Adhesive-applied Roofing: A Canadian reality
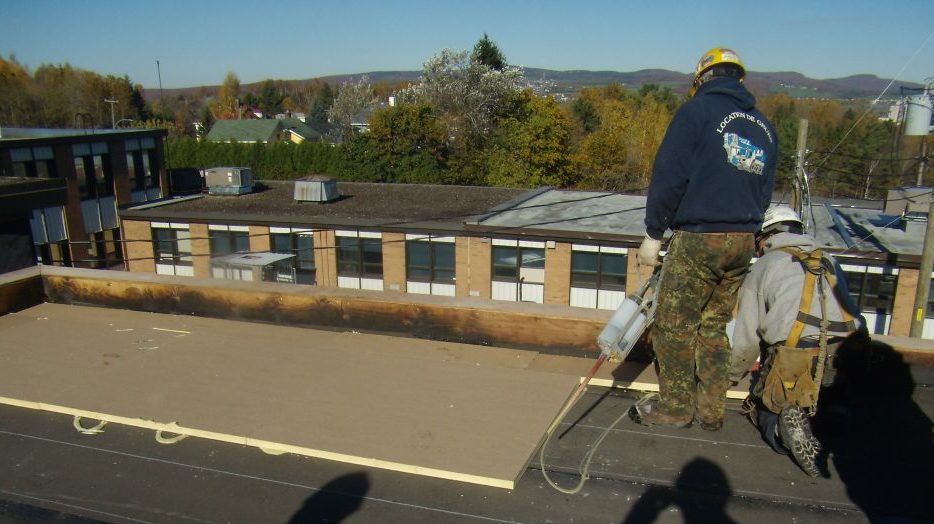
By Jean-François Côté, PhD, and Vincent Boisvert, ing., CSC
Until recently, using asphalt to adhere roofing materials was likely the most popular attachment method. It was used for everything, from vapour retarders and insulation, to the thermal barrier and cover board. Even roof membranes were bonded in asphalt—the first ply of a two-ply modified bitumen (mod-bit) roof membrane or the entire four-ply ‘tar-and-gravel’ system got their share.
Over the last 15 years, however, popularity of asphalt-adhered roofing systems has steadily declined. Odour issues, aging or obsolete equipment, difficult temperature management at point of contact (especially in winter), material brittleness, quality, and supply issues are among factors that contributed to its slow and steady decline in Canada.
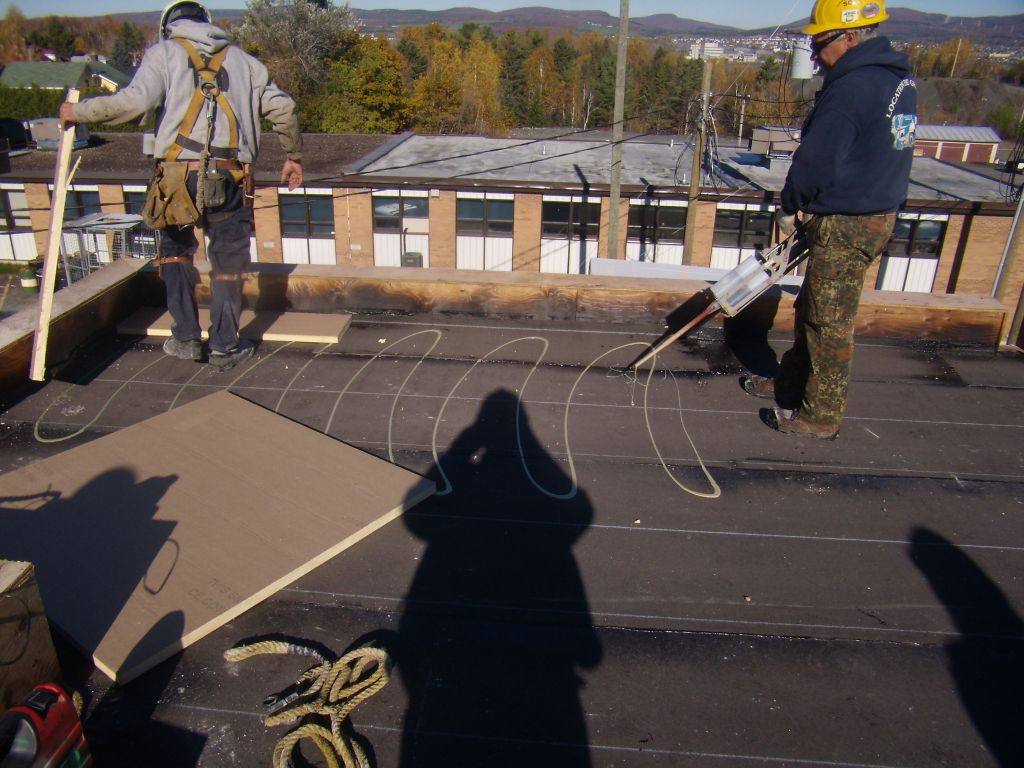
The downsides of asphalt have always been known. However, without economical and technical alternatives, the potential for change in roofing materials adhesion methods was low. Today, asphalt is still widely used in areas surrounding refineries or heavy petroleum industries, but has almost completely disappeared from remote locations, away from metropolitan areas. Fewer mod-bit roofing membranes are also adhered using asphalt. In Canada, it has never been common to mop cap sheets; at the authors’ company, mopped base sheet numbers fall by five to 10 per cent annually.
In 2009, a Construction Canada article by Yves Bradet focused on the increasing popularity of mechanically attached roofing systems (MARS) as a means to move away from mopping down roofing sheets while using an alternate installation method.1 Observations made at that time included the challenges of MARS, such as:
- thermal bridging;
- air infiltration into the roofing system caused by wind uplift; and
- fastener corrosion issues.
Although MARS bring their share of solutions, the market still requires solutions in adhered systems. Whether because the type of deck does not allow penetrations, or by choice (i.e. designer’s preference), mechanical fasteners are not always desired, and an adhered roofing system without asphalt is still a solution many are looking for.
Cold-adhered systems: a difficult genesis
Until recently, use of cold adhesives remained marginal because early versions exhibited many limitations—long cure times, odours, high volatile organic compound (VOC) content, and difficulties to adapt to extreme installation temperatures (both hot and cold).
Recent developments in the chemistry of roofing adhesives allowed asphalt-free cold-adhered systems to be significantly improved. Fully adhered roofing systems using asphalts have a long track record; therefore, recently improved cold-adhered systems cannot really be considered ‘new.’ Only the bonding material has changed.
Further, since the adhesive has been developed specifically for the application, it is expected to deliver a performance level superior to rigid and brittle asphalt. These hypotheses are found to be true when these systems are tested for wind uplift—rupture occurs rarely within the adhesive, but rather within adhered materials such as insulation facer delamination, for example.
Although fully adhered systems (mostly using asphalt) have been used for decades, wind-uplift dynamics of fastener-free roofing systems have never been studied extensively until 2008. Specification writers needed to count on past experiences combined with empirical data available from manufacturers and other sources to evaluate a roof system’s suitability. Systems installed over the years under good conditions and with known materials provided some kind of knowledge base, but it could never serve as a solid foundation for predicting the performance levels using new adhesives. These systems were sentenced to a slow growth.
Of course, Factory Mutual (FM) allowed use of adhesives for some of the roof system components. However, even today, FM does not insure any building covered with a fastener-free, adhesive-applied roof system (AARS), despite such assemblies being used throughout Canada. Writing a specification for an AARS was therefore quite a challenge that may have involved a significant level of speculation.
Research comes in support to the industry
Bridging such a gap was one of the objectives of the Special Interest Group on the Dynamic Evaluation of Roofing Systems (SIGDERS), found almost a decade ago. This program, launched and lead by researchers of the National Research Council of Canada (NRC), has benefited from the participation of most of the North American roofing industry’s stakeholders. Research has followed the industry’s technical evolution to provide an effective test protocol for all roofing systems.
Phase 1 of the program had already focused on systems where the roof membrane is mechanically attached to the deck (i.e. MARS), so such systems could be tested and rated. Phase 2 extended the research to AARS.
Numerous tests were performed within this program phase. It was demonstrated the different behaviour of AARS when compared to MARS (i.e. the latter may significantly billow between rows of fasteners when the system is subjected to wind loads, which is not the case of AARS) required two distinct test sequences to be developed
At the end of the second phase, results were validated by SIGDERS, as members prepared a request for revision of the Canadian Standards Association (CSA) A123.21, Standard Test Method for the Dynamic Wind Uplift Resistance of Membrane-roofing Systems, asking the CSA A123 Technical Committee on Bituminous Roofing Materials to include a test sequence specific to AARS. In 2010, the standard was updated, and it is now possible to measure the resistance of an AARS to wind uplift using a test protocol adapted to these systems.
It is the manufacturers’ responsibility to have their systems evaluated as per the dynamic CSA protocol in an independent third-party laboratory. The test is performed on a system, installed on the laboratory table just as if it was installed on the actual roof. A retractable dome, connected to a vacuum pump, is then placed on the roofing system equipped with pressure gauges. Air is pumped out of the dome to create a vacuum atop the system as per the CSA protocol.
If the system has sustained the required number of cycles to levels of pressure prescribed by the standard, it is given a rating. A test report from the laboratory will contain the detailed system tested (i.e. components and installation methods) and the pressure rating to which the system was successfully exposed, with and without the safety factor, which is 1.5 for the CSA protocol (i.e. lower than FM’s safety factor of 2.0). This demonstrates the test’s severity and representation ability.
In 2013, the Standing Committee on Environmental Separation has proposed a modification to sentence 5.2.2.2 (Division B) of the National Building Code of Canada (NBC) that would add a reference to CSA A123.21 in the 2015 edition. At the time of this writing, this proposal (number 525) is undergoing the mandatory public comment period. The final decision will be known in early 2014.
The consequences for specification writers
When designing a roof, it is imperative to calculate the wind load for the building being roofed or reroofed. This calculation has been greatly simplified with use of NRC’s Wind-RCI online calculator, based on Canadian climatic data and the location and dimensions of the building.2
This tool also provides the user with a description of the roof zones considered as ‘perimeter’ and ‘corners,’ where the wind loads can be larger than in the field of the roof. This information is critical for the roofer and other people involved in the installation or the inspection of the roof.
After determining the wind loads and pressures expected to act on the building, the specification writer must find out whether the roofing system intended to be used on this building is robust enough to sustain such loads. Test reports and system ratings obtained by manufacturers through testing of their roofing systems by the CSA A123.21 standard will then be useful.
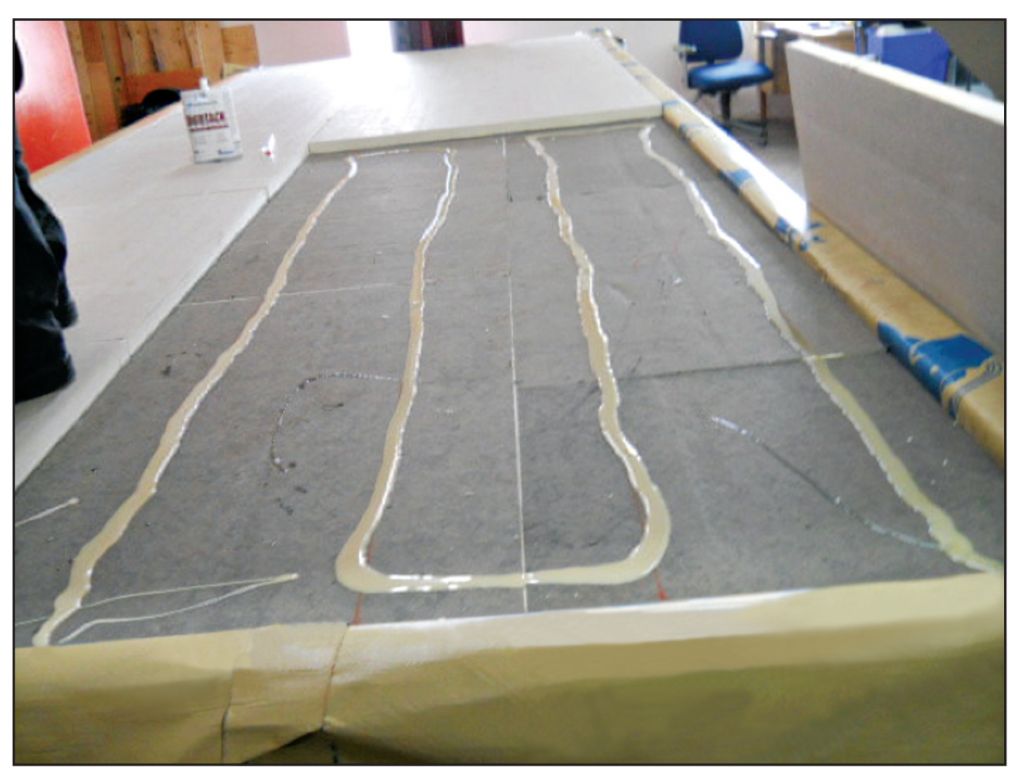
AARS greatly benefit from the use of the Wind-RCI and CSA protocol as it finally allows these systems to prove their suitability on a specific building and gives peace of mind to building professionals who have used them and continue to do so.
Wind-RCI and CSA can also make the roofing installer’s life easier. Instead of systematically requiring a prescriptive enhancement of fastener or adhesive density in the perimeter or corner zones (which can be difficult to implement and regulate), the designer can select an assembly with a rating high enough to allow its use in all zones of the roof, without requiring a modification of fastener or adhesive quantities.
The suitability of many AARS used in the Canadian market was confirmed through use of Wind-RCI and CSA, in most cases without adjustment. Some cost savings could even be realized through careful system optimizations.
AARS: here to last?
AARS have been re-engineered with the launch of new cold adhesives. Roofing assemblies can now see thermal barriers, insulation boards, and cover boards maintained in place with these products. Discontinuous bonding—mainly using ribbons—has replaced the full-bed adhesion of asphalt. Ribbon adhesion brings flexibility and speed of installation that even asphalt has a difficult time competing with, which explains why it is now so popular. However, it brings a challenge to resistance to wind uplift; pressure applied on the components adhered in a discontinuous pattern acts differently and creates a concentration of stress at the edges of the ribbons, as opposed to full adhesion where the stress is evenly distributed throughout the roof area. Cohesion of roofing materials is taken to its limit.
Even if new cold adhesives exhibit better mechanical properties and bonding qualities, there are additional reasons for which they are becoming more popular. Their improved chemistry allows for a quicker cure, usually within minutes. This behaviour brings solutions to the roofing crews who no longer need to change how they stage their work from the traditional asphalt installation.
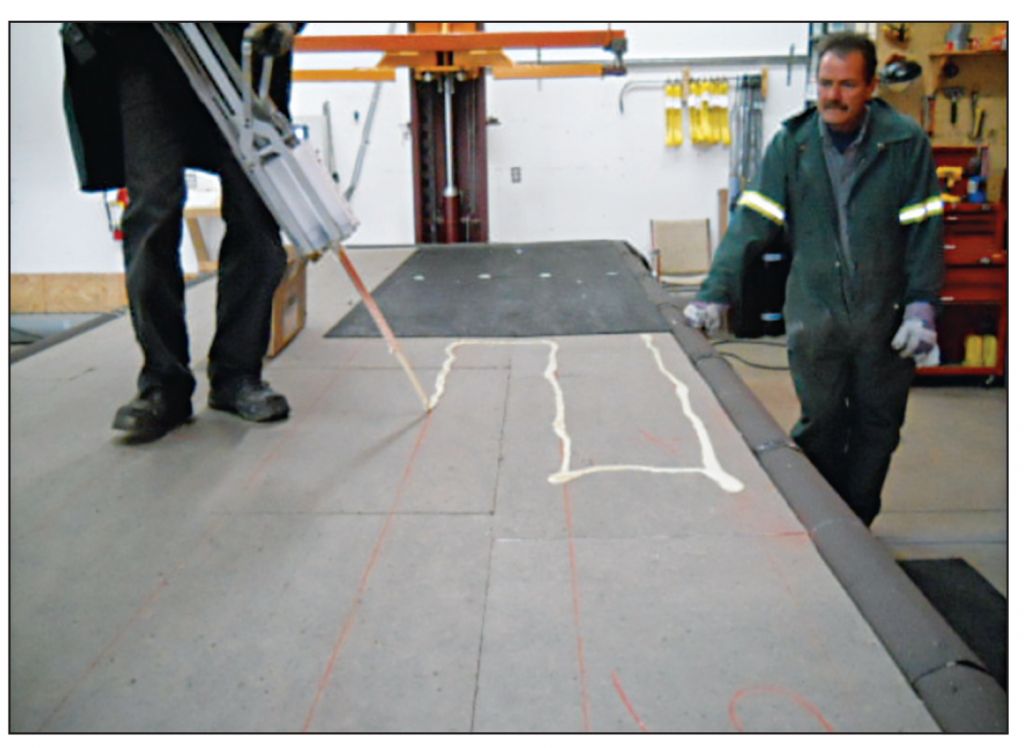
A123.21 test protocol.
This evolution of the adhesives also solved the VOC content issue that plagued former generations supposed to substitute asphalt. Today’s adhesives are either low in VOCs or VOC-free, which is a blessing for the environment and the workers who install them and eliminates risks associated with the presence of flammable solvents. They also allow roofing work to carry on later in winter, with installation temperature ranges that can go down to temperatures as low as −15 C (5 F).
Conclusion
MARS may still be preferred for large buildings such as warehouses, especially if the view of fastener tips through the steel deck is not an issue to the owner or occupants. However, today’s adhesives exhibit properties with which neither asphalt nor mechanical fasteners can compete, at a competitive cost.
These adhesives are less rigid and less brittle; they show some elastic deformation when exposed to repetitive uplift loads. Consequently, they perform well under dynamic wind uplift situations such as the CSA protocol. Some manufacturers already claim use of a significant portion of their adhesive formulations from renewable carbon sources (natural or bio-based ingredients)—a feature that goes a long way in these times of lifecycle assessment (LCA) and sustainable development. These materials, and the systems they contribute to, are significant in the Canadian roofing market and will remain for many years to come.
Notes
1 The article, “Dynamic Wind Uplift Testing: New Protocols for Roofing Assemblies,” appeared in the November 2007 issue. (back to top)
2 For more information, visit www.nrc-cnrc.gc.ca/eng/services/windrci/index.html. (back to top)
Jean-François Côté, PhD, is the director of strategic development for Soprema. He oversees the Canadian R&D and technical departments of the organization, co-ordinating activities related to product and systems development in North America. A registered chemist in Québec, he co-chairs the ASTM D08-04 Subcommittee on felts, fabrics, and bituminous sheet materials. Côté is an active member of Asphalt Roofing Manufacturers Association (ARMA), Single-ply Roofing Industry (SPRI), Canadian Standards Association (CSA), and Underwriters Laboratories of Canada (ULC). He can be reached at jfcote@soprema.ca.
Vincent Boisvert, ing., CSC, is the director of Soprema’s technical department, co-ordinating activities related to products and systems certifications and to the development of training programs for the installation of the company’s products. He is a registered engineer in the province of Québec (OIQ) and is an active member of the (SIGDERS) group. Boisvert is also an affiliate member of CSC, RCI, and the Canadian Roofing Contractors Association (CRCA). He can be contacted at vboisvert@soprema.ca.