asphaltic membranes can be more expensive to install than elastomeric systems, depending on availability. Both systems can have a range of maintenance and repair costs, based on the traffic configuration and volume in the garage.
The service life of these waterproofing systems is difficult to pin down, as it depends so highly on traffic volumes, exposure, and maintenance. Some building owners take a relaxed approach to garage upkeep, only reacting to issues if leakage through the slab begins to impact operations (e.g. dripping onto cars). In some cases, building owners defer repairs and instead install diverters/troughs to redirect the water away from the car. Other building owners take a diligent preventative maintenance approach, attending to damage to the wear course in short order to minimize the risk of water leakage and maintain full protection provided by the waterproofing system.
It is a certainty parking garage traffic topping systems will require maintenance. To maintain watertight conditions and a good driving surface, both systems require regular inspections and local repairs. With thin systems, it is necessary to locally replace or reapply the wear course more frequently at the high traffic areas over the system’s life. For high-volume commercial garages, this may be as often as every five years, but the frequency ultimately depends on the traffic. As shown in Figure 5, other areas need to be checked for debonding of the membrane (where the initial application did not provide an adequate bond to the concrete slab) and cracks (where the membrane has not been successful at bridging an underlying crack in the concrete).
Thick systems also need to be regularly inspected for tire shears and damage from vehicle leaks. Where there is damage, it will have to be addressed by local replacement of the wear course—again, how often highly depends on the amount of traffic.
A major garage repair program is required for both system types at some point over their lifetime. For elastomeric membranes, this typically includes applying a new wear course (over the existing one) at all the drive aisles and other high-traffic areas. Full replacement, including the membrane layer, would only be performed locally (where needed), as would repairs to remedy any concrete deterioration that may have occurred at breaches. For asphaltic systems, repairs would be limited to local replacement of the wear course and waterproofing, as well as any necessary concrete repairs. Despite the approach to maintenance, both systems can last for more than 25 years.
Summing up the evidence
Despite serving the same function and having a similar service life and lifecycle cost, the two systems present different performance issues and maintenance patterns. Neither is the perfect fit for all situations. Architects, engineers, and specifiers who ask the right questions can help their clients make more informed decisions. (See “Which Traffic Topping System is the Best Fit?”)
As with all waterproofing and coating systems, strict adherence to the manufacturer’s guidelines is essential to ensure the installation meets the performance standards to which it has been designed. Factors that can greatly influence long-term performance include:
- concrete surface preparation;
- mixing ratios;
- mixing and placement temperatures; and
- concrete moisture content.
The best way to ensure the system is applied under the right conditions and to the manufacturer’s specifications is to have a third-party reviewer provide inspection and quality control services during installation. These services should include:
- testing the moisture content of the concrete before placement;
- cutting samples of the installed material to verify it has been applied at the required thicknesses;
- and field-testing the strength of the bond to the concrete slab.
Dave Uren, P.Eng., is a project manager at Halsall Associates, a consulting engineering company with seven offices across Canada. He specializes in evaluating existing buildings and has done hundreds of property condition assessments for commercial, residential, and industrial buildings. Uren can be contacted via e-mail at duren@halsall.com.